Ann Arbor’s Climate Strategy
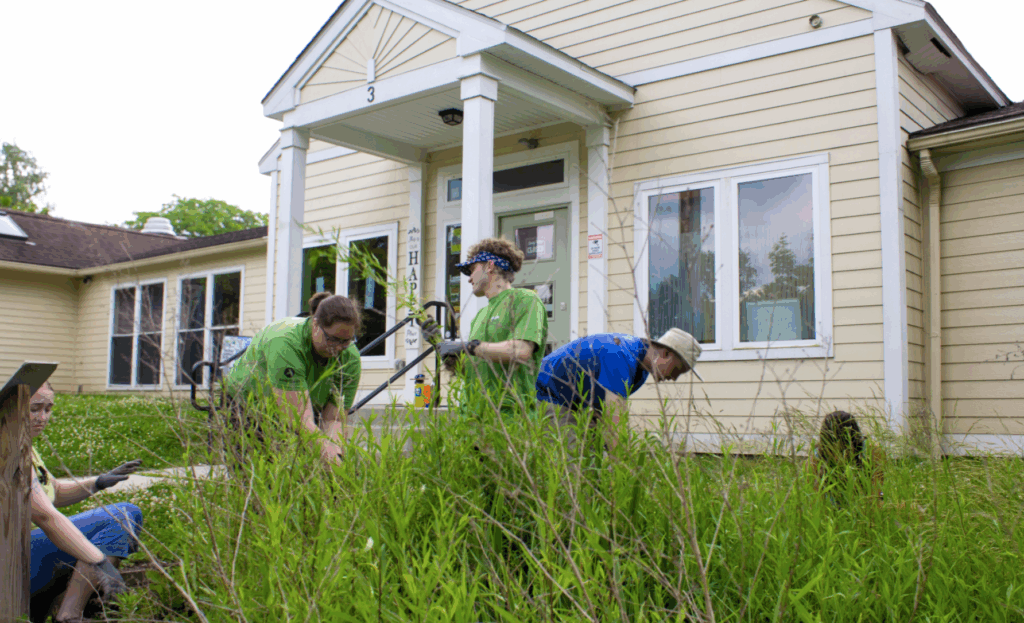
In 2020, the City of Ann Arbor adopted A²ZERO, a climate action strategy designed to achieve community-wide carbon neutrality by 2030. The plan outlines a framework for embedding sustainability into city operations, economic growth, and everyday decision-making, while also emphasizing equity and long-term resilience. One of the most visible efforts under A²ZERO is the Bryant project, a first-of-its-kind initiative to transition an entire neighborhood—home to more than 250 households—toward carbon neutrality. The project combines energy efficiency upgrades, renewable energy, and community-centered planning to create a scalable model for neighborhood-scale decarbonization. Leading the A2ZERO program is Missy Stults, Ann Arbor’s sustainability and innovations director, who helped steer the A²ZERO plan’s rapid development and continues to guide its evolution. SBN Detroit interviewed Stults about how the plan is shaping the local economy, what other cities can learn from Ann Arbor’s approach, and the challenges and opportunities that lie ahead. Q: How is sustainability fueling the local economy in Ann Arbor, and what benefits are you seeing from the A20 plan? A: We’re working to institutionalize sustainability as part of the culture, and we are seeing it manifest in multiple ways. Tech entrepreneurs are innovating around clean energy and mobility. In the circular economy, businesses are repurposing materials or finding second lives for decommissioned electronics—like harvesting valuable parts from old phones. I see this as a movement by which people make choices not just because they’re profitable, but because they’re right, and we’re making them more convenient. Over time, that mindset fuels business innovation and economic resilience. Q: What differentiates A²ZERO from other cities? A: First, the speed. We built this plan in 82 days. Second, we never pretended it would be perfect – we focused on what was possible and necessary. We talk about the planning being a living framework for our work, something that is directional but not the directions for where we need to go. Third, we anchored it in three pillars: equity, sustainability, and transformation. Equity is the center of the work (not just a lens we look through). Sustainability means it must last well beyond any of us. Transformation acknowledges that the systems that created this crisis cannot be the systems that solve it. Lastly, we also didn’t shy away from costs. It would have been easier to gloss over the investments needed, but we were transparent. That honesty has required us to be bold and very vulnerable, and I think that differentiates the Ann Arbor process. Q: How has the strategy evolved since its 2020 adoption? A: Constantly. Telework is a good example. The original plan was written in 2019, just before the pandemic. Telework wasn’t part of it – then suddenly it became central. The plan is directional, and we adapt to cultural, political, and financial moments as they come. Another example is tree planting. Our goal was to plant 10,000 trees later in the plan, but in 2020, we pulled that forward because it was work we could do during the pandemic. We’ve now planted 11,000 trees. That’s the beauty of a living document – It allows us to be nimble while staying aligned to the overall direction. Q: If you could think freely – blue-sky style – what environmental innovation or policy would you love to see Ann Arbor implement next? A: If a flood is happening, the first thing you do is turn off the faucet before you clean up. We need that mindset here. We need building codes and regulations that stop allowing new buildings that pollute. We need aggressive codes that require polluters, such as manufacturers and industrial operators- not individuals – to take responsibility for the pollution they are creating. That kind of systemic shift is essential. Q: What key lessons can other cities learn from the Bryant project? A: The importance of trust. It’s something you can’t underestimate. The community has to determine the end goals. And you have to show up consistently, even when the answers aren’t easy. Early on, people asked, “What if Bryant gentrifies?” We didn’t have an answer – but we said that out loud and committed to figuring it out together. Persistence and vision matter. People need hope, but hope without action is empty. In Bryant, we’ve paired hope with concrete steps – like stabilizing utility bills through energy efficiency improvements- and that sequencing is critical. Now the project has momentum, and we are looking at things like installing networked geothermal. Q: Given recent setbacks—like reduced federal funding and legal barriers—what’s your strategy for sustaining progress? A: Force and persistence. There’s no option but to keep doing this work. Well, the only option is complacency, and that won’t happen. Success begets success. Our goal is to institutionalize sustainability so deeply that it doesn’t matter who is in my role – this will be part of Ann Arbor’s DNA. It’s important to note that local governments have historically had do this without much federal support. The Biden administration was an outlier. We are used to working under challenging conditions, and we will continue regardless. Q: What are some recent wins or innovations? A: In November 2024, voters approved creating the nation’s first sustainable energy utility—an opt-in utility that is supplemental to the existing investor-owned utility, and a utility that only offers energy from renewable energy sources. That’s transformative. In Bryant, we’ve secured $18 million, including a $10 million federal geothermal grant we hope is finalized soon. That would be one of the first large-scale demonstrations of an alternative heating and cooling model in the country. We’re also piloting a circularity initiative with returnable containers, which could scale into broader partnerships. I’ll stop there. There’s much more being done, but these are some good examples of the transformation that’s happening. Q: How are you tracking outcomes? A: We use a mix of metrics. Some update automatically every day into a reporting dashboard we have; others are annual. We’re close to releasing the 2024 annual report. But we also recognize that not everything that matters can
