Building with Purpose
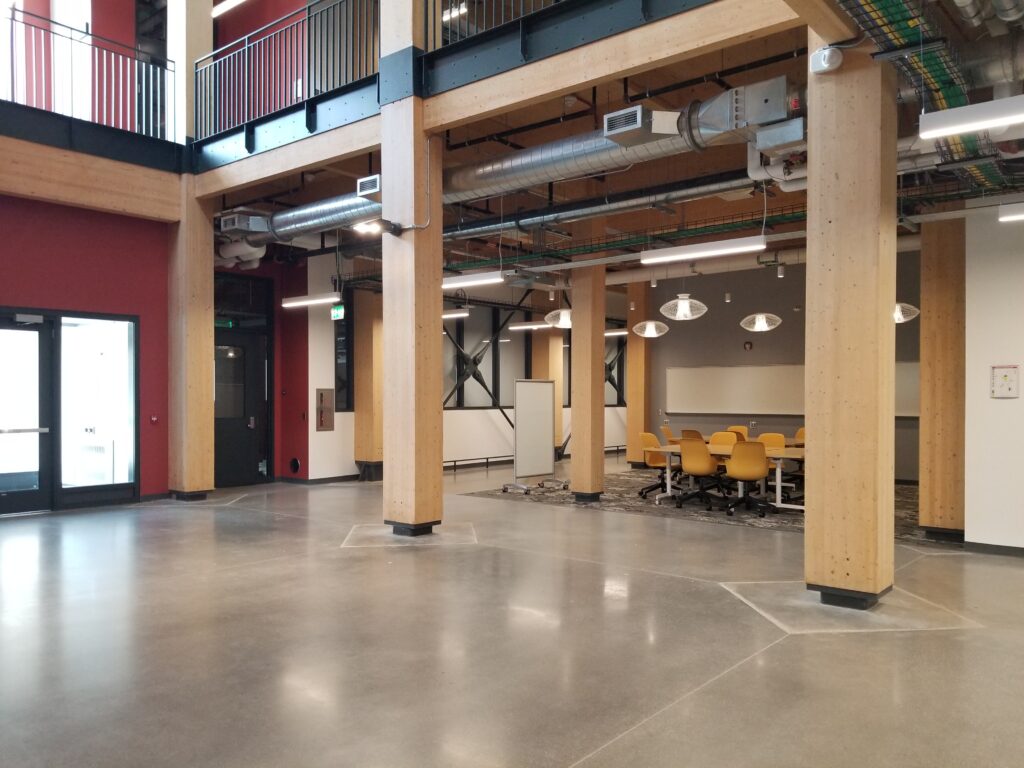
MassTimber@MSU is a cross-disciplinary initiative at Michigan State University dedicated to advancing mass timber construction and manufacturing in Michigan. Collaborating with partners across construction, forestry, development, and state agencies—including the Michigan Department of Natural Resources—the initiative leverages MSU’s land-grant mission through research, teaching, stakeholder engagement, and policy development to build a sustainable mass timber future for the state. SBN Detroit interviewed Sandra Lupien, Director of MassTimber@MSU, about the environmental, economic, and design implications of mass timber and the growing momentum behind the material in Michigan and beyond. Q: What is the MassTimber@MSU initiative, and what inspired its creation? A: MassTimber@MSU is a collaboration across MSU’s School of Planning, Design and Construction, Department of Forestry, and MSU Extension. We work with partners across the state—including construction professionals, foresters, community and development organizations, and state agencies like the Michigan Department of Natural Resources—to advance mass timber construction and manufacturing in Michigan. Our approach reflects MSU’s land-grant mission: research, teaching and curriculum development, stakeholder engagement, and policy exploration that could support mass timber adoption. Since I started in this role in July 2021, momentum is growing. There are now more than 65 mass timber projects in the pipeline in Michigan. The STEM Teaching and Learning Facility on MSU’s campus, which is the second building in the state to use cross-laminated timber (CLT), helped demonstrate what’s possible. And we’re now seeing serious interest from prospective producers who are looking to locate in Michigan. Q: What are the environmental benefits of mass timber in terms of sustainability, carbon reduction, and climate resilience? A: This is exactly what drew me to mass timber. It’s a tool in our toolkit to reduce carbon emissions, support sustainable communities, and help foster healthier, more resilient forests. Globally, the built environment accounts for about 39% of greenhouse gas emissions—28% from building operations and 11% from construction materials like concrete, steel, and glass. These materials are essential, but they’re energy-intensive to produce. Wood, by contrast, is a renewable resource that stores carbon. When we use wood in construction, we’re not only lowering a building’s embodied carbon footprint—we’re also locking that carbon into the structure itself. At MSU, the STEM Teaching and Learning Facility contains roughly 3,000 cubic meters of mass timber, which stores about 1,856 metric tons of carbon dioxide equivalent. That’s comparable to removing the emissions from 4 million miles driven by an average car. Mass timber buildings, in this way, become carbon storage banks. On the forestry side, we know that many forests evolved with low-intensity natural fires that helped maintain healthy densities. Today, many of our forests are overcrowded, which makes them vulnerable to pests, disease, and catastrophic wildfire. Because of past logging practices and fire suppression, we have an obligation—and opportunity—to steward forests more sustainably. When we do that, we can produce wood that extends the climate benefits of trees, especially if that wood would otherwise decay or burn. Q: How are MSU students and faculty engaging with mass timber—from design to research to real-world application? A: There are three main academic areas deeply engaged with mass timber: Construction Management, Forestry and Biochemistry, and Civil and Environmental Engineering. We have undergraduates, master’s students, and Ph.D. candidates working with faculty on projects across those disciplines. In Construction Management, Professor George Berghorn is developing mass timber curriculum modules that can be used nationally in engineering and construction programs. In Forestry, Professor Mojgan Nejad is doing incredible work on developing bio-based adhesives