Rethinking Thermal Energy in Commercial Buildings

PowerPanel, headquartered in Oxford, focuses on sustainable energy technology with a particular emphasis on hot water systems and thermal energy capture. The company designs and manufactures modular solar hybrid systems that integrate both photovoltaic and thermal components into a single unit. Its goal is to offer energy solutions that are more efficient, durable, and economically viable for a range of commercial and industrial applications. SBN Detroit interviewed Garth Schultz, founder and president, and Oliver Buechse, who leads strategy and organizational development, about energy planning, misconceptions around renewables, and how Michigan’s engineering legacy could help shape the future of sustainability. Q: What is the impetus behind PowerPanel—what are you looking to achieve? Garth Schultz: Our work is driven by two goals – decarbonization and energy savings. We’ve developed a photovoltaic-thermal (PVT) module that combines solar electric and thermal capture in a single footprint. That means you can generate electricity while also capturing heat for domestic hot water or space heating, achieving a form of double decarbonization. We’ve paired that with a flexible hot water storage system. Water can store energy for long periods – up to 55 hours in some cases – so we’re using it as a thermal battery. The system allows for energy recovery from rooftop solar units or HVAC waste heat and redistributes it through a pump for heating needs. The components are designed for easy installation, using engineered foam and PVC linings. Oliver Buechse: By reimagining the infrastructure, we’ve been able to introduce solutions that are cost-effective, recyclable, and have longer life cycles. We’re focused on creating practical, adaptable tools for commercial facilities. Q: What are some of the most common misconceptions businesses have about adopting renewable energy, and how do these misunderstandings slow progress? Schultz: One major misconception is that renewable energy is always more expensive or only viable with significant incentives. In reality, for domestic hot water systems – especially in commercial settings – the return on investment can be very favorable. The payback period is often short, particularly when combined with existing energy efficiency measures. There’s also the belief that traditional systems are “good enough.” But if you compare life cycles, newer solutions like ours often last twice as long as standard replacements and provide better performance over time. Buechse: Another barrier is the perception that renewable adoption is driven by political pressure rather than economic value. When we talk to property owners or facilities managers, the conversation often shifts quickly once they understand the cost savings and operational advantages. Government incentives help reduce the upfront investment, but the benefits – lower utility bills, resilience, and future-proofing – stand on their own. Q: How has the conversation around energy efficiency evolved within Southeast Michigan businesses over the last decade? Schultz: There’s more awareness now. Internal sustainability mandates are common, even in sectors where they didn’t exist 10 or 15 years ago. Businesses are looking at practical ways to improve efficiency, not just for compliance, but because it aligns with their operational goals. Buechse: We’re also seeing a shift where architects and developers are integrating energy solutions from the start. They want buildings that are good for the environment and good for people. It’s not just about meeting code, it’s about delivering healthier, more sustainable spaces that people feel good about occupying. Q: When it comes to energy planning, how can businesses expand their thinking beyond electricity? What parts of the energy equation are often overlooked? Schultz: Thermal energy is often underappreciated. If you look at the average building, around 85% of total energy use goes to heating, cooling, and hot water, not electricity. But we rarely evaluate that side of the equation as thoroughly. Buechse: There’s also a broader awareness now that utility bills don’t reflect the full cost of energy. Natural disasters, insurance premiums, environmental degradation – those costs are externalized. More people are recognizing that energy efficiency also means resilience and reduced long-term risk. Technologies like geothermal or air-source heat pumps are also gaining traction. The big shift we are working toward is using energy that’s already present in the environment – or being wasted – and recapturing it. Q: In a state like Michigan, what makes energy strategy particularly challenging or unique? Schultz: Michigan has a heating-dominant climate. That creates challenges, but it also opens opportunities. In summer, a PVT (photovoltaic) unit produces both peak solar electricity and peak thermal output. That surplus energy can be stored and used later to replenish geothermal systems or supplement heating needs during the cold months. It’s about layering different technologies together—solar, thermal storage, geothermal—to create a more flexible and reliable energy strategy. Q: What trends are you seeing among commercial and industrial businesses rethinking sustainability and energy use? Buechse: It goes back to integration. For example, hospitals need to cool their operating rooms, and they also need hot water for sterilization. If these things happen on completely different systems it’s inefficient and costly. But if you can tie them together, taking energy out of the operating room and using that same energy to heat another area or make hot water you become much more efficient. We’ve worked with breweries where waste heat from tank cleaning is now being reused within the process. That reduces overall energy demand and cuts operating costs. The best part? Many of these upgrades can be implemented as retrofits. They don’t require a complete rebuild, and they create local jobs in plumbing, HVAC, and construction. Q: What role can Michigan businesses play in shaping national or global conversations around sustainable energy? Schultz: Michigan’s manufacturing legacy is a huge asset. The expertise in design, tooling, and production, especially from the auto industry, gives us a unique advantage when it comes to developing and scaling new technologies. Buechse: There’s also a mindset here around solving problems and making things work. We don’t need to compete head-to-head with global solar manufacturers on commodity products. Instead, we can offer solutions with additional value—like thermal capture and storage—and use that to differentiate ourselves. The
Sustainability in Practice at the Detroit VA

The Detroit VA Healthcare System is implementing a systemwide sustainability strategy through its Green Environmental Management System (GEMS), designed to reduce waste, lower energy consumption, and improve operational efficiency. The program recently earned Practice Greenhealth’s “Top 25 Environmental Excellence Award.” Through coordinated efforts across departments and a commitment to innovation—particularly in high-resource areas like dialysis—the Detroit VA works to demonstrate how environmental stewardship and clinical care can go hand in hand. SBN Detroit interviewed Andrew Deppner, clinical nurse manager of the hemodialysis unit at the Detroit VA, to learn more about the system’s approach and what other healthcare institutions can adopt from their progress. Q: Why do you think sustainability is such a crucial part of healthcare today? A: Sustainability is relevant to all human operations today—we’re working with finite resources, and being good stewards of those resources is imperative. That’s especially true in healthcare. The population is aging, and we’re seeing more people living longer with chronic health needs. Meanwhile, healthcare itself is becoming more expensive. That means we need to be smarter about how we allocate and use resources. At the VA, we serve 9 million–10 million veterans every year with a workforce of nearly half a million staff members. The sheer scale of our operations means our environmental footprint is significant. So our responsibility is twofold: Providing top-tier care and managing the institution in a way that honors that care through sustainability. Q: Walk me through the structure of the GEMS program. How do departments collaborate to implement sustainability initiatives across such a large system? A: GEMS operates as a committee that meets quarterly to evaluate all relevant projects—whether it’s new construction, repairs, upgrades, or procedural changes. One of our key parameters for approval is sustainability. We always ask: Can this process or improvement be made more sustainable? We also assess best practices across the larger VA health system and use that insight to inform local decisions. That structure allows us to prioritize environmental responsibility across the board while tailoring solutions to our specific needs. Q: In terms of winning Practice Greenhealth’s Top 25 Environmental Excellence Award, what do you think sets the Detroit