Powering Smarter Battery Futures
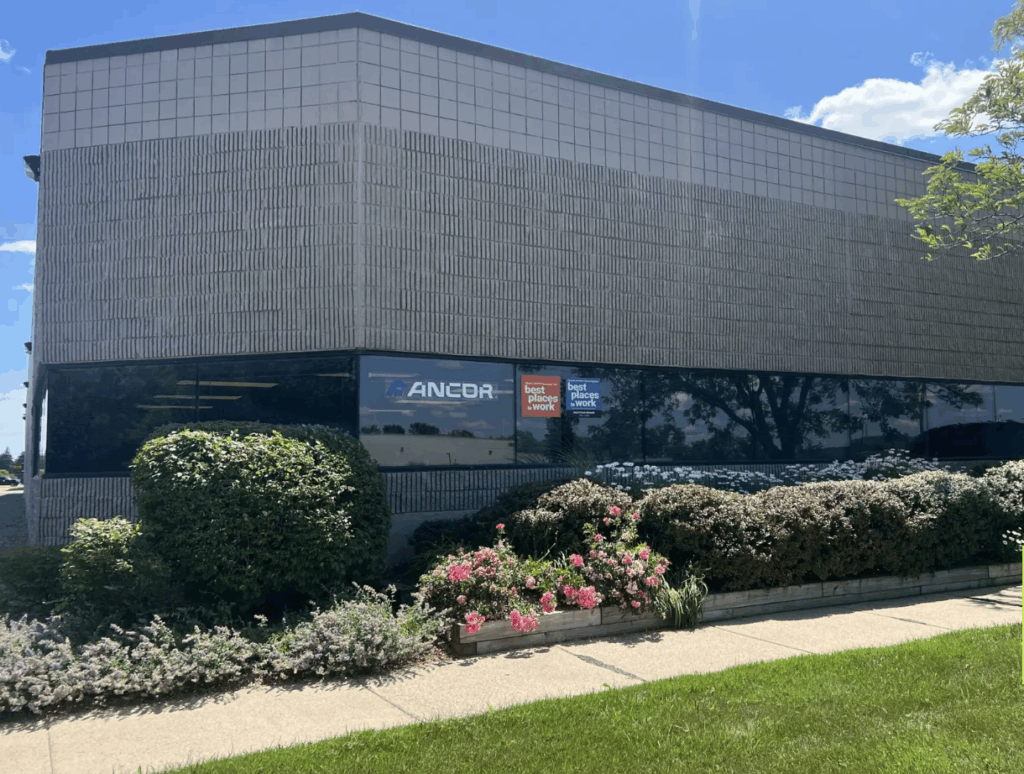
Troy-based Ancor’s roots are in automotive compliance and labeling, but the company has expanded into smart-technology solutions for healthcare, retail, and automotive, including smart battery tracking to stay compliant with local and global regulations. One of its developments is BattCor, a next-generation platform designed to create a real-time “digital twin” of an electric vehicle battery, enabling real-time monitoring, predictive analytics, and improved lifecycle management—from first use through recycling or repurposing. SBN Detroit interviewed CEO Jose L. Flores about the evolution of battery management systems and the challenges and opportunities in electric mobility. Q: Tell us about Ancor Automotive and BattCor. A: Ancor began 50 years ago as a data management and labeling supplier for OEMs. Three years ago, we launched an innovation hub—now our Innovation Solutions Division to expand into tech-forward and sustainable solutions – just as the EV revolution accelerated. We saw a clear gap: while automakers focused on vehicle production, very few addressed battery lifecycle, repurposing, or compliance at scale. BattCor was built to solve that. It’s a digital twin that provides real-time battery health insights and predictive analytics, helping optimize charging, extend lifespan, and even return energy to the grid while consolidating siloed data into unified platform for compliance, sustainability, and better decision-making. BattCor isn’t just a product—it’s how we’re helping organizations future-proof their energy strategies through data-driven decision-making. Q: How is the evolution of battery management systems (BMS) reshaping what’s possible in electric mobility and energy storage? A: The next frontier is taking BMS from reaction to prediction. And this extends well beyond automotive. Once a battery’s primary life in a vehicle is over, it can still serve as stationary storage—for example, in healthcare facilities or other industries with high energy demands. That second life is an untapped opportunity. But there are challenges. Recycling EV batteries is still a complex and not widely understood process. In the EU, for example, regulations already require a minimum percentage of recycled materials—13% recycled cobalt, among other components. To meet that, you need full visibility into a battery’s history and condition. That’s where centralized, accessible data becomes essential. Q: What are the biggest technical or infrastructure challenges in deploying advanced battery systems at scale? A: The first challenge is data chaos. Without integration, insights are either lost or stuck in silos. The second is alignment. We don’t yet have a clear, universal path to compliance, and different stakeholders are moving in different directions. Infrastructure is another question – can the current grid support widespread EV adoption? Are the right regulations in place? Too much of the industry is still operating in silos, and that fragmentation makes it harder to scale sustainable, intelligent solutions. Q: From a sustainability perspective, how can smarter BMS influence circularity and lifecycle efficiency? A: When BMS technology incorporates predictive analytics, it enables smarter charging and discharging behavior, batteries charge more efficiently and avoid unnecessary wear. Smart charging – avoiding constant charging cycles – extends battery life and reduces resource consumption. That’s key for sustainability. The longer we keep batteries in the field, the fewer raw materials we need to extract. Q: How is demand for better battery intelligence changing? A: It’s growing rapidly. From a manufacturer’s standpoint, being able to demonstrate that your batteries last longer and perform better is a strategic differentiator. Effective management not only preserves value for the consumer but also reduces warranty issues and improves brand reputation. Q: What barriers still need to be addressed for mass adoption of advanced BMS platforms? A: Infrastructure is a major barrier. Some cities have robust charging networks, but many don’t. Beyond that, we need the grid to operate as a two-way street—able to receive energy from EVs as well as supply it. What we need now is alignment—not just across tech providers, but across regulators, utilities, and OEMs. The question is: can the rest of the ecosystem move with the same urgency as platforms like BattCor. Q: Battery safety is critical in EVs and aviation. How is the industry shifting its approach? A: Battery anxiety is real. With predictive monitoring, we can catch early warning signs like rising temperatures before they escalate. If parameters are trending toward failure, action can be taken immediately. This proactive approach can dramatically reduce the risk of catastrophic events and improve confidence in the technology. Q: Looking ahead 5–10 years, what’s the most transformational potential of battery intelligence? A: We’ll see an entirely new level of autonomy in how vehicles and buildings manage energy. Imagine a car that decides when to charge based on grid demand, or a building that balances its energy use based on stored battery health. We could see vehicles and the grid collaborating to optimize distribution, reduce strain during peak hours, and even stabilize the system during emergencies. Ultimately, companies will seek unified platforms that can integrate sustainability, compliance, tracking, and predictive analysis in one place. There are players who excel in one or two of those areas, but very few that can bring it all together. That’s where Ancor is focused, and BattCor is our blueprint for that future. We’re not just participating in the next wave of battery innovation. We’re helping lead it. Be sure to subscribe to our newsletter for regular updates on sustainable business practices in and around Detroit.