and coatings for use in mass timber—replacing fossil-fuel-based polyurethane with lignin-based alternatives. She’s actively working toward commercialization. We’ve also done economic research to analyze supply chains and survey demand, which helps inform developers and policymakers. And beginning Spring 2025, we launched a new course focused entirely on mass timber, led by Dr. George Berghorn and tailored for both undergraduate and graduate students. Q: From an economic perspective, how could mass timber help revitalize Michigan’s forestry sector and rural economies? A: We’ve modeled the economic impacts of launching a 50,000-cubic-meter-per-year mass timber manufacturing facility in Michigan. The results are exciting: such a facility would contribute $152 million to the state’s GDP and support 318 jobs. There’s a strong need to find new uses for Michigan wood. With the paper industry in decline and other traditional markets shifting, mass timber presents an opportunity to create high-value products that support Michigan jobs and rural economies. Q: How does the initiative align with Michigan’s climate goals or sustainable development strategies statewide? A: The MI Healthy Climate Plan, which outlines the state’s climate goals, directly mentions mass timber three times—as a key strategy for reducing emissions in the built environment and managing natural lands sustainably. The City of Lansing’s Sustainability Action Plan also highlights mass timber, and East Lansing has even amended its zoning ordinance to incentivize developers to use mass timber and build LEED-certified projects. It’s encouraging to see this kind of policy support—it sends a signal that mass timber can and should be part of Michigan’s climate solution. Q: What does Michigan’s existing forest resource look like, and how does sustainable forestry tie into your vision? A: Healthy, resilient forests are the foundation of everything we do. In Michigan, about 70% of our forest resource is hardwood and 30% is softwood. Most mass timber products currently certified for use in the U.S. are made from softwoods. That said, Michigan does have suitable softwood species. For example, red pine was certified for structural use because the Michigan DNR prioritized using Michigan wood in a customer service building in the Upper Peninsula. That’s a great example of state leadership driving local wood utilization. As the industry evolves, there’s potential to expand the species we can use in mass timber production. Q: Looking ahead five to ten years, what’s your boldest vision for the impact of the Mass Timber Initiative? A: I’d like to see commercial buildings—everything from multifamily housing to community centers to industrial facilities—considering mass timber from the outset, not as a novelty but as a viable, mainstream option. Mass timber
Aligning Business with Sustainability
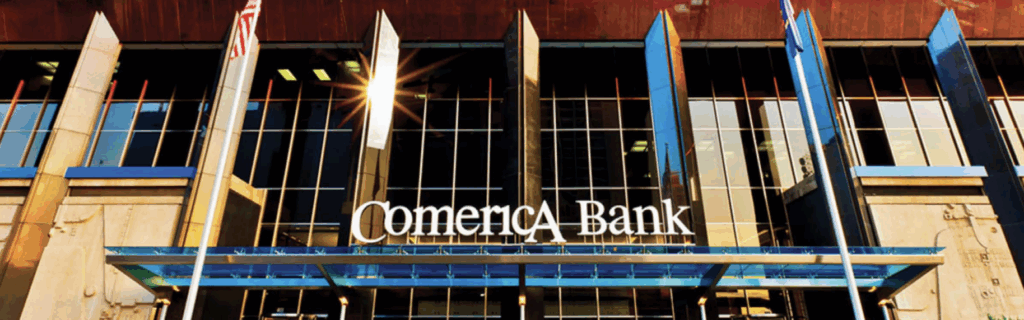
Comerica Inc. was founded in Detroit in 1849 and remains rooted in Southeast Michigan, even as its headquarters now sit in Dallas. With 4,300 employees in the region and a strong presence across the state, the bank continues to play an active role in environmental responsibility and community impact. SBN Detroit interviewed Scott Beckerman, Senior Vice President and Director of Corporate Sustainability, about the bank’s climate strategy, operational footprint, and the role financial institutions play in driving sustainable progress. Q: Comerica has deep roots in Detroit, even as its headquarters are now in Dallas. How does that legacy influence the bank’s sustainability priorities in Southeast Michigan and beyond? A: Comerica is really proud of our 175-year legacy in Detroit, and over half of our employees are here. As a lifelong resident of the Detroit area myself, I recognize the unique environment of this region. So naturally, there is a certain connection to our desire to protect and preserve this special environment. But we also know that environmental issues aren’t just local – they are global in their nature. I think the connection here is that we understand the importance