VA apart, and what might others learn from your example? A: Honestly, it comes down to our scale and our passion. We deliver a huge volume of patient care, so the impact of our sustainability efforts is magnified. But what truly sets us apart is that our team is fully committed. Stewardship isn’t just an initiative here—it’s a value we live by. That passion influences every decision we make, and it shows up in the way we approach both large-scale projects and day-to-day operations. If there’s one thing other systems can take away, it’s that passion drives results. When your team is genuinely invested in sustainability, it shows up in your outcomes. Q: How did your team reimagine the system to reverse the traditional water-use ratio in dialysis—and are other departments applying this kind of thinking? A: Traditionally, reverse osmosis (RO) systems in dialysis operate with significant water waste, which is 60% to 80% efficient. We are working at about 98% efficiency. We achieved this by choosing a high-recovery RO system over a standard one. That decision alone results in millions of gallons of water saved each year. When we received quotes from vendors, we made high-recovery RO our top priority, even though it required more investment and more work on our end. We believed it was worth it, and our team embraced the challenge. Q: What were some of the biggest challenges you encountered when trying to drive sustainability in a healthcare setting, and how did you overcome them? A: One challenge was our water room construction project. We decided to partner with a smaller, less globally established engineering company. That meant we had to take on a larger share of the planning and preparation ourselves. The tradeoff was that we had more control over the sustainability aspects of the project, but it also required more time and resources. Despite the extra effort — more vendor coordination, more problem-solving — it paid off. We now have a highly efficient system that we believe in. It was more work, but we were willing to do it because the outcome aligned with our values. Q: How does the Detroit VA balance sustainability with the demands of clinical care, especially in high-intensity or resource-heavy departments? A: It starts with commitment. Everyone on our team is dedicated to serving our veterans. That shared purpose enables us to pursue ambitious projects without compromising care. I’ve been able to focus on our sustainability efforts because I trust my clinical team implicitly. Their professionalism and passion have freed me to work on these broader initiatives, and I know the patient care side is in excellent hands. Q: If you could share one key takeaway or piece of advice with other healthcare systems looking to follow your lead, what would it be? A: Plan ahead. You can’t foresee every variable, but the more proactive you are, the better your outcomes will be. Anticipate your resource needs early and map out the process thoroughly. If you do that, you’ll be in a stronger position to allocate budget and support before problems arise. Sustainability is about systems thinking, and that starts with good planning. Be sure to subscribe to our newsletter for regular updates on sustainable business practices in and around Detroit.
Reimagining the Pallet Supply Chain

Founded in Michigan, 3R Pallets is working to transform what can be an environmentally costly component of global logistics: the shipping pallet. The company creates reusable composite pallets made with recycled plastics and reclaimed plant fibers, designed to reduce waste and extend product lifespan, offering a scalable alternative to traditional wood and plastic models. SBN Detroit interviewed co-founder Kylee Guenther about innovation in the pallet industry, the environmental consequences, and the outlook for Southeast Michigan and beyond. Q: What was the impetus behind founding 3R Pallets? A: I’m the second-generation in my family to work in Michigan’s plastics industry—I literally grew up on the shop floor, learning from the bottom up. My dad worked on everything from one-gallon milk bottles to those little lemon-shaped juice containers. I was always fascinated by the engineering, but I was also concerned by the amount of waste I saw. As an adult, I became more focused on sustainability and how I could be part of the solution, so I decided to do something about it. That’s how 3R Pallets was born. Our goal is to disrupt the archaic wooden shipping pallet industry with the world’s most sustainable pallets. Not only are our pallets sustainable, but we help save our customers money. Traditional pallets damage and destroy product, cause production downtimes and need constant repair and endless reordering. With our drop in solution, we’re disrupting this space. We just graduated from TechStars and are the first company from Lansing to ever be accepted. It’s one of the most competitive and respected accelerators in the country. We’re also currently raising a $1.2 million pre-seed round to help onboard new customers, build inventory, and grow our team. Q: What do most people misunderstand about the scale and impact of pallet production? A: People just don’t think about them. Pallets are invisible to most consumers. They’re not something you interact with every day, so it’s hard to grasp the scale unless you’ve worked in logistics or manufacturing. Compare that to straws, bags, or plastic bottles—people have firsthand experience with those, so there’s a clear sense of impact. But over 90% of the goods we use were shipped on a pallet at some point. It’s a massive part of the supply chain that’s often overlooked. Q: With pallet use expected to increase in the next decade due to e-commerce growth, what are the biggest sustainability challenges facing the industry today? A: The first big challenge is access to materials. We’re already seeing lumber shortages in many places, and if demand doubles, costs will rise, and pressure on forests will increase. We can’t pretend there’s an endless supply of trees to meet that need. Plastic pallets are often seen as an alternative, but not all plastics can be used in pallet manufacturing. And recycling plastic isn’t a forever solution—it degrades over time. Our approach uses recycled plastic and reclaimed bamboo fibers which actually strengthens the material and increases how many times it can be reused or recycled. Q: Most wooden pallets are only used a few times before being discarded. Why has reuse or recycling been such a persistent challenge? A: The main issue is durability. Wooden pallets simply aren’t built to last. They break down after a few uses, especially when hit by forklifts or exposed to the elements. And if they’ve been fumigated, they often can’t be recycled at all. Our composite pallets can be used 50 to 60 times. They won’t degrade like wooden pallets and can be repaired or recycled when necessary. That’s a huge improvement in terms of both cost and environmental impact. Q: What is the typical lifecycle of a pallet from production to landfill, and where are the biggest environmental pain points? A: For wood, a tree is grown, cut down, milled, and nailed into a pallet. It’s sent to a distributor, then to a customer, used a few times, and if it’s damaged or treated, it goes to a landfill. Best case scenario is they enter a secondary market after being repaired and get a couple more uses. Plastic pallets are usually injection molded, often using virgin plastic. They might last for 30 to 40 cycles, then either get recycled or landfilled depending on their condition. Our pallets are different. They’re made with non-edible plant fibers with recycled plastic and molded into a durable product. They can go through 50 to 60 uses, and in many cases can be repaired or recycled again. That means fewer pallets are needed overall—and far fewer are discarded. Q: How does Michigan contribute to or feel the impacts of pallet consumption? A: We use a lot of pallets here—there’s no doubt about that. But Michigan also gives us a big opportunity because the automotive industry is one of the most forward-thinking when it comes to closed loopy supply chains. We’re already seeing traction in that space. Our value proposition is simple: help customers ship more goods with fewer pallets. That’s good for business and good for the planet. Q: How does the end-of-life of a pallet impact the total carbon footprint of a shipping operation? A: It’s huge. Most traditional wood or plastic pallets end up in landfills and producing new ones requires more energy and raw materials. That adds up. If you extend the life of a pallet and reduce the number of replacements needed, you lower emissions, reduce waste, and conserve resources. Our composite pallets are designed to be durable and recyclable, which makes the whole system more sustainable from start to finish. Q: What has innovation been like in the pallet industry? A: There truly hasn’t been a lot of innovation. Most of it is on the software side but the heart of shipping is still the pallet. Be sure to subscribe to our newsletter for regular updates on sustainable business practices in and around Detroit.