Electrifying Eastern Market
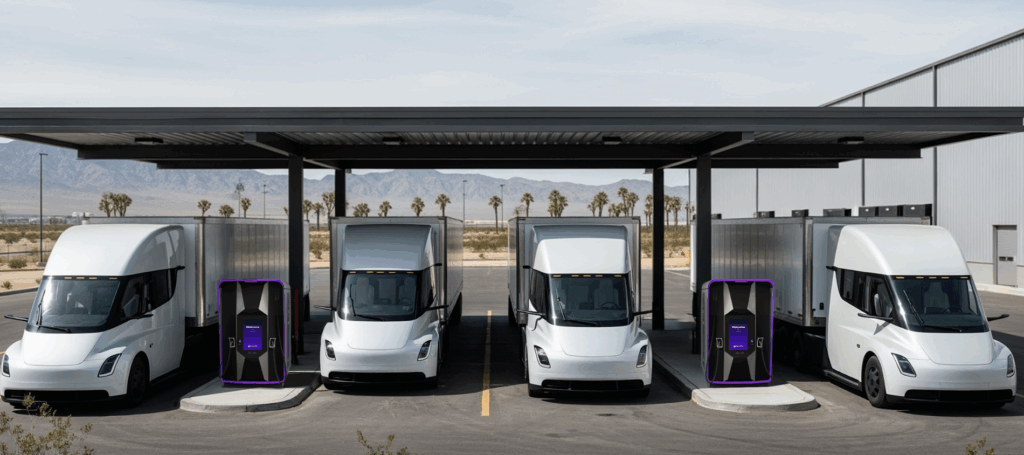
Detroit’s Eastern Market is working to become a national model for integrating freight solutions that reduce fossil fuel use and freight operation costs. San Carlos, Calif.-based ElectricFish, a finalist in the Toyota Mobility Foundation’s Sustainable Cities Challenge, was chosen to build battery-integrated fast chargers to power EVs and provide backup energy for Eastern Market. As one of only three cities worldwide chosen for this challenge, Detroit is using the opportunity to position itself as a leader in transportation innovation, this time in clean mobility. SBN Detroit interviewed ElectricFish co-founder Anurag Kamal about why Eastern Market is the ideal proving ground, what this means for the city’s EV landscape, and how this project could influence urban electrification nationwide. Q: What does Detroit’s selection as a Toyota Mobility Foundation Sustainable Cities Challenge finalist mean for its position in EV and clean mobility? A: Being one of just three cities in the world chosen for this program is an achievement in itself. Detroit has always been a center of automotive innovation, and now we’re seeing a new evolution – from internal combustion to electric. The challenges are complex, especially for medium- and heavy-duty freight vehicles, where electrification requires both cost-effective solutions and robust infrastructure. This project is a way to demonstrate what’s possible and draw attention to Detroit’s potential in leading the shift to sustainable transport. Q: What advantages or challenges does Detroit present for innovating in EV infrastructure? A: Detroit’s biggest advantage is its proximity to the automakers and decision-makers. For startups like ours, having industry leaders see our work firsthand is invaluable. But Detroit is also a challenging test bed – the infrastructure in many areas is outdated and upgrading it can be extremely expensive. In places like Eastern Market, where we’re deploying, the cost to modernize could run into the millions. That’s why we’re proving there’s a different, more cost-effective way to build charging capability that can be replicated in other cities with similar constraints. Q: How does the Toyota Mobility Foundation competition help accelerate innovation? A: Funding is a huge part of it. Detroit secured $3 million for the first phase, with additional funding for companies that advance to later stages. Just as important is the collaboration—talking directly with local businesses, understanding their needs, and identifying unique challenges. For example, a mid-sized fishery in Eastern Market could lose thousands of dollars in product during a four- to six-hour outage caused by infrastructure upgrades. Backup energy solutions become not just a convenience, but a necessity. Q: What does success look like for this project? A: In the short term, success means mid-sized businesses in Eastern Market integrating sustainable practices, whether that’s switching to EVs or having accessible charging infrastructure on-site. For small vendors, it means being able to plug in while working in the market. On September 26, we will launch the first Public Fast Charging Hub at an event that’s open to the public. We’ll be able to demonstrate first-hand how businesses can benefit, and we are hoping to get early adoption. Long term, we want Detroit’s project to be a national case study in rapid, cost-effective urban electrification—something that inspires other cities to follow. Q: What are the biggest gaps you see today in EV charging and fleet electrification? A: Infrastructure is the number one gap. There’s a common perception that switching to electric means changing your entire workflow, parking a vehicle overnight for charging, waiting hours instead of minutes. That’s not sustainable for many businesses. The challenge is not just funding infrastructure but also developing alternative technologies and deployment models that make charging fast, flexible, and accessible. Q: As a startup, how do you decide which innovations to prioritize? A: It’s a constant balancing act. We designed a product with two very fast charging ports that can be deployed almost anywhere. But some customers question the need to pay for faster charging when they don’t see the immediate benefit. Others, like Amazon, request larger-scale systems with eight ports. The key is to stay laser-focused on our mission, move quickly, and avoid overextending into too many variations at once. Q: What lessons have you learned about scaling technology in a rapidly changing industry? A: Flexibility is everything. We’ve seen battery pack prices drop from $200,000 to $60,000 in just three and a half years. Locking into long-term agreements without room to adapt can be costly. We make sure our supply agreements account for technological changes, so we can pivot as new, more cost-effective options emerge. Q: What’s your vision for Detroit’s EV charging landscape in 10 years? A: I think we’ll see significant fleet electrification – possibly 10% adoption or more – along with widespread public and private charging. Places that sell fuel today will likely also serve EV drivers. Home charging will be common for homeowners, but public infrastructure will carry the bulk of the load. If projects like Eastern Market succeed, Detroit could be one of the most compelling examples of how urban EV infrastructure can be built quickly, effectively, and in a way that meets the needs of diverse users. Be sure to subscribe to our newsletter for regular updates on sustainable business practices in and around Detroit.