of issues in the near-term and at the local scale but also recognize the importance of the global scale. For issues like climate change, that means our future success depends on the actions we are taking today, both here in the Detroit area and across the country. Q: What are the most pressing environmental or climate-related risks Comerica is working to address within its operations and client services? A: Our commitment is around three main areas: Reducing our own environmental footprint, embedding sustainability into our business, and supporting our customers’ needs. For our own footprint, we are focused on reducing water consumption, waste generation, resource consumption, and greenhouse gas emissions. Since 2012, we’ve reduced our GHG emissions 61%, – on our way to a 65% reduction target by 2030 and moving toward our north star of 100% reduction by 2050. For water, we’ve decreased our consumption by 48% and have also seen a 41% reduction in waste. On the resource consumption side, our focus is paper usage and since 2012 we’ve decreased that by 89%. For our customers, we want to ensure they have access to the financial products and services they need to address the challenges they face. Maybe for a homeowner, that is a home equity loan to make their home more energy efficient or add solar to their roof. For a business, that may mean providing the financing to upgrade the efficiency of their equipment or capital improvements to a building to make it more climate resilient. Q: Comerica has made commitments to reduce operational emissions and increase energy efficiency. Can you walk us through the key strategies being used to reach those goals — and how success is measured? A: Our primary drive has been a focus on energy efficiency. With roughly 400 buildings in our portfolio, this is no easy task, and no two buildings are alike. We’ve deployed a host of efficiency measures from lighting to advanced building controls to really working on driving down energy consumption, which is the largest contributor to our greenhouse gas emissions. The other important thing is to right-size our real estate footprint while still serving our customer needs. A lot has changed with the digitalization of banking, and we simply don’t need the same amount of space that we needed in the past. So being smart about the amount of real estate we occupy has also helped us drive down our overall energy consumption. At the same time, we recognize that the shift to a digital world is not without its own set of issues, including GHG emissions, so we work with providers to ensure the majority of our technology and data center needs are powered by renewable energy. We’re also investing in renewable energy solutions across our footprint, focused on local impacts, including piloting solar projects and REC (renewable energy certificate)-backed electricity programs in Michigan and Texas. Q: What role does Comerica’s sustainability team play in engaging business units across such a large organization? How do you ensure consistency in implementation? A: First, we center our sustainability program on value creation. What I mean by that is that our sustainability initiatives need to be generating value by reducing risks or costs, spurring innovation, and supporting revenue growth. If we do all that well, it enhances our reputation and brand which delivers additional value. While it may be cliché, I think it’s true that sustainability really is the ultimate team sport. We are successful with our programs because we have the buy-in and support from colleagues across our organization. We also support sustainability through colleague education, regional Green Teams, and volunteer-driven community programs. Q: In your view, what’s the biggest challenge for banks — especially legacy institutions like Comerica — when it comes to embedding sustainability into the core business model? A: For any business, there are a ton of ever-evolving business priorities, based on things like the market, customer needs, regulatory requirements, and changing technology. So, if you approach sustainability