Designing for the Future: How HED Approaches Sustainable, Integrated Design Delivery
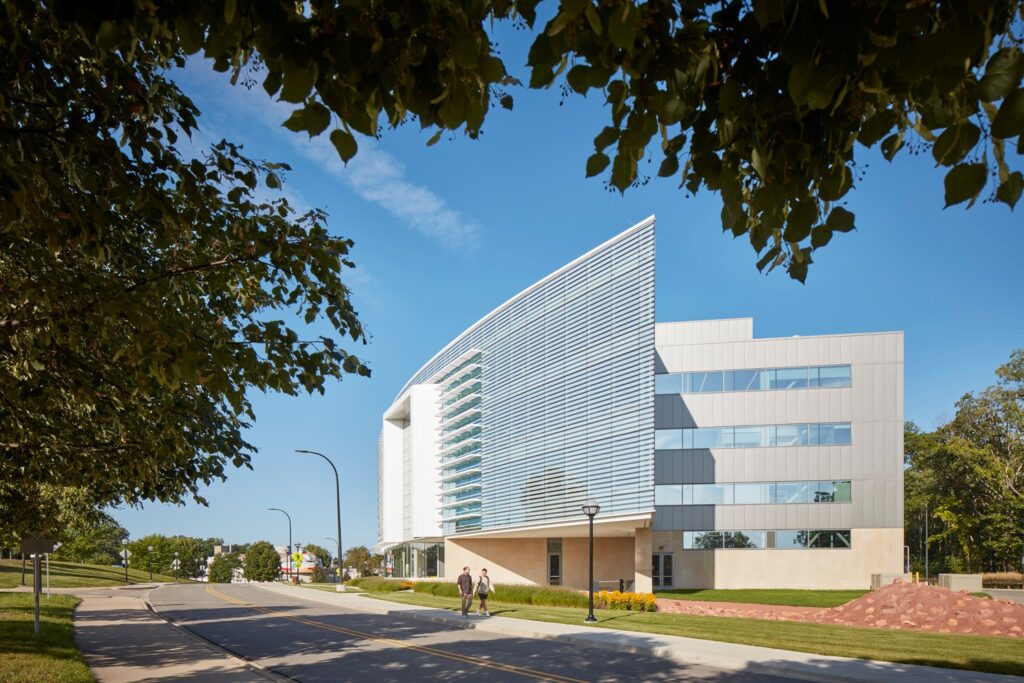
HED is an integrated design, architecture, and engineering company founded in Detroit with a Royal Oak office and a national presence, dedicated to designing high-performing, sustainable spaces that enhance lives and strengthen communities. The firm collaborates with both public and private clients to address the complex challenges of decarbonization and climate resilience. SBN Detroit interviewed Daniel Jaconetti, National Sustainable Design Leader, and Thomas Hoff, Mechanical Engineering and Sustainable Design Leader, to explore the realities of achieving net zero, what clients are prioritizing in Southeast Michigan, and where sustainability efforts must go next. Q: As we approach 2030, how realistic is the industry-wide goal of achieving net-zero operational and embodied carbon in buildings, and where are the biggest gaps today? Jaconetti: Whether or not it’s “realistic” is beside the point; the goal is what is necessary. Scientists have defined what the atmosphere can tolerate, and we’re working backwards from there. The American Institute of Architects (AIA) has set a target of net zero energy (operational greenhouse gas emissions or “carbon”) by 2030 and net zero embodied carbon by 2050. That first part — net zero energy — is readily achievable for many, if not all. However, 2030 is less than five years away, and even if we think we may fall short, we can’t take our foot off the accelerator. One of the biggest gaps right now is energy modeling. We have the tools, but too often, energy modeling is done late in the design process. If we model earlier, we can make smarter decisions upfront, decisions that shape a building’s performance for decades. Q: What trends or client demands are driving sustainability in architecture and engineering, especially in Michigan? Hoff: The most immediate driver is cost. More efficient buildings are simply cheaper to operate and easier to manage, especially when extreme weather hits. Energy efficiency and resilience go hand in hand, and that’s an easy sell. We’re also seeing more clients who want to lead by example. They’re not just aiming for code minimum; they have their own climate goals and want to build high-performance environments that align with their values. Those are fantastic clients to work with because they’re already motivated and looking to push the envelope. Q: What are the most common challenges you face when trying to decarbonize a project? Jaconetti: The biggest challenge is often understanding. There are still knowledge gaps in what “decarbonization” actually means. Sometimes clients — even large manufacturers — are under pressure from global partners to “decarbonize” but don’t know what that entails. So, we start by educating and aligning on definitions. Another issue is that the term “net zero” itself has been made confusing, sometimes defined as just being better than a baseline. That muddies the water. Let’s be honest and consistent about what we’re doing and why. This isn’t a branding exercise. It’s an existential issue for humanity. Q: How do you communicate the long-term value or ROI of sustainable design to clients focused on short-term costs? Hoff: Energy modeling is key. We can take a theoretical building and compare design options, showing exactly how much money (and energy / GHG emissions) a client might save over 5 or 10 years. It’s about shifting the conversation from low first cost to lifecycle cost (or total cost of ownership). When we model early in the design process, we can shape the building to hit more favorable payback windows and improve ROI. In most cases, you spend a little more up front and gain a lot more over the long haul. Q: Can you share a recent Michigan project that exemplifies sustainability, and what made it successful? Hoff: One great example is the renovation and addition of the Alexander G. Ruthven Building at the University of Michigan. The original building was an old museum — architecturally iconic, but outdated and inefficient. We helped transform it into a modern administrative and classroom facility, incorporating chilled beams, a VAV hot water system, and high-performance design throughout. It’s now LEED BD+C NC V4 Gold certified. Even more important: we took a forward-thinking approach to the campus’s future. Although we needed to connect to U-M’s central steam plant in the near term, we designed the systems to be able to evolve into a more efficient central hot water system in the future, to align with their long-term sustainability goals. That kind of systemic thinking is what helps make a project truly sustainable. Q: How do public vs. private sector clients approach sustainability, and how does that play out in Southeast Michigan? Jaconetti: In our experience, both sectors are committed, but the way they document and communicate that commitment can differ. Public clients are often more visible and accountable to constituents, so there’s a strong emphasis on modeling, metrics, and transparency. Private clients, especially those with ESG reporting obligations or international affiliations, can be just as rigorous. What varies most is the degree of certification or formal documentation they pursue. Hoff: In the public sector, particularly with projects like laboratories or civic buildings, the long-term horizon is often more accepted. These clients understand that resilient design can mean lower operating costs over decades — and that aligns well with public funding structures. Q: What role does retrofitting existing buildings play in decarbonization, and how does that differ from new construction? Jaconetti: As architects, we love the blank slate of new construction — it allows us to optimize everything. But the most sustainable building is often the one that already exists. About 50% of a building’s embodied carbon is in the structure. If we can reuse that structure, we’ve already made major progress. That said, we must evaluate trade-offs carefully. Upgrading systems to all-electric, for example, might not make sense if the embodied carbon of those new systems outweighs the operational benefits. Every retrofit has different variables, it’s a nuanced equation, and we have to be honest about the priorities and data behind our decisions. Q: What technologies, policies, or behaviors will be most important in accelerating
Guiding Michigan Businesses Toward Smarter Climate Action

Fresh Coast Climate Solutions is a Michigan-based climate consultancy that aims to help organizations across sectors implement sustainable, equitable, and economically viable climate strategies. Founded on deep expertise in greenhouse gas inventories, carbon mitigation, ESG, water stewardship, and circular economy principles, the company provides technical support and strategic guidance to businesses and municipalities navigating the energy transition. Fresh Coast has partnered on projects ranging from municipal benchmarking in Flint to advanced battery development in collaboration with American Battery Solutions. SBN Detroit interviewed Jenny Oorbeck and Josh Brugeman, co-founders of Fresh Coast Climate Solutions, to discuss the company’s current priorities, lessons from its recent projects, and how small and mid-sized businesses can build effective climate strategies in a fast-changing policy and economic landscape. Q: What is the impetus behind Fresh Coast Climate Solutions? Oorbeck: We launched Fresh Coast three years ago with a sense of urgency. The climate crisis felt personal and immediate, and we wanted to take the reins into our own hands. From the beginning, we focused on building a company culture grounded in bold, transformative action. That means not being afraid