In 1995, after graduating from the College for Creative Studies with a degree in industrial and product design and an eye toward bettering the environment, Keith Zendler founded Environmental Services of North America Inc. in Detroit.
Nearly thirty years later, the company retooled and relaunched to focus on waste management and upgraded its technology to help it expand and improve its services and expand its network of partners domestically and globally.
We interviewed founder and owner Keith Zendler to learn more.
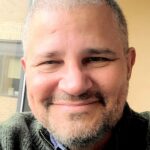
Q: Tell us about RecycleMax.
A: RecycleMax is a tech-based reboot of a company I founded in 1995. At that time, we had a plant in Detroit and a fleet of 14 trucks and we were focused mainly on paper and similar recyclables. We now provide the environmentally sound management of virtually all solid and liquid waste materials.
I have always been interested in sustainability from a community standpoint – in building stronger and more sustainable communities through technology. So, I sold the original recycling company in 2008 and started a civic tech company focused on designing an online community network for people and organizations to better work together. Through this company, I launched a multisided SaaS platform with the intent of improving stakeholder communication, collaboration, and engagement to help leaders solve political, health, social, environmental, and economic issues.
Eventually, I realized I could apply this technology to the recycling industry and provide businesses with robust and customized waste management programs that help them meet their sustainability goals and reduce their carbon footprint. So, RecycleMax was relaunched as a tech-based company in 2020.
We use the same technology we offer clients internally for our operations. The crux of the platform is its ability to facilitate a community network and real-time communication. We have used it to build a global network of recyclers and haulers that we can leverage for clients.
Q: How is the industry different now, than in the 1990s?
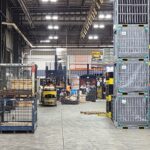
A: There was a time when we had to push companies to recycle, and they would only do so if we could show that it either saved them money or at the very least did not incur additional expenses. That is no longer the driver. Companies are doing it now no matter what. That is a surprising shift. We work heavily in the auto industry, and I’ve been amazed at how progressive these companies are and how seriously the industry is taking environmental measures.
Adding to that, until recently, most of our recyclables were shipped overseas, and we relied on China to handle them. A lot of waste was ending up in the ocean. China shut that off and it certainly caused a disruption, but ultimately it made the industry stronger. There are more and more companies being established in the U.S. to handle these materials.
The industry has made a tremendous amount of progress, and it’s exciting.
Q: Who are some of your customers in Detroit and Southeast Michigan?
A: Union Tank Car Company, Detroit Manufacturing Systems, Fishbeck, and Piston Automotive to name a few.
Q: In your experience, what are the challenges companies face with recycling?
A: Education and incentivization. Employees often need to be trained in why and how to recycle and handle their waste materials. It’s also vitally important for individuals to understand the difference they are making. Providing that data offers motivation to continue the momentum toward success.
Q: What are the biggest challenges you see that businesses have with waste management?
A: Participation is probably the biggest challenge. Companies need all employees on board. Training and education are critical to a successful recycling program. There is still a lot of work to do in getting people to take recycling seriously.
Plastic is another big challenge for the industry. There are types of plastics that are not commonly recycled due to the unique resins involved. It can become difficult for companies to manage this.
Trucking and logistics are a challenge as well. Transportation costs can be the biggest component when it comes to recycling.
Q: What are the biggest opportunities?
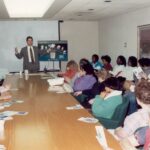
A: I think there is a massive global opportunity in recycling. And by applying technology, the potential to streamline efficiencies is huge.
I never thought I’d be in recycling for over thirty years, but It’s a wonderful industry. It feels good to be able to help businesses meet their recycling and waste management goals and do their part to better the environment.
Be sure to subscribe to our newsletter for regular updates on sustainable business practices in and around Detroit.