as an add-on to the traditional business priorities, then it can get pushed aside by pressing traditional business needs of the moment. But if you embed sustainability into your core values and it becomes a part of how you do business, then it becomes a long-term source of business stability. At Comerica, we have a core value of being “A Force For Good,” which means we’ve worked to embed sustainability into how we do business. Since the establishment of our sustainability office in 2008, that means we’ve significantly reduced our environmental footprint and delivered tens of millions of dollars of cost savings. Q: Where do you see the greatest opportunity for Comerica to lead — whether through lending practices, investments, community partnerships, or internal operations? A: Our length of time in this space has given us a real advantage in terms of long-term impacts. During that time,
Identifying Opportunities for Improved Efficiencies

The Energy Alliance Group of North America focuses on helping businesses implement sustainable energy solutions by identifying opportunities for improved efficiency and connecting clients to funding and technology. Based in Ann Arbor, Michigan, the company collaborates with commercial and industrial property managers to reduce energy consumption, enhance operations, and achieve long-term cost savings. SBN Detroit interviewed Scott Ringlein, founder, principal, and Chief Strategy Officer, about energy efficiency in Southeast Michigan, the role of financing and audits, and the importance of long-term thinking when it comes to sustainability. Q: What are the biggest energy efficiency challenges facing commercial and industrial buildings in Southeast Michigan? A: Misinformation is one of the biggest challenges. Every building has the opportunity to implement energy efficiency improvements, and there is money available to make it happen. These improvements offer a return on investment, but many building operators and owners either don’t believe the numbers or assume they don’t apply to them. The truth is, utility costs are ongoing and only getting higher, so the only way to gain control is to improve your building’s efficiency. Q: How can businesses identify when it’s time to upgrade or retrofit their energy systems A: Start by knowing what you have—what systems are in place, their expected lifespan, and their maintenance history. If you’re seeing frequent repairs and higher maintenance costs, it’s time to look at alternatives. Then evaluate how much more efficient a new system could be and what kind of energy savings it could deliver. If the numbers make sense, that’s the signal to move forward. Unfortunately, many businesses struggle with that last step—deciding to invest. Q: What misconceptions do you commonly encounter around cost recovery or energy savings? A: Many building owners don’t believe the projections—even when we show them data that supports a positive cash flow within one or two years. They tend to focus solely on ROI and forget that utilities never go away. You’re always going to pay for water, electricity, gas—whatever it is. And the utility companies have no vested interest in lowering your costs. So even if you’re skeptical, you’re still going to be paying more year after year unless you act. Q: How has the financing landscape changed for energy upgrades—especially for nonprofits or small businesses? A: We’ve been in this space since 2012, and the financing options today are better than they’ve ever been. Tax credits will come and go, but there are more long-term tools now than there were a decade ago. Michigan has been a leader in this area. Programs like Michigan Saves were the first of their kind in the U.S. We’re also a state approved for Property Assessed Clean Energy (PACE) financing, although it’s underutilized here compared to states like California. Still, the options are out there—you have choices, and you can take control. Q: What role do energy audits play in long-term planning, and how often should they be conducted? A: Audits are essential. You need to know where you stand—what equipment