to push boundaries, not say no to pilot projects, and work only with partners who share our ambition and urgency. Our goal has always been impact at scale, not incrementalism. Brugeman: We’re very deliberate about engaging in projects that move the needle. That includes deploying transformative technologies, piloting new programmatic approaches, and pursuing strategies that can meaningfully shift the trajectory of climate and sustainability efforts. We’re not interested in business-as-usual—we want to help organizations lead. Q: What are the most common climate-related challenges businesses in Southeast Michigan are facing right now? Oorbeck: We’re seeing a consistent challenge among small and mid-sized enterprises. Many are under pressure—from customers, employees, and supply chain partners—to demonstrate meaningful climate action. But they often lack the bandwidth, technical knowledge, or financial resources to respond effectively. New regulations, evolving standards, and growing stakeholder expectations can feel overwhelming. They need help making informed, strategic, decisions that advance both their sustainability and competitiveness. Brugeman: For many of these companies, sustainability is becoming a prerequisite for doing business, especially if they’re part of larger supply chains. Increasingly, their clients are demanding emissions data, decarbonization strategies, and ESG transparency. The risk is real: Suppliers that don’t adapt could lose out on future contracts. That’s why we emphasize not only environmental stewardship, but also economic competitiveness and operational resilience – things like reducing energy costs or preparing for power disruptions and extreme weather events. Q: Once businesses are ready to act, what barriers tend to prevent meaningful progress? Oorbeck: The most common barriers are capacity and resources. In smaller organizations, sustainability is often an added responsibility for someone already juggling multiple roles. Without a dedicated team or financial backing, the work can stall. That’s why our Michigan Climate Wise Business Program—funded by the Erb Family Foundation—focuses specifically on helping these under-resourced companies move forward. We provide access to expert guidance so they can prioritize and implement practical solutions. Brugeman: I’d also highlight two major gaps: technical expertise and access to capital. Many businesses know sustainability is important, but they don’t know where to start. That’s where engaging external experts can make a difference. We encourage companies to look for “no-regrets” projects—efforts that cut emissions, save money, improve efficiency, and position them for future success. Q: Are there misconceptions you regularly encounter when it comes to emissions, ESG, or water stewardship? Brugeman: One of the biggest misconceptions is around timelines. Many leaders focus solely on short-term paybacks, but climate action is a long game. Sustainability isn’t just a “nice to have”—in larger organizations, it’s already embedded into operations, tied to financial incentives, and closely monitored at the executive level. Smaller companies don’t always realize how deeply integrated these issues have become, and that disconnect can be costly. Oorbeck: Agreed. Another misconception is that the pressure to act will fade, or that a few small gestures are enough. The reality is that some companies risk being dropped as suppliers if they can’t demonstrate credible sustainability progress. We need to move the conversation beyond quarterly goals and toward long-term impact. This is the defining business challenge of our time. Q: How does Michigan’s regional identity shape the way companies need to approach sustainability? Brugeman: Michigan has a unique responsibility and opportunity. We sit at the center of the largest freshwater system on the planet—yet we undervalue and underprotect this critical resource. Water stewardship should be a defining focus for our region. We also have deep roots in heavy manufacturing, which has been the economic backbone of the state. As the global economy shifts toward decarbonization, Michigan is positioned to lead—but only if we commit to building a cleaner, more sustainable industrial base. We’ve excelled at making things. Now we need to excel at making them responsibly. Q: You’ve worked with municipal governments on decarbonization strategies. What can businesses learn from those efforts? Oorbeck: I started my career in the public sector, and at times cities have led the way in sustainability, especially when support at the state or federal level has wavered. Cities began developing climate action plans more than two decades ago. Businesses can learn from those experiences: how to build internal teams, engage stakeholders, and set meaningful targets. At the same time, municipalities can learn from the agility of the private sector, especially in deploying solutions quickly. Brugeman: One thing the public sector does well is plan for the long term. That mindset is essential for climate action. Conversely, the private sector often moves faster and embraces innovation more readily. If each sector borrows from the other, we can accelerate progress. Q: What recent projects are you especially proud of and what lessons might they offer to other Michigan businesses? Brugeman: One is our Michigan Climate Wise Business Program. In partnership with Centrepolis Accelerator and supported by the Erb Family Foundation, we provide sustainability and climate services to small and mid-sized businesses that lack the internal capacity to
Natural Community Services Works to Reclaim Ecological Health in Southeast Michigan

Founded in 2009 and based in Northville, Natural Community Services provides ecological restoration and land stewardship services focused on native landscapes, habitat creation, and green infrastructure. The company works with municipalities, businesses, and nonprofit organizations across Michigan to implement science-based strategies aiming to improve ecological function and address long-term environmental concerns. SBN Detroit interviewed company cofounder Liz DeLisle and Senior Ecologist Nick Longbucco to gain insight into Southeast Michigan’s ecological challenges, how organizations are adapting their land-use practices, and what trends may shape local approaches to sustainability and restoration. Q: What inspired the creation of Natural Community Services, and what specific environmental problems were you aiming to address from the start? DeLisle: The company was founded to address growing ecological degradation in our region—things like habitat loss, urban heat islands, and unmanaged stormwater runoff. We wanted to bring attention to sustainable processes and increase education among both residents and businesses. From the beginning, we’ve been focused on designing landscapes with native plant species and building habitats for pollinators, while also encouraging community-led efforts to reconnect with and restore local ecosystems. Q: From your perspective, what are the biggest ecological challenges businesses and municipalities in Southeast Michigan are facing today? Longbucco: There are quite a few, but broadly speaking, climate change and urban sprawl are two of the most pressing. Southeast Michigan – from Detroit to Pontiac – is heavily built out, and impervious surfaces like concrete create major issues with stormwater management. Localized flooding has become a widespread concern, so implementing green stormwater infrastructure like bioretention systems and rain gardens is more important than ever. Habitat fragmentation is another challenge that often gets overlooked. As urban areas expand and natural spaces are divided, we’re seeing a rise in invasive species, along