Building with Purpose
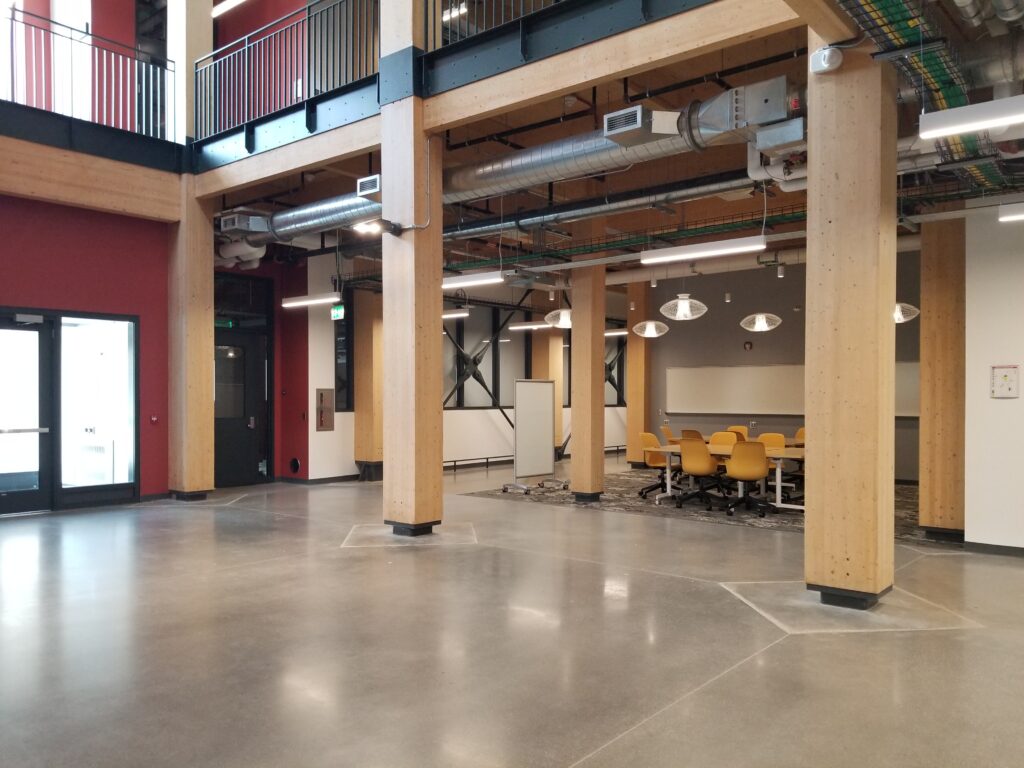
MassTimber@MSU is a cross-disciplinary initiative at Michigan State University dedicated to advancing mass timber construction and manufacturing in Michigan. Collaborating with partners across construction, forestry, development, and state agencies—including the Michigan Department of Natural Resources—the initiative leverages MSU’s land-grant mission through research, teaching, stakeholder engagement, and policy development to build a sustainable mass timber future for the state. SBN Detroit interviewed Sandra Lupien, Director of MassTimber@MSU, about the environmental, economic, and design implications of mass timber and the growing momentum behind the material in Michigan and beyond. Q: What is the MassTimber@MSU initiative, and what inspired its creation? A: MassTimber@MSU is a collaboration across MSU’s School of Planning, Design and Construction, Department of Forestry, and MSU Extension. We work with partners across the state—including construction professionals, foresters, community and development organizations, and state agencies like the Michigan Department of Natural Resources—to advance mass timber construction and manufacturing in Michigan. Our approach reflects MSU’s land-grant mission: research, teaching and curriculum development, stakeholder engagement, and policy exploration that could support mass timber adoption. Since I started in this role in July 2021, momentum is growing. There are now more than 65 mass timber projects in the pipeline in Michigan. The STEM Teaching and Learning Facility on MSU’s campus, which is the second building in the state to use cross-laminated timber (CLT), helped demonstrate what’s possible. And we’re now seeing serious interest from prospective producers who are looking to locate in Michigan. Q: What are the environmental benefits of mass timber in terms of sustainability, carbon reduction, and climate resilience? A: This is exactly what drew me to mass timber. It’s a tool in our toolkit to reduce carbon emissions, support sustainable communities, and help foster healthier, more resilient forests. Globally, the built environment accounts for about 39% of greenhouse gas emissions—28% from building operations and 11% from construction materials like concrete, steel, and glass. These materials are essential, but they’re energy-intensive to produce. Wood, by contrast, is a renewable resource that stores carbon. When we use wood in construction, we’re not only lowering a building’s embodied carbon footprint—we’re also locking that carbon into the structure itself. At MSU, the STEM Teaching and Learning Facility contains roughly 3,000 cubic meters of mass timber, which stores about 1,856 metric tons of carbon dioxide equivalent. That’s comparable to removing the emissions from 4 million miles driven by an average car. Mass timber buildings, in this way, become carbon storage banks. On the forestry side, we know that many forests evolved with low-intensity natural fires that helped maintain healthy densities. Today, many of our forests are overcrowded, which makes them vulnerable to pests, disease, and catastrophic wildfire. Because of past logging practices and fire suppression, we have an obligation—and opportunity—to steward forests more sustainably. When we do that, we can produce wood that extends the climate benefits of trees, especially if that wood would otherwise decay or burn. Q: How are MSU students and faculty engaging with mass timber—from design to research to real-world application? A: There are three main academic areas deeply engaged with mass timber: Construction Management, Forestry and Biochemistry, and Civil and Environmental Engineering. We have undergraduates, master’s students, and Ph.D. candidates working with faculty on projects across those disciplines. In Construction Management, Professor George Berghorn is developing mass timber curriculum modules that can be used nationally in engineering and construction programs. In Forestry, Professor Mojgan Nejad is doing incredible work on developing bio-based adhesives and coatings for use in mass timber—replacing fossil-fuel-based polyurethane with lignin-based alternatives. She’s actively working toward commercialization. We’ve also done economic research to analyze supply chains and survey demand, which helps inform developers and policymakers. And beginning Spring 2025, we launched a new course focused entirely on mass timber, led by Dr. George Berghorn and tailored for both undergraduate and graduate students. Q: From an economic perspective, how could mass timber help revitalize Michigan’s forestry sector and rural economies? A: We’ve modeled the economic impacts of launching a 50,000-cubic-meter-per-year mass timber manufacturing facility in Michigan. The results are exciting: such a facility would contribute $152 million to the state’s GDP and support 318 jobs. There’s a strong need to find new uses for Michigan wood. With the paper industry in decline and other traditional markets shifting, mass timber presents an opportunity to create high-value products that support Michigan jobs and rural economies. Q: How does the initiative align with Michigan’s climate goals or sustainable development strategies statewide? A: The MI Healthy Climate Plan, which outlines the state’s climate goals, directly mentions mass timber three times—as a key strategy for reducing emissions in the built environment and managing natural lands sustainably. The City of Lansing’s Sustainability Action Plan also highlights mass timber, and East Lansing has even amended its zoning ordinance to incentivize developers to use mass timber and build LEED-certified projects. It’s encouraging to see this kind of policy support—it sends a signal that mass timber can and should be part of Michigan’s climate solution. Q: What does Michigan’s existing forest resource look like, and how does sustainable forestry tie into your vision? A: Healthy, resilient forests are the foundation of everything we do. In Michigan, about 70% of our forest resource is hardwood and 30% is softwood. Most mass timber products currently certified for use in the U.S. are made from softwoods. That said, Michigan does have suitable softwood species. For example, red pine was certified for structural use because the Michigan DNR prioritized using Michigan wood in a customer service building in the Upper Peninsula. That’s a great example of state leadership driving local wood utilization. As the industry evolves, there’s potential to expand the species we can use in mass timber production. Q: Looking ahead five to ten years, what’s your boldest vision for the impact of the Mass Timber Initiative? A: I’d like to see commercial buildings—everything from multifamily housing to community centers to industrial facilities—considering mass timber from the outset, not as a novelty but as a viable, mainstream option. Mass timber
Identifying Opportunities for Improved Efficiencies

The Energy Alliance Group of North America focuses on helping businesses implement sustainable energy solutions by identifying opportunities for improved efficiency and connecting clients to funding and technology. Based in Ann Arbor, Michigan, the company collaborates with commercial and industrial property managers to reduce energy consumption, enhance operations, and achieve long-term cost savings. SBN Detroit interviewed Scott Ringlein, founder, principal, and Chief Strategy Officer, about energy efficiency in Southeast Michigan, the role of financing and audits, and the importance of long-term thinking when it comes to sustainability. Q: What are the biggest energy efficiency challenges facing commercial and industrial buildings in Southeast Michigan? A: Misinformation is one of the biggest challenges. Every building has the opportunity to implement energy efficiency improvements, and there is money available to make it happen. These improvements offer a return on investment, but many building operators and owners either don’t believe the numbers or assume they don’t apply to them. The truth is, utility costs are ongoing and only getting higher, so the only way to gain control is to improve your building’s efficiency. Q: How can businesses identify when it’s time to upgrade or retrofit their energy systems A: Start by knowing what you have—what systems are in place, their expected lifespan, and their maintenance history. If you’re seeing frequent repairs and higher maintenance costs, it’s time to look at alternatives. Then evaluate how much more efficient a new system could be and what kind of energy savings it could deliver. If the numbers make sense, that’s the signal to move forward. Unfortunately, many businesses struggle with that last step—deciding to invest. Q: What misconceptions do you commonly encounter around cost recovery or energy savings? A: Many building owners don’t believe the projections—even when we show them data that supports a positive cash flow within one or two years. They tend to focus solely on ROI and forget that utilities