you have, how efficient it is, and what condition it’s in. It’s surprising how many clients have never even been on their own roof, where all the major equipment is housed. There are different levels of audits. A Level 1 audit gives you a basic understanding of what you have and where you’re spending your money. A Level 3 audit goes deeper and is useful when you’re preparing to make major decisions—like process changes or equipment replacement. A challenge is that many companies don’t take the time for a comprehensive audit until it’s too late. Smaller organizations may lack the staff, and larger ones may lose visibility due to scale. But without that baseline, long-term planning is difficult. Q: How do Southeast Michigan’s climate swings shape energy strategy in the region? A: As an organization, we don’t use climate change as the primary argument for doing the right thing. Climate change is happening, but we believe the conversation around energy efficiency should be happening regardless. You’re spending money on utilities – and there are better systems and more efficient ways to operate. We also need to think long-term. In the U.S., we don’t treat these upgrades as long-term investments the way they do in Europe or Asia. There, the systems are central to the building’s value and are maintained accordingly. Here, we often focus too much on short-term costs instead of building for performance and sustainability. Q: What advice do you have for businesses looking to reduce costs and improve operations going forward? A: Real-time monitoring of building systems from a central location gives you visibility and control. Beyond that, the cost of implementing technologies like LED lighting, heat pumps, solar panels, and combined heat and power (CHP) systems has become very feasible. There are also integrated systems now—solar light poles with battery storage and surveillance, for example—that operate independently of utility companies. The key is maintenance. These systems don’t last forever if they’re neglected. But with built-in monitoring and upkeep, they can be powerful tools for cutting costs and improving resilience. Be sure to subscribe to our newsletter for regular updates on sustainable business practices in and around Detroit.
Driving Sustainable Innovation in Mobility

ZF Group, a global technology company with its North American headquarters in Northville, specializes in systems for passenger cars, commercial vehicles, and industrial technology. With a focus on next-generation mobility, the company develops solutions that address electrification, automation, and digitalization while aiming to improve safety, efficiency, and sustainability in transportation. SBN Detroit interviewed Anuj Shah, Sustainability Lead, for the Americas, to explore the most pressing environmental challenges in the region’s mobility and manufacturing sectors – and how technology, collaboration, and design innovation are shaping a more sustainable future. Q: What are the most pressing sustainability challenges facing the mobility and manufacturing industries in Southeast Michigan today? A: One of the biggest challenges is decarbonizing our complex supply chains. To give you an idea of scale, ZF in North America alone has about 3,700 direct suppliers, and as you move further upstream, that number multiplies. Many Tier 2 and Tier 3 suppliers lack the tools and resources to track, manage, and reduce emissions. ZF is driving progress in this area through our supply chain sustainability program and to support our supply base, we have established a supplier sustainability training academy that offers trainings around several topics like responsible sourcing, use of green electricity and how to meet requirements set forth in our sustainability bid conditions. It is a fundamental change in philosophy in how we interact with our suppliers in the development of products and processes, and in the choices we make. Another challenge is sourcing sustainable materials. As demand for magnets and critical raw materials rises, our commitment to responsible sourcing – guided by human