with increased pressure on the green spaces that remain. The need to protect, manage, and restore those spaces is absolutely critical. Q: How would you describe the current level of ecological literacy or awareness among business and civic leaders in Michigan? Longbucco: We’ve definitely seen growth, especially among municipalities, counties, and townships. Topics like sustainability, stormwater management, and climate adaptation are much more present in conversations now than they were a decade ago. Many of these public leaders are responding to increased interest and concern from their constituents. That said, a major gap still exists in understanding the long-term benefits and cost savings of sustainable practices. Too often, decision-makers see the upfront investment but don’t grasp the payoff that comes over time. DeLisle: Incentives can really help bridge that gap. Stormwater credits and grant funding have played an important role in encouraging businesses to explore green infrastructure. Once they see both the environmental and economic benefits, we’ve found they’re more likely to adopt and continue those practices. Q: What are the most persistent barriers that organizations face when trying to implement ecological or sustainable landscape projects? Longbucco: The biggest challenge is often a lack of funding, or even knowledge of where to look for it. Beyond that, many organizations simply don’t have in-house expertise. They may not know where to begin, how to design a project, or who to partner with. There are also regulatory hurdles. HOA rules or local ordinances may restrict things like alternative lawns or rain gardens. And from a process standpoint, getting landscape architects, civil engineers, and ecological planners to collaborate effectively can be tricky. Those groups often come from different perspectives, and aligning them early in the process is essential for successful outcomes. Q: Have you noticed any shifts in how businesses or public entities are thinking about land use, stormwater, habitat preservation, or native landscaping over the past decade? Longbucco: Absolutely. There’s been a major shift among public sector leaders, especially at the municipal level. As people in the community become more vocal about sustainability and green space, public entities are responding. There’s also been an increase in collaborative efforts – nonprofits, cities, and private organizations working together more fluidly than they used to. That’s been especially noticeable over the past five years. DeLisle: As public understanding grows, it has a ripple effect. People start asking their cities and local governments to make more sustainable choices, whether that’s through native plantings or more ecologically responsible land management strategies like prescribed burns. It’s about keeping the community happy while also doing what’s right for the land. Q: What issues or opportunities are particular to Southeast Michigan? Longbucco: Urban sprawl is definitely one of the biggest issues, along with aging infrastructure and climate change. Our region is located in a lake plain, which makes water drainage more challenging. That creates a major opportunity for green infrastructure to play a larger role in how we manage stormwater and climate impacts. There’s also a growing focus on environmental justice, ensuring that everyone has access to healthy green spaces. Both governments and businesses are starting to recognize that quality of life matters when it comes to attracting and retaining talent, and ecological stewardship plays a part in that. DeLisle: The lack of green space in industrial and urban areas is a big challenge, but it’s also an opportunity. With community engagement and the right investments, we can revitalize these areas through green initiatives that improve both ecology and public well-being. Q: Are there any recent success stories or surprising lessons you’ve seen emerge from local projects that could be instructive to others? Delisle: We’ve been fortunate to work on a number of successful public projects. Eliza Howell Park, Heritage Park in Farmington Hills, Normandy Oaks in Royal Oak, Legacy Park in Northville, and several parks for Wayne County and in Van Buren Township are great examples. In those areas, we’ve done everything from invasive species removal and native seedings to prescribed burns and long-term habitat management. One of the most exciting outcomes for these parks, as well as our Detroit River islands projects, is when monitoring data shows a clear increase in native species. They are powerful examples of how the right ecological interventions can lead to
Working to Expand Food Waste Composting in Michigan

Spurt Industries is a Wixom-based composting facility and the only EGLE-registered site in Macomb, Wayne, and Oakland counties producing STA Certified Compost, which is the Seal of Testing Assurance from the U.S. Composting Council. The company focuses on transforming food waste into high-quality compost products, working with a wide range of partners to divert waste from landfills and support healthier soils across Southeast Michigan. Through these efforts they consistently divert 15 million pounds of food waste from landfills annually. SBN Detroit interviewed Bill Whitley Jr., Owner and General Manager, and Adriana Whitley, Sales and Marketing Director, about the company’s origin, how compost is created and classified, and the importance of expanding food waste programs. Q: What inspired the founding of Spurt Industries, and how has the company’s mission evolved since its inception? A: Spurt Industries was founded in 1994, coinciding with Michigan’s yard waste ban, which required that yard waste be composted instead of landfilled. That legislation sparked the emergence of commercial composting operations in the state, including Spurt’s original facility in Grand Rapids. In 2008, a previous owner had opened a site in Wixom. We acquired the business in 2016 and have been operating fully out of that location. In Marc, we took over the SOCRRA Composting Yard in Rochester Hills, giving us two locations with roughly equal volume. This will allow us to process approximately 200,000 cubic yards of organics annually, making Spurt one of the largest composters in Michigan. Q: What does it mean to be an EGLE-registered composting facility? A: The previous process to become registered was as simple as submitting a one-page form and fee, but the state passed new solid waste laws about two years ago with new regulations. Now, the requirements are much more robust and we’re fully supportive of that shift. To operate a commercial composting site, facilities must now obtain a general permit and develop detailed documentation, including operational, fire safety and training plans, and more. We also post a $20,000 bond with the state. These measures ensure that composting is done responsibly and consistently across operators. We were involved in lobbying for these changes because we want a level playing field where materials are managed safely and sustainably. Q: What is the significance of being the only facility in Macomb, Wayne, and Oakland counties producing STA Certified Compost? A: The STA Certification is administered by the U.S. Composting Council and is one of the most rigorous compost quality programs in the country. Only four facilities in Michigan currently hold this certification, and we’re proud to be one of them. The certification process includes documenting all input materials, monitoring every compost pile weekly for temperature, moisture, and density, and conducting rigorous lab testing on finished compost. That includes testing for nutrients, metals, and pathogens, and running plant growth trials. This high standard has enabled