never go away. You’re always going to pay for water, electricity, gas—whatever it is. And the utility companies have no vested interest in lowering your costs. So even if you’re skeptical, you’re still going to be paying more year after year unless you act. Q: How has the financing landscape changed for energy upgrades—especially for nonprofits or small businesses? A: We’ve been in this space since 2012, and the financing options today are better than they’ve ever been. Tax credits will come and go, but there are more long-term tools now than there were a decade ago. Michigan has been a leader in this area. Programs like Michigan Saves were the first of their kind in the U.S. We’re also a state approved for Property Assessed Clean Energy (PACE) financing, although it’s underutilized here compared to states like California. Still, the options are out there—you have choices, and you can take control. Q: What role do energy audits play in long-term planning, and how often should they be conducted? A: Audits are essential. You need to know where you stand—what equipment you have, how efficient it is, and what condition it’s in. It’s surprising how many clients have never even been on their own roof, where all the major equipment is housed. There are different levels of audits. A Level 1 audit gives you a basic understanding of what you have and where you’re spending your money. A Level 3 audit goes deeper and is useful when you’re preparing to make major decisions—like process changes or equipment replacement. A challenge is that many companies don’t take the time for a comprehensive audit until it’s too late. Smaller organizations may lack the staff, and larger ones may lose visibility due to scale. But without that baseline, long-term planning is difficult. Q: How do Southeast Michigan’s climate swings shape energy strategy in the region? A: As an organization, we don’t use climate change as the primary argument for doing the right thing. Climate change is happening, but we believe the conversation around energy efficiency should be happening regardless. You’re spending money on utilities – and there are better systems and more efficient ways to operate. We also need to think long-term. In the U.S., we don’t treat these upgrades as long-term investments the way they do in Europe or Asia. There, the systems are central to the building’s value and are maintained accordingly. Here, we often focus too much on short-term costs instead of building for performance and sustainability. Q: What advice do you have for businesses looking to reduce costs and improve operations going forward? A: Real-time monitoring of building systems from a central location gives you visibility and control. Beyond that, the cost of implementing technologies like LED lighting, heat pumps, solar panels, and combined heat and power (CHP) systems has become very feasible. There are also integrated systems now—solar light poles with battery storage and surveillance, for example—that operate independently of utility companies. The key is maintenance. These systems don’t last forever if they’re neglected. But with built-in monitoring and upkeep, they can be powerful tools for cutting costs and improving resilience. Be sure to subscribe to our newsletter for regular updates on sustainable business practices in and around Detroit.
Sustainability in Practice at the Detroit VA

The Detroit VA Healthcare System is implementing a systemwide sustainability strategy through its Green Environmental Management System (GEMS), designed to reduce waste, lower energy consumption, and improve operational efficiency. The program recently earned Practice Greenhealth’s “Top 25 Environmental Excellence Award.” Through coordinated efforts across departments and a commitment to innovation—particularly in high-resource areas like dialysis—the Detroit VA works to demonstrate how environmental stewardship and clinical care can go hand in hand. SBN Detroit interviewed Andrew Deppner, clinical nurse manager of the hemodialysis unit at the Detroit VA, to learn more about the system’s approach and what other healthcare institutions can adopt from their progress. Q: Why do you think sustainability is such a crucial part of healthcare today? A: Sustainability is relevant to all human operations today—we’re working with finite resources, and being good stewards of those resources is imperative. That’s especially true in healthcare. The population is aging, and we’re seeing more people living longer with chronic health needs. Meanwhile, healthcare itself is becoming more expensive. That means we need to be smarter about how we allocate and use resources. At the VA, we serve 9 million–10 million veterans every year with a workforce of nearly half a million staff members. The sheer scale of our operations means our environmental footprint is significant. So our responsibility is twofold: Providing top-tier care and managing the institution in a way that honors that care through sustainability. Q: Walk me through the structure of the GEMS program. How do departments collaborate to implement sustainability initiatives across such a large system? A: GEMS operates as a committee that meets quarterly to evaluate all relevant projects—whether it’s new construction, repairs, upgrades, or procedural changes. One of our key parameters for approval is sustainability. We always ask: Can this process or improvement be made more sustainable? We also assess best practices across the larger VA health system and use that insight to inform local decisions. That structure allows us to prioritize environmental responsibility across the board while tailoring solutions to our specific needs. Q: In terms of winning Practice Greenhealth’s Top 25 Environmental Excellence Award, what do you think sets the Detroit VA apart, and what might others learn from your example? A: Honestly, it comes down to our scale and our passion. We deliver a huge volume of patient care, so the impact of our sustainability efforts is magnified. But what truly sets us apart is that our team is fully committed. Stewardship isn’t just an initiative here—it’s a value we live by. That passion influences every decision we make, and it shows up in the way we approach both large-scale projects and day-to-day operations. If there’s one thing other systems can take away, it’s that passion drives results. When your team is genuinely invested in sustainability, it shows up in your outcomes. Q: How did your team reimagine the system to reverse the traditional water-use ratio in dialysis—and are other departments applying this kind of thinking? A: Traditionally, reverse osmosis (RO) systems in dialysis operate with significant water waste, which is 60% to 80% efficient. We are working at about 98% efficiency. We achieved this by choosing a high-recovery RO system over a standard one. That decision alone results in millions of gallons of water saved each year. When we received quotes from vendors, we made high-recovery RO our top priority, even though it required more investment and more work on our end. We believed it was worth it, and our team embraced the challenge. Q: What were some of the biggest challenges you encountered when trying to drive sustainability in a healthcare setting, and how did you overcome them? A: One challenge was our water room construction project. We decided to partner with a smaller, less globally established engineering company. That meant we had to take on a larger share of the planning and preparation ourselves. The tradeoff was that we had more control over the sustainability aspects of the project, but it also required more time and resources. Despite the extra effort — more vendor coordination, more problem-solving — it paid off. We now have a highly efficient system that we believe in. It was more work, but we were willing to do it because the outcome aligned with our values. Q: How does the Detroit VA balance sustainability with the demands of clinical care, especially in high-intensity or resource-heavy departments? A: It starts with commitment. Everyone on our team is dedicated to serving our veterans. That shared purpose enables us to pursue ambitious projects without compromising care. I’ve been able to focus on our sustainability efforts because I trust my clinical team implicitly. Their professionalism and passion have freed me to work on these broader initiatives, and I know the patient care side is in excellent hands. Q: If you could share one key takeaway or piece of advice with other healthcare systems looking to follow your lead, what would it be? A: Plan ahead. You can’t foresee every variable, but the more proactive you are, the better your outcomes will be. Anticipate your resource needs early and map out the process thoroughly. If you do that, you’ll be in a stronger position to allocate budget and support before problems arise. Sustainability is about systems thinking, and that starts with good planning. Be sure to subscribe to our newsletter for regular updates on sustainable business practices in and around Detroit.