rights and environmental due diligence policies – becomes even more critical. Ideally, we start with using less, then designing products that can accept higher recycled content materials, and where technically feasible, designing with circularity in mind to provide access to these materials to bring them back into the loop. Q: As the auto industry shifts toward electric and digital systems, where do you see the biggest opportunities for companies in Michigan to lead in sustainable innovation? A: I see two major areas of opportunity. First, digital twins and predictive sustainability. With advances in AI, IoT and cloud computing, we continue to gain the ability to simulate and optimize sustainability across a product’s entire lifecycle. Michigan companies have the potential to drive breakthroughs here, unlocking real-time emissions tracking, predictive maintenance, and more circular design outcomes. At ZF, for example, our SCALAR platform provides real-time diagnostics to fleet operators. It’s a fleet management solution that offers remote diagnostics on vehicle health using smart sensors, telematics, and predictive maintenance that combines historical and live data to forecast potential failures and propose proactive maintenance. Second, there’s room for innovation in product design that balances cost, supply chain resilience, and sustainability, like reducing reliance on rare earth magnets. For example, ZF’s Separately Excited Synchronous Motor (SESM), a magnet-free e-motor technology. Q: How important is collaboration across suppliers, OEMs, government, and academia in accelerating sustainable progress? A: Collaboration is essential. The scale and complexity of sustainability challenges demand system-level thinking and collective action. Collaboration can take many forms, and start with small steps by sharing common standards, targets, and data. This enables clarity and provides a common language when working to decarbonize the value chain and develop more circular materials. Collaboration can also help leverage scale through greater partnership between OEMs and suppliers to take advantage of installed capacities and build upon existing competencies to lower cost and increase re-usability of infrastructure. This requires strong feedback loops between industry partners, sometimes requiring flexibility in design parameters to accommodate available off-the-shelf solutions. Some examples at ZF: We engage with our suppliers around ESG Goals, best practice sharing, and sometimes co-developing decarbonization roadmaps. We also work with external organizations like MEMA and AIAG, providing inputs on policy, contribute to white papers, and align on best practices on various topics like human rights and supply chain transparency. These platforms are critical for creating a consistent approach across the industry. Q: The mobility industry is under growing pressure to quantify and reduce emissions. How is the conversation around Scope 3 evolving, and what tools are helping drive accountability? A: The conversation around Scope 3 has evolved rapidly, from awareness to tangible action. Just a few years ago, many companies were working to define and estimate these indirect emissions. Today, Scope 3 is front and center, especially in the automotive industry, where upstream and downstream emissions make up the majority of a company’s emissions. At ZF, we’re approaching Scope 3 with a focus on data integrity, supplier engagement, and cross-industry collaboration Transparency and supplier engagement are key. We are systematically working to move away from secondary emissions data and working closely with our suppliers to gather more accurate product-specific emissions data. This is critical for building trust and accountability across the value chain. Regarding our emissions, disclosure alone isn’t enough; our stakeholders expect us to present clear decarbonization roadmaps. Many of our customers have also defined product-level and material-level carbon footprint targets, which is helping shift the broader industry mindset. We’re also participating in initiatives