us to sell compost to certified organic farms – and most importantly, we produce a clean product, free of plastic, glass, or metal contamination. That’s core to our mission. Q: What distinguishes different grades of compost, and how are they managed? A: Several factors influence compost quality: Feedstock: The materials used to make the compost matter. Incorporating food waste alongside yard waste increases nutrient value and mimics natural decomposition processes. Contamination and Pathogen Control: Compost must be free of contaminants and turned regularly to kill pathogens. Otherwise, it won’t meet quality standards. Chemical Maturity: Compost must be fully matured. “Hot compost” that hasn’t cured properly won’t support plant growth. Screening Method: Screen the product to remove oversized or undecomposed material. The finer the screening, the more refined the compost. Beyond quality, we’re also mission-driven to expand food waste composting. Yard waste is mandated by law, but food waste is not – and yet, Michigan sends 1.5 to 2 million tons of food waste to landfills annually. That’s a missed opportunity for soil and water quality improvement. When we apply compost to soil, it increases water absorption by about 100 gallons per cubic yard. That means less runoff, less strain on sewer systems, and fewer sewage overflows into our lakes, which is critical for protecting Michigan’s economy and tourism industry. Q: What has been the reaction from local businesses? Have you seen more interest in food waste recycling of late? A: Absolutely. While COVID-19 significantly disrupted commercial food waste collection – dropping volume by over 90% – we’ve since seen a steady rebound. We now see meaningful enthusiasm from businesses and strong policy support from the state. Michigan has a goal to cut food waste in half by 2030, and EGLE is developing a statewide roadmap that includes composting as a key strategy. Q: How does composting help mitigate climate change and support the environment? A: There are two major benefits: Methane Reduction: Food waste in landfills produces methane – a potent greenhouse gas. Composting food waste in an aerobic (oxygen-rich) environment prevents this. Carbon Sequestration and Soil Health: Compost improves soil quality and reduces the need for synthetic fertilizers, which often require long-distance transport and carry environmental costs. Applying compost also helps sequester carbon in the soil. It’s a win-win for climate and community. Q: Are there untapped opportunities for food waste diversion and composting in Southeast Michigan? A: Yes. There’s a long list. Only a few communities offer food scrap drop-off programs, and even fewer allow food and yard waste to be co-mingled. Less than 1% of restaurants and schools are currently composting, and yet these sectors produce massive amounts of food waste. We believe every business should be composting. We have found that when restaurants begin composting, they become more aware of their overall food waste and often change behavior, improving efficiency and reducing waste overall. Grocers like Meijer and Walmart have made meaningful progress in composting, but there’s still significant untapped potential for other businesses and municipalities to follow suit. Q: What are the biggest barriers to business adoption? A: Cost is one. The other is what we call the “ick factor.” Businesses
Landscape Architecture Rooted in Place, People, and Process

livingLAB is a Detroit-based landscape architecture and ecological planning firm that focuses on sustainable design rooted in place, people, and process. Through a blend of environmental expertise and community engagement, their work spans parks, green infrastructure, community gardens, and other projects with the goal of transforming urban spaces into resilient, inclusive landscapes. SBN Detroit interviewed with livingLAB’s founder, Courtney Piotrowski, to explore the region-specific challenges and opportunities of working in Southeast Michigan, and how a resident-led approach is redefining its approach to landscape architecture. Q: What was the impetus behind livingLAB, and how did the concept take shape? A: livingLAB was born from a desire to offer a more people-centered approach to landscape architecture than what we had experienced in larger, traditional firms. We believe great spaces require the collaboration of many people to build and steward them. By centering community voices and respecting the diverse neighborhoods and environments we work in, we’re able to create more impactful, meaningful spaces. Our work is rooted in community-driven values. Q: How is the field of landscape architecture evolving in response to climate change and environmental pressures? A: Sustainability has always been a foundational aspect of landscape architecture – even when early practices were focused primarily on aesthetics. As climate change has become a more urgent concern, we’ve increasingly focused on resilience and on quantifying the impact of our work. Landscape architects have long planned for dense, walkable communities, green space preservation, and low-impact development. What’s changed is the level of intentionality and the use of technology. We’re now incorporating features like green roofs, water-efficient design, and sustainable materials to reduce environmental harm and promote long-term climate resilience. In many ways, environmental thinking is inherent in our work – it’s just more explicit now. Q: What are the most pressing ecological or environmental challenges unique to Southeast Michigan that you encounter in your work? A: Much of our work is within the city of Detroit, where we frequently encounter challenges like industrial air pollution and localized flooding – especially due to more frequent and severe storms linked to climate change. Industrial activity and truck traffic create not just poor air quality, but excessive noise, and safety concerns. These are not abstract environmental issues – they directly impact residents’ health and quality of life. So, for us, it’s very much about community-centered environmental solutions. Q: Conversely, what opportunities does Southeast Michigan’s geography and ecosystem present that may not exist in other parts of the country? A: Southeast Michigan has the tremendous privilege – and responsibility – of being home to the Great Lakes, which contain 20% of the world’s fresh surface water. This region plays a critical role in protecting drinking water, ensuring recreational access, and restoring ecosystems like streams, wetlands, and forests. Our geography is a unique asset, and thoughtful environmental planning here can have an outsized impact. Q: You describe your work as resident-led. What does that look like in practice? How does that shift the process or outcomes of a project? A: Every project we take on has a community engagement component. But for us, it’s more than checking a box – we aim for true co-creation. That means understanding the goals, concerns, and lived experiences of the people who will use and be affected by the space. It shifts the outcome significantly. Projects are more likely to be used, embraced, and maintained when they reflect community priorities. For example, in our master planning work at Patton Park in Southwest Detroit, we held deep engagement sessions across many demographics and age groups. One topic that emerged was the role of public safety – what presence felt welcoming versus intrusive. Those conversations shaped design decisions and ultimately helped the community feel more connected to the changes. Q: What systemic or policy barriers make sustainable landscape design more difficult to implement at scale in this region? A: One of the biggest challenges is the fragmentation