Reimagining the Pallet Supply Chain

Founded in Michigan, 3R Pallets is working to transform what can be an environmentally costly component of global logistics: the shipping pallet. The company creates reusable composite pallets made with recycled plastics and reclaimed plant fibers, designed to reduce waste and extend product lifespan, offering a scalable alternative to traditional wood and plastic models. SBN Detroit interviewed co-founder Kylee Guenther about innovation in the pallet industry, the environmental consequences, and the outlook for Southeast Michigan and beyond. Q: What was the impetus behind founding 3R Pallets? A: I’m the second-generation in my family to work in Michigan’s plastics industry—I literally grew up on the shop floor, learning from the bottom up. My dad worked on everything from one-gallon milk bottles to those little lemon-shaped juice containers. I was always fascinated by the engineering, but I was also concerned by the amount of waste I saw. As an adult, I became more focused on sustainability and how I could be part of the solution, so I decided to do something about it. That’s how 3R Pallets was born. Our goal is to disrupt the archaic wooden shipping pallet industry with the world’s most sustainable pallets. Not only are our pallets sustainable, but we help save our customers money. Traditional pallets damage and destroy product, cause production downtimes and need constant repair and endless reordering. With our drop in solution, we’re disrupting this space. We just graduated from TechStars and are the first company from Lansing to ever be accepted. It’s one of the most competitive and respected accelerators in the country. We’re also currently raising a $1.2 million pre-seed round to help onboard new customers, build inventory, and grow our team. Q: What do most people misunderstand about the scale and impact of pallet production? A: People just don’t think about them. Pallets are invisible to most consumers. They’re not something you interact with every day, so it’s hard to grasp the scale unless you’ve worked in logistics or manufacturing. Compare that to straws, bags, or plastic bottles—people have firsthand experience with those, so there’s a clear sense of impact. But over 90% of the goods we use were shipped on a pallet at some point. It’s a massive part of the supply chain that’s often overlooked. Q: With pallet use expected to increase in the next decade due to e-commerce growth, what are the biggest sustainability challenges facing the industry today? A: The first big challenge is access to materials. We’re already seeing lumber shortages in many places, and if demand doubles, costs will rise, and pressure on forests will increase. We can’t pretend there’s an endless supply of trees to meet that need. Plastic pallets are often seen as an alternative, but not all plastics can be used in pallet manufacturing. And recycling plastic isn’t a forever solution—it degrades over time. Our approach uses recycled plastic and reclaimed bamboo fibers which actually strengthens the material and increases how many times it can be reused or recycled. Q: Most wooden pallets are only used a few times before being discarded. Why has reuse or recycling been such a persistent challenge? A: The main issue is durability. Wooden pallets simply aren’t built to last. They break down after a few uses, especially when hit by forklifts or exposed to the elements. And if they’ve been fumigated, they often can’t be recycled at all. Our composite pallets can be used 50 to 60 times. They won’t degrade like wooden pallets and can be repaired or recycled when necessary. That’s a huge improvement in terms of both cost and environmental impact. Q: What is the typical lifecycle of a pallet from production to landfill, and where are the biggest environmental pain points? A: For wood, a tree is grown, cut down, milled, and nailed into a pallet. It’s sent to a distributor, then to a customer, used a few times, and if it’s damaged or treated, it goes to a landfill. Best case scenario is they enter a secondary market after being repaired and get a couple more uses. Plastic pallets are usually injection molded, often using virgin plastic. They might last for 30 to 40 cycles, then either get recycled or landfilled depending on their condition. Our pallets are different. They’re made with non-edible plant fibers with recycled plastic and molded into a durable product. They can go through 50 to 60 uses, and in many cases can be repaired or recycled again. That means fewer pallets are needed overall—and far fewer are discarded. Q: How does Michigan contribute to or feel the impacts of pallet consumption? A: We use a lot of pallets here—there’s no doubt about that. But Michigan also gives us a big opportunity because the automotive industry is one of the most forward-thinking when it comes to closed loopy supply chains. We’re already seeing traction in that space. Our value proposition is simple: help customers ship more goods with fewer pallets. That’s good for business and good for the planet. Q: How does the end-of-life of a pallet impact the total carbon footprint of a shipping operation? A: It’s huge. Most traditional wood or plastic pallets end up in landfills and producing new ones requires more energy and raw materials. That adds up. If you extend the life of a pallet and reduce the number of replacements needed, you lower emissions, reduce waste, and conserve resources. Our composite pallets are designed to be durable and recyclable, which makes the whole system more sustainable from start to finish. Q: What has innovation been like in the pallet industry? A: There truly hasn’t been a lot of innovation. Most of it is on the software side but the heart of shipping is still the pallet. Be sure to subscribe to our newsletter for regular updates on sustainable business practices in and around Detroit.
Designing for the Future: How HED Approaches Sustainable, Integrated Design Delivery
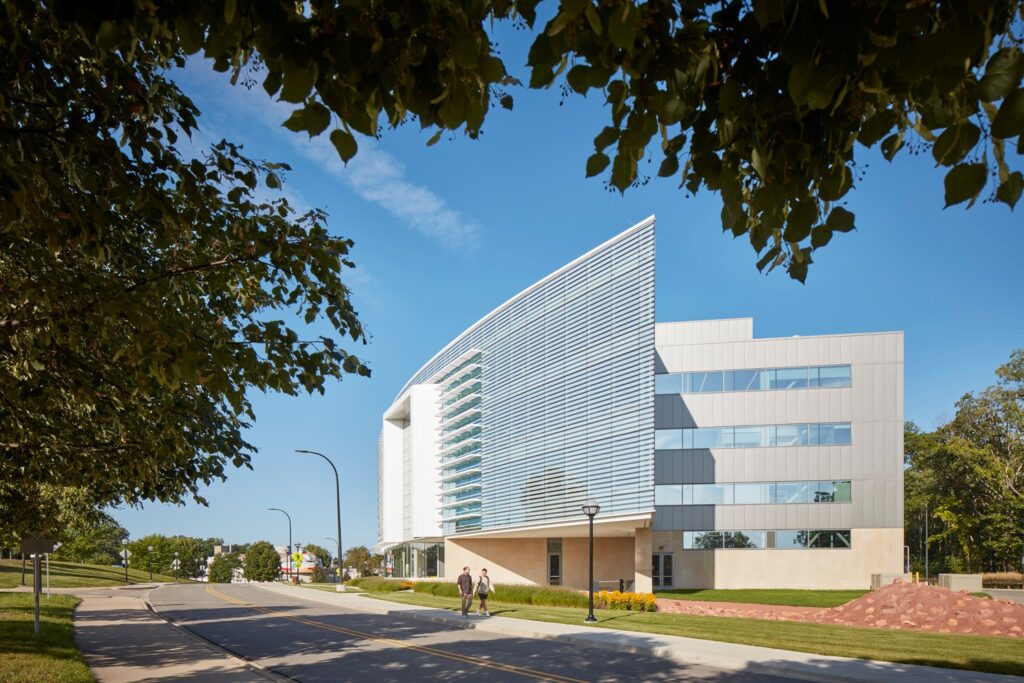
HED is an integrated design, architecture, and engineering company founded in Detroit with a Royal Oak office and a national presence, dedicated to designing high-performing, sustainable spaces that enhance lives and strengthen communities. The firm collaborates with both public and private clients to address the complex challenges of decarbonization and climate resilience. SBN Detroit interviewed Daniel Jaconetti, National Sustainable Design Leader, and Thomas Hoff, Mechanical Engineering and Sustainable Design Leader, to explore the realities of achieving net zero, what clients are prioritizing in Southeast Michigan, and where sustainability efforts must go next. Q: As we approach 2030, how realistic is the industry-wide goal of achieving net-zero operational and embodied carbon in buildings, and where are the biggest gaps today? Jaconetti: Whether or not it’s “realistic” is beside the point; the goal is what is necessary. Scientists have defined what the atmosphere can tolerate, and we’re working backwards from there. The American Institute of Architects (AIA) has set a target of net zero energy (operational greenhouse gas emissions or “carbon”) by 2030 and net zero embodied carbon by 2050. That first part — net zero energy — is readily achievable for many, if not all. However, 2030 is less than five years away, and even if we think we may fall short, we can’t take our foot off the accelerator. One of the biggest gaps right now is energy modeling. We have the tools, but too often, energy modeling is done late in the design process. If we model earlier, we can make smarter decisions upfront, decisions that shape a building’s performance for decades. Q: What trends or client demands are driving sustainability in architecture and engineering, especially in Michigan? Hoff: The most immediate driver is cost. More efficient buildings are simply cheaper to operate and easier to manage, especially when extreme weather hits. Energy efficiency and resilience go hand in hand, and that’s an easy sell. We’re also seeing more clients who want to lead by example. They’re not just aiming for code minimum; they have their own climate goals and want to build high-performance environments that align with their values. Those are fantastic clients to work with because they’re already motivated and looking to push the envelope. Q: What are the most common challenges you face when trying to decarbonize a project? Jaconetti: The biggest challenge is often understanding. There