across regulatory bodies and municipal agencies. For example, the City of Detroit’s Planning Department may have goals that conflict with those of the Water and Sewerage Department. That lack of alignment creates roadblocks during implementation. Additionally, we often lack dedicated funding for green infrastructure, as well as the capacity to maintain it long-term. These barriers can stall otherwise promising projects. Q: How are equity and access being addressed—or not addressed—in landscape architecture and green infrastructure planning today? A: Equity often comes into focus around issues like green stormwater infrastructure. Historically, urban communities have borne the brunt of climate-related issues like flooding or heat islands. Over the past 13 years, we’ve seen significant strides in bringing equity into the conversation. But that progress is fragile. Much depends on political will and continued investment. We also must rebuild trust with communities that have historically been left out of these processes. The current political climate, with its emphasis on dismantling equity-focused initiatives, presents a real challenge. Q: If you could implement one major change in how we design and manage land in Southeast Michigan, what would it be – and why? A: We need to rethink how we address housing and transportation because those two areas are deeply connected to land use, sustainability, and community health. Expanding access to affordable, climate-resilient housing that is connected to transit would be a game-changer. Smart land use policy must consider both housing equity and climate adaptation if we want to build healthy, inclusive, and economically resilient communities. That’s the secret sauce. Be sure to subscribe to our newsletter for regular updates on sustainable business practices in and around Detroit.
Rethinking Water in a Changing Climate

Ann Arbor, Michigan-based LimnoTech is an environmental science and engineering firm with more than 50 years of experience with water-related issues. The firm works with public agencies, private industry, and nonprofit organizations to provide science-driven solutions to complex water challenges. SBN Detroit interviewed Brendan Cousino, PE, Principal and Senior Civil & Environmental Engineer at LimnoTech, to discuss the region’s most pressing water infrastructure challenges and where he sees the biggest opportunities for improvement. Q: What is the impetus behind LimnoTech? A: LimnoTech was founded by graduate students at the University of Michigan over 50 years ago. At the time, the country was just beginning to grapple with water pollution and how to treat contaminated waterways. This was also the early age of computing, and the founders began using computer-based modeling to better understand and solve environmental problems. Essentially, they were a crack team of water quality modeling experts who turned their research into a business that provides real-world environmental solutions. Q: With increasing climate variability, how do you approach designing water management solutions that are both adaptable and future-proof? A: To be future-proof, everything must be adaptable. We’re facing longer drought periods and increasingly intense rainfall events – sometimes in very short time frames. These extremes are becoming more common, and we’ve seen the consequences play out across Michigan. Our approach is to stay aligned with the latest climate science, evaluate the full range of projected conditions, and design infrastructure that can perform under both extremes. Q: What are some of the most pressing water-related challenges facing Southeast Michigan today, and how do they compare to other regions? A: Southeast Michigan is dealing with aging infrastructure systems that were built for historical conditions – not today’s climate realities. The recent Great Lakes Water Authority pipe break in Southwest Detroit is one example. Urban flooding and stormwater management are key issues, as is legacy pollution from our industrial past, compounded by new threats like microplastics, and PFAS. At the same time, Michigan is unique in its abundance of freshwater, much of it in relatively clean condition. That puts a responsibility on all of us to protect these globally significant resources. Q: Conversely, what are the biggest opportunities in Southeast Michigan for improvement and is there any low-hanging fruit? A: In many ways, we’ve already picked the low-hanging fruit. For example, our region has been ahead of the curve when it comes to combined sewer overflow treatment. Investments made in the ’90s and early 2000s, such as retention basins and treatment systems, have made a real difference in improving water quality in the region. Many of the pollutant sources in our stormwater are more broadly distributed. What’s next is being more strategic to plan infrastructure investment. We’re using better data and technology to monitor conditions. For example, we can now use robotics to inspect pipes so we don’t have to wait for them to fail, and real-time monitoring to inform operations during wet weather. That allows us to make smarter, targeted investments to prepare for changing conditions. Q: What innovative strategies or technologies are emerging to help cities like Detroit handle extreme weather events and stormwater management? A: Big data and real-time system operations are making a huge difference. With improved forecasting, operators can anticipate where rainfall is headed and adjust pump systems and treatment infrastructure in advance. We’re also using high-resolution 2D modeling to understand where water will accumulate during storms. That allows us to plan better and pinpoint risk areas. It’s transforming how we manage and design urban stormwater systems. Q: You worked extensively on the Ralph C. Wilson, Jr. Centennial Park on the Detroit riverfront. What specific water-related challenges did this project address, and how does it serve as a model for future waterfront development? A: The site had a number of infrastructure issues. There was legacy sediment contamination from industrial activity that had to be remediated to support a healthy aquatic ecosystem. The bulkheads along the river also were failing, creating dangerous sinkholes. We replaced those with new shoreline stabilization measures. We also incorporated aquatic habitat restoration into the project. The result is a world-class park that improves the riverfront for people while also addressing serious environmental concerns. It’s a great example of how community projects and infrastructure improvements can work hand in hand. Q: Infrastructure in Detroit is aging and often not designed for today’s environmental pressures. What are the biggest gaps in water infrastructure that need to be addressed, and what solutions exist? A: Much of the infrastructure was designed for storm conditions that were expected to occur once every 10 years. Now we’re seeing those types of storms almost every year, at least in some locations within the region. Our stormwater systems simply weren’t built to handle that level of intensity and frequency. The biggest gap is funding. Many systems are at or beyond their design life, but utilities don’t have the financial resources to replace them quickly. We need to identify failure points, understand what’s most vulnerable, and prioritize investment accordingly. Q: What role do community engagement and education play in developing effective climate resilience projects? A: Community engagement is a core part of most projects we work on. It’s essential that the infrastructure improvements we make actually serve the people who live there. When communities have a voice in the design process, the outcomes are better. Education also is key. Whether it’s installing a rain barrel, planting native species, or simply understanding how the stormwater system works, individual actions can add up. If we can manage even the first half inch of rainfall before it enters the storm system, we reduce the reliance on aging infrastructure. Q: Looking ahead, what do you see as the biggest opportunities for improving climate resilience and sustainable water management in the next decade? A: One major opportunity is the shift we’re seeing from purely regulatory compliance to voluntary corporate action. Many of our corporate clients are taking the initiative to reduce their water impacts. That’s a