are still knowledge gaps in what “decarbonization” actually means. Sometimes clients — even large manufacturers — are under pressure from global partners to “decarbonize” but don’t know what that entails. So, we start by educating and aligning on definitions. Another issue is that the term “net zero” itself has been made confusing, sometimes defined as just being better than a baseline. That muddies the water. Let’s be honest and consistent about what we’re doing and why. This isn’t a branding exercise. It’s an existential issue for humanity. Q: How do you communicate the long-term value or ROI of sustainable design to clients focused on short-term costs? Hoff: Energy modeling is key. We can take a theoretical building and compare design options, showing exactly how much money (and energy / GHG emissions) a client might save over 5 or 10 years. It’s about shifting the conversation from low first cost to lifecycle cost (or total cost of ownership). When we model early in the design process, we can shape the building to hit more favorable payback windows and improve ROI. In most cases, you spend a little more up front and gain a lot more over the long haul. Q: Can you share a recent Michigan project that exemplifies sustainability, and what made it successful? Hoff: One great example is the renovation and addition of the Alexander G. Ruthven Building at the University of Michigan. The original building was an old museum — architecturally iconic, but outdated and inefficient. We helped transform it into a modern administrative and classroom facility, incorporating chilled beams, a VAV hot water system, and high-performance design throughout. It’s now LEED BD+C NC V4 Gold certified. Even more important: we took a forward-thinking approach to the campus’s future. Although we needed to connect to U-M’s central steam plant in the near term, we designed the systems to be able to evolve into a more efficient central hot water system in the future, to align with their long-term sustainability goals. That kind of systemic thinking is what helps make a project truly sustainable. Q: How do public vs. private sector clients approach sustainability, and how does that play out in Southeast Michigan? Jaconetti: In our experience, both sectors are committed, but the way they document and communicate that commitment can differ. Public clients are often more visible and accountable to constituents, so there’s a strong emphasis on modeling, metrics, and transparency. Private clients, especially those with ESG reporting obligations or international affiliations, can be just as rigorous. What varies most is the degree of certification or formal documentation they pursue. Hoff: In the public sector, particularly with projects like laboratories or civic buildings, the long-term horizon is often more accepted. These clients understand that resilient design can mean lower operating costs over decades — and that aligns well with public funding structures. Q: What role does retrofitting existing buildings play in decarbonization, and how does that differ from new construction? Jaconetti: As architects, we love the blank slate of new construction — it allows us to optimize everything. But the most sustainable building is often the one that already exists. About 50% of a building’s embodied carbon is in the structure. If we can reuse that structure, we’ve already made major progress. That said, we must evaluate trade-offs carefully. Upgrading systems to all-electric, for example, might not make sense if the embodied carbon of those new systems outweighs the operational benefits. Every retrofit has different variables, it’s a nuanced equation, and we have to be honest about the priorities and data behind our decisions. Q: What technologies, policies, or behaviors will be most important in accelerating
Guiding Michigan Businesses Toward Smarter Climate Action

Fresh Coast Climate Solutions is a Michigan-based climate consultancy that aims to help organizations across sectors implement sustainable, equitable, and economically viable climate strategies. Founded on deep expertise in greenhouse gas inventories, carbon mitigation, ESG, water stewardship, and circular economy principles, the company provides technical support and strategic guidance to businesses and municipalities navigating the energy transition. Fresh Coast has partnered on projects ranging from municipal benchmarking in Flint to advanced battery development in collaboration with American Battery Solutions. SBN Detroit interviewed Jenny Oorbeck and Josh Brugeman, co-founders of Fresh Coast Climate Solutions, to discuss the company’s current priorities, lessons from its recent projects, and how small and mid-sized businesses can build effective climate strategies in a fast-changing policy and economic landscape. Q: What is the impetus behind Fresh Coast Climate Solutions? Oorbeck: We launched Fresh Coast three years ago with a sense of urgency. The climate crisis felt personal and immediate, and we wanted to take the reins into our own hands. From the beginning, we focused on building a company culture grounded in bold, transformative action. That means not being afraid to push boundaries, not say no to pilot projects, and work only with partners who share our ambition and urgency. Our goal has always been impact at scale, not incrementalism. Brugeman: We’re very deliberate about engaging in projects that move the needle. That includes deploying transformative technologies, piloting new programmatic approaches, and pursuing strategies that can meaningfully shift the trajectory of climate and sustainability efforts. We’re not interested in business-as-usual—we want to help organizations lead. Q: What are the most common climate-related challenges businesses in Southeast Michigan are facing right now? Oorbeck: We’re seeing a consistent challenge among small and mid-sized enterprises. Many are under pressure—from customers, employees, and supply chain partners—to demonstrate meaningful climate action. But they often lack the bandwidth, technical knowledge, or financial resources to respond effectively. New regulations, evolving standards, and growing stakeholder expectations can feel overwhelming. They need help making informed, strategic, decisions that advance both their sustainability and competitiveness. Brugeman: For many of these companies, sustainability is becoming a prerequisite for doing business, especially if they’re part of larger supply chains. Increasingly, their clients are demanding emissions data, decarbonization strategies, and ESG transparency. The risk is real: Suppliers that don’t adapt could lose out on future contracts. That’s why we emphasize not only environmental stewardship, but also economic competitiveness and operational resilience – things like reducing energy costs or preparing for power disruptions and extreme weather events. Q: Once businesses are ready to act, what barriers tend to prevent meaningful progress? Oorbeck: The most common barriers are capacity and resources. In smaller organizations, sustainability is often an added responsibility for someone already juggling multiple roles. Without a dedicated team or financial backing, the work can stall. That’s why our Michigan Climate Wise Business Program—funded by the Erb Family Foundation—focuses specifically on helping these under-resourced companies move forward. We provide access to expert guidance so they can prioritize and implement practical solutions. Brugeman: I’d also highlight two major gaps: technical expertise and access to capital. Many businesses know sustainability is important, but they don’t know where to start. That’s where engaging external experts can make a difference. We encourage companies to look for “no-regrets” projects—efforts that cut emissions, save money, improve efficiency, and position them for future success. Q: Are there misconceptions you regularly encounter when it comes to emissions, ESG, or water stewardship? Brugeman: One of the biggest misconceptions is around timelines. Many leaders focus solely on short-term paybacks, but climate action is a long game. Sustainability isn’t just a “nice to have”—in larger organizations, it’s already embedded into operations, tied to financial incentives, and closely monitored at the executive level. Smaller companies don’t always realize how deeply integrated these issues have become, and that disconnect can be costly. Oorbeck: Agreed. Another misconception is that the pressure to act will