Sustainability in Real Estate: CBRE’s Strategy for a Lower-Carbon Future

With roots tracing back to 1906, CBRE is a global real estate services firm specializing in property sales, leasing, financing, facilities and property management, valuations, investment management, and development across various industries. With a strong presence in Detroit and Southeast Michigan, the company plays a key role in shaping the region’s commercial real estate landscape. SBN Detroit interviewed Tommy Bledsoe, Senior Sustainability Specialist at CBRE, about the company’s sustainability strategy, the hurdles in decarbonizing real estate, and the trends shaping the future of sustainable property management. Q: How does CBRE approach sustainability? A: CBRE’s goal is to create long-term value for the company and its clients by accelerating sustainability initiatives. This commitment extends across CBRE’s operations as well as the properties it manages and develops. The company has set a net-zero greenhouse gas emissions target by 2040, covering corporate operations, real estate management and development, and supply chain activities. Since most of these emissions come from properties managed on behalf of clients, CBRE’s success depends on strong collaboration. To meet this challenge, CBRE has built end-to-end sustainability capabilities that help the company and its clients transition toward a lower-carbon future. Since 2019, we’ve reduced absolute emissions by 18 percent across Scopes 1, 2, and 3. Q: CBRE has set ambitious sustainability targets, but what are the biggest challenges in reducing emissions across managed properties and assets? A: One of the biggest challenges is the need for partnerships with property owners. While CBRE plays a key role in managing properties, major sustainability investments and operational changes require approval from the building owners themselves. To address this, CBRE takes a consultative approach, helping guide decision-making with data-driven recommendations that align financial benefits with sustainability outcomes. By demonstrating how sustainability investments enhance asset value and operational efficiency, the company works to gain buy-in from property owners and support long-term emissions reductions. Q: With nearly 97 percent of CBRE’s total emissions coming from property management and development, what strategies are in place to address and decarbonize these areas? A: Since 2019, CBRE has reduced emissions across property and facility management by focusing on four core areas: Maximizing resource efficiency through energy efficiency projects Expanding the adoption of renewable energy Reducing reliance on fossil fuels through electrification Decarbonizing the supply chain by working closely with vendors CBRE has also strengthened its sustainability capabilities through strategic partnerships. The company has a global collaboration with Deepki, a leader in ESG data management, and has expanded its renewable energy expertise by acquiring NRG’s renewable business. Additionally, CBRE is investing in learning and development programs to ensure employees – especially those outside of sustainability roles – have the knowledge needed to effectively advise clients. Q: Many companies struggle to balance sustainability goals with financial concerns. How does CBRE demonstrate the business case for sustainability to property owners and investors? A: We discuss the financial benefits of sustainability with our clients frequently, and the data consistently shows that sustainability investments are good for business. Buildings that incorporate sustainability measures tend to generate higher operating income, with many commanding an increase in rental premiums of up to four percent in the office sector. Additionally, these properties operate more efficiently, leading to lower utility and maintenance costs. Market demand is also increasing. A CBRE survey of office occupiers found that 66 percent of tenants prioritize sustainable building features, making it the most commonly cited amenity preference. Properties with strong sustainability credentials also tend to resell at higher values, making sustainability a key differentiator in long-term asset performance. CBRE works closely with clients to provide data-driven insights and present projects that align both financial and environmental benefits. Q: What industries or property types present the biggest challenges for sustainability initiatives, and how does CBRE tailor solutions to different clients? A: The biggest challenge isn’t necessarily the type of property, but rather the lease structure. Industrial and retail properties, for example, often operate under triple-net leases, where tenants – not property owners – are responsible for utility costs. This creates a scenario where landlords may hesitate to invest in sustainability upgrades if tenants receive most of the financial benefits. As a property manager, CBRE sits at the nexus between owners and tenants, putting the company in a unique position to bridge this gap. We work to align interests by educating tenants on green initiatives, offering sustainability services that collect and analyze utility data, and identifying mutually beneficial sustainability projects. By facilitating collaboration, CBRE helps landlords and tenants find common ground on sustainability investments. Q: Speaking of collaboration, how does CBRE work with suppliers, contractors, and municipalities to ensure sustainable building practices? A: CBRE’s sustainability efforts extend beyond property owners and occupiers to include suppliers, contractors, and industry organizations. The company is an active member of industry groups such as the U.S. Green Building Council and the Building Owners and Managers Association. Additionally, CBRE enforces a supplier code of conduct that ensures vendors align with socially and environmentally responsible commitments. Q: Many older buildings were not designed with energy efficiency in mind. What strategies does CBRE use to retrofit and modernize legacy properties? A: Retrofitting existing buildings is a major focus, particularly since an estimated 80 percent of today’s buildings will still be in use by 2050. Achieving a sustainable built environment requires upgrading these properties rather than relying on new construction alone. We begin by assessing a building’s baseline performance, using software tools to analyze energy consumption and model potential retrofit pathways. Engineers conduct on-site evaluations to identify efficiency opportunities, and findings are compiled into asset-specific sustainability action plans. Q CBRE operates globally. How do sustainability priorities and challenges differ across regions, specifically Southeast Michigan? A: We see a lot of regional differences and nuances. Regulations vary by region, and in Southeast Michigan, local policies play a key role in driving sustainability efforts. Both Detroit and Ann Arbor have energy and water benchmarking policies, requiring properties of a certain size to report consumption data. While benchmarking is common nationwide, some cities and states