fade, or that a few small gestures are enough. The reality is that some companies risk being dropped as suppliers if they can’t demonstrate credible sustainability progress. We need to move the conversation beyond quarterly goals and toward long-term impact. This is the defining business challenge of our time. Q: How does Michigan’s regional identity shape the way companies need to approach sustainability? Brugeman: Michigan has a unique responsibility and opportunity. We sit at the center of the largest freshwater system on the planet—yet we undervalue and underprotect this critical resource. Water stewardship should be a defining focus for our region. We also have deep roots in heavy manufacturing, which has been the economic backbone of the state. As the global economy shifts toward decarbonization, Michigan is positioned to lead—but only if we commit to building a cleaner, more sustainable industrial base. We’ve excelled at making things. Now we need to excel at making them responsibly. Q: You’ve worked with municipal governments on decarbonization strategies. What can businesses learn from those efforts? Oorbeck: I started my career in the public sector, and at times cities have led the way in sustainability, especially when support at the state or federal level has wavered. Cities began developing climate action plans more than two decades ago. Businesses can learn from those experiences: how to build internal teams, engage stakeholders, and set meaningful targets. At the same time, municipalities can learn from the agility of the private sector, especially in deploying solutions quickly. Brugeman: One thing the public sector does well is plan for the long term. That mindset is essential for climate action. Conversely, the private sector often moves faster and embraces innovation more readily. If each sector borrows from the other, we can accelerate progress. Q: What recent projects are you especially proud of and what lessons might they offer to other Michigan businesses? Brugeman: One is our Michigan Climate Wise Business Program. In partnership with Centrepolis Accelerator and supported by the Erb Family Foundation, we provide sustainability and climate services to small and mid-sized businesses that lack the internal capacity to
Remora’s Carbon Capture Technology Targets Heavy-Duty Transportation

Founded in 2020 and based in Wixom, Michigan, Remora is developing a carbon capture device designed to attach directly to semi-trucks and locomotives and collect emissions. The captured carbon dioxide is then sold to end-users, creating a potential revenue stream for fleet operators and rail companies while reducing their environmental impact. The company has raised more than $100 million in venture capital. SBN Detroit interviewed Paul Gross, co-founder and CEO of Remora, about the company’s current stage of development, the challenges of scaling climate technology, and what it takes to commercialize clean transportation solutions from Southeast Michigan. Q: You’ve raised more than $100 million in venture funding. Who’s backing Remora, and what does that support enable? A: We’ve raised $117 million to date across several funding rounds. Our latest round was led by Valor Equity Partners – they were one of the first institutional investors in Tesla, so we’re fortunate to have that kind of backing and belief in what we’re building. Other key investors include Lowercarbon Capital and First Round Capital. This kind of support has allowed us to invest in R&D and begin to partner with some of the biggest transportation companies in the world. Q: To that end, Remora has drawn interest from companies like Union Pacific, DHL, and Ryder. What does that level of engagement say about the industry’s readiness to adopt carbon capture technology, and how has it shaped your strategic approach? A: I’ve been amazed at how excited trucking and rail companies are about this technology. That level of interest tells me that the industry wants to act. They’re not just talking about sustainability – they’re ready to deploy solutions that make sense financially and operationally. That’s been the missing link. Our system retrofits onto existing vehicles, and it pays for itself by generating revenue from the captured CO₂. That’s what makes it viable for these companies to adopt at scale. Q: Where are you in terms of deployment and technology development? A: We built our first carbon capture system for semi-trucks a few years ago, and that prototype taught us a lot. Our second-generation system is now running with a truck engine and achieving 90% capture efficiency – which we consider a major milestone. We’ve partnered with fleets like Ryder, Estes, and Werner and are preparing for wider deployment. We’re also designing the system to be as compact and lightweight as possible to meet the operational needs of the industry. The scale of the opportunity is huge – there are about 2 million semi-trucks on the road in the U.S., emitting around 350 million tons of CO₂ per year. On the locomotive side, we’re developing the world’s first carbon capture system for trains and testing it right now in Wixom. We’ll begin field deployment with Union Pacific next year. Q: Remora’s approach stands out because it generates revenue through carbon capture resale. How do you see this model evolving as more companies adopt decarbonization strategies? A: There’s already significant demand for CO₂ in the U.S. – around 75 million tons are used every year, and that demand is growing. Industries like food and beverage, wastewater treatment, and sustainable aviation fuel use it, but not to scale. We’re seeing CO₂ being converted into things like hand sanitizer and laundry detergent. So, we’re capturing a waste stream and turning it into a revenue stream. In addition to selling CO₂, we also plan to sequester it underground using EPA-certified wells. There are federal tax credits supporting this, originally passed under the Obama administration and expanded under both Trump and Biden. So, whether through resale or sequestration, we have strong pathways to scale. Q: What are the biggest barriers to broader deployment? A: The biggest challenge right now is manufacturing at scale. This is the first carbon capture system ever built for a locomotive, and there’s no existing supply chain. We’re building it from the ground up, and we’re doing it mostly here in the U.S. So, the focus now is on industrializing our manufacturing process so that we can produce systems quickly, cost-effectively, and at high quality. That’s essential if we’re going to deploy these systems at the speed the climate crisis demands. Q: What advice do you have for other cleantech startups in Southeast Michigan or beyond? A: One lesson is that it’s important to demonstrate commercial demand early. A lot of engineers and scientists are working on technology solutions in this sector, but you have to make sure you’re solving a real problem that your customer has. We started talking to trucking companies on day one, even before we had a working prototype. Getting feedback early helped us design a system that met their needs, worked within their operations, and made financial sense. That kind of customer co-design has been huge for us. Q: What metrics do you track to measure impact? A: We focus on three key indicators: capture efficiency, product purity, and energy use. Capture efficiency tells us what percentage of CO₂ the system is capturing, as I said, we’re at 90% on our latest truck engine tests. Product purity matters because a lot of our CO₂ is going to sectors that need high-purity gas, like food and beverage. Energy use is the third metric. Carbon capture is inherently energy-intensive, and we’re working constantly to improve our efficiency. If the system draws too much energy, it’s not practical – so that’s a top focus for us. Q: Looking ahead, how do you see Remora’s technology integrating with broader trends in transportation, such as fleet electrification, hydrogen fuel, or grid decarbonization? A: Our technology is best suited for heavy-duty, long-haul vehicles — the sector that’s hardest to decarbonize. Electrifying a locomotive, for example, would require about 750 Tesla batteries. Building overhead electrical lines for freight rail would cost over a trillion dollars. And hydrogen still faces a lot of technical and infrastructure challenges. Within this sector, we can retrofit existing vehicles and make a meaningful dent in emissions while generating a return.