like Catena-X, which helps standardize the sharing of ESG metrics. That kind of consistency enables more meaningful collaboration across the value chain. Ultimately, Scope 3 is where the real transformation happens — and it’s also where the greatest opportunity lies. By working together across the value chain, we can drive measurable, lasting impact. Q: You’ve spoken about the importance of embedding sustainability early in product development. How does that shift impact timelines, cost, and engineering culture? A: This is a topic close to my heart. I’ve spent the last three years focused on embedding sustainability into product development, and it really does all start here. Around 80% of a product’s environmental footprint is determined at the design stage, so we must rethink how we define value, performance, and innovation. Embedding sustainability upfront does add time during the concept phase, but that investment pays off by reducing rework and helping avoid costly
Rethinking Thermal Energy in Commercial Buildings

PowerPanel, headquartered in Oxford, focuses on sustainable energy technology with a particular emphasis on hot water systems and thermal energy capture. The company designs and manufactures modular solar hybrid systems that integrate both photovoltaic and thermal components into a single unit. Its goal is to offer energy solutions that are more efficient, durable, and economically viable for a range of commercial and industrial applications. SBN Detroit interviewed Garth Schultz, founder and president, and Oliver Buechse, who leads strategy and organizational development, about energy planning, misconceptions around renewables, and how Michigan’s engineering legacy could help shape the future of sustainability. Q: What is the impetus behind PowerPanel—what are you looking to achieve? Garth Schultz: Our work is driven by two goals – decarbonization and energy savings. We’ve developed a photovoltaic-thermal (PVT) module that combines solar electric and thermal capture in a single footprint. That means you can generate electricity while also capturing heat for domestic hot water or space heating, achieving a form of double decarbonization. We’ve paired that with a flexible hot water storage system. Water can store energy for long periods – up to 55 hours in some cases – so we’re using it as a thermal battery. The system allows for energy recovery from rooftop solar units or HVAC waste heat and redistributes it through a pump for heating needs. The components are designed for easy installation, using engineered foam and PVC linings. Oliver Buechse: By reimagining the infrastructure, we’ve been able to introduce solutions that are cost-effective, recyclable, and have longer life cycles. We’re focused on creating practical, adaptable tools for commercial facilities. Q: What are some of the most common misconceptions businesses have about adopting renewable energy, and how do these misunderstandings slow progress? Schultz: One major misconception is that renewable energy is always more expensive or only viable with significant incentives. In reality, for domestic hot water systems – especially in commercial settings – the return on investment can be very favorable. The payback period is often short, particularly when combined with existing energy efficiency measures. There’s also the belief that traditional systems are “good enough.” But if you compare life cycles, newer solutions like ours often last twice as long as standard replacements and provide better performance over time. Buechse: Another barrier is the perception that renewable adoption is driven by political pressure rather than economic value. When we talk to property owners or facilities managers, the conversation often shifts quickly once they understand the cost savings and operational advantages. Government incentives help reduce the upfront investment, but the benefits – lower utility bills, resilience, and future-proofing – stand on their own. Q: How has the conversation around energy efficiency evolved within Southeast Michigan businesses over the last decade? Schultz: There’s more awareness now. Internal sustainability mandates are common, even in sectors where they didn’t exist 10 or 15 years ago. Businesses are looking at practical ways to improve efficiency, not just for compliance, but because it aligns with their operational goals. Buechse: We’re also seeing a shift where architects and developers are integrating energy solutions from the start. They want buildings that are good for the environment and good for people. It’s not just about meeting code, it’s about delivering healthier, more sustainable spaces that people feel good about occupying. Q: When it comes to energy planning, how can businesses expand their thinking beyond electricity? What parts of the energy equation are often overlooked? Schultz: Thermal energy is often underappreciated. If you look at the average building, around 85% of total energy use goes to heating, cooling, and hot water, not electricity. But we rarely evaluate that side of the equation as thoroughly. Buechse: There’s also a broader awareness now that utility bills don’t reflect the full cost of energy. Natural disasters, insurance premiums, environmental degradation – those costs are externalized. More people are recognizing that energy efficiency also means resilience and reduced long-term risk. Technologies like geothermal or air-source heat pumps are also gaining traction. The big shift we are working toward is using energy that’s already present in the environment – or being wasted – and recapturing it. Q: In a state like Michigan, what makes energy strategy particularly challenging or unique? Schultz: Michigan has a heating-dominant climate. That creates challenges, but it also opens opportunities. In summer, a PVT (photovoltaic) unit produces both peak solar electricity and peak thermal output. That surplus energy can be stored and used later to replenish geothermal systems or supplement heating needs during the cold months. It’s about layering different technologies together—solar, thermal storage, geothermal—to create a more flexible and reliable energy strategy. Q: What trends are you seeing among commercial and industrial businesses rethinking sustainability and energy use? Buechse: It goes back to integration. For example, hospitals need to cool their operating rooms, and they also need hot water for sterilization. If these things happen on completely different systems it’s inefficient and costly. But if you can tie them together, taking energy out of the operating room and using that same energy to heat another area or make hot water you become much more efficient. We’ve worked with breweries where waste heat from tank cleaning is now being reused within the process. That reduces overall energy demand and cuts operating costs. The best part? Many of these upgrades can be implemented as retrofits. They don’t require a complete rebuild, and they create local jobs in plumbing, HVAC, and construction. Q: What role can Michigan businesses play in shaping national or global conversations around sustainable energy? Schultz: Michigan’s manufacturing legacy is a huge asset. The expertise in design, tooling, and production, especially from the auto industry, gives us a unique advantage when it comes to developing and scaling new technologies. Buechse: There’s also a mindset here around solving problems and making things work. We don’t need to compete head-to-head with global solar manufacturers on commodity products. Instead, we can offer solutions with additional value—like thermal capture and storage—and use that to differentiate ourselves. The
Designing for the Future: How HED Approaches Sustainable, Integrated Design Delivery
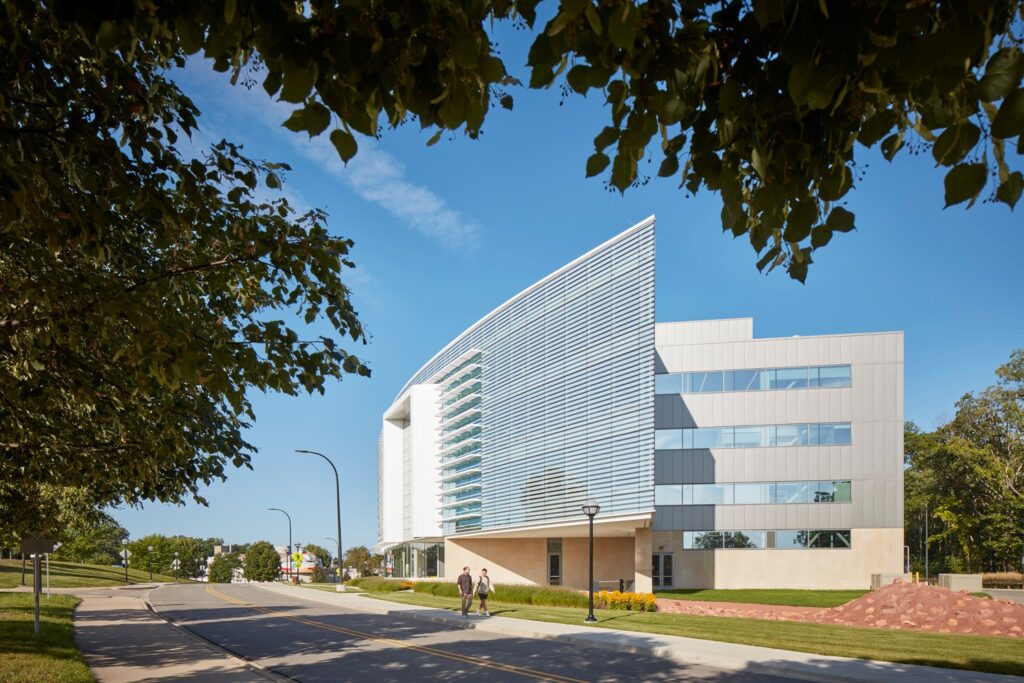
HED is an integrated design, architecture, and engineering company founded in Detroit with a Royal Oak office and a national presence, dedicated to designing high-performing, sustainable spaces that enhance lives and strengthen communities. The firm collaborates with both public and private clients to address the complex challenges of decarbonization and climate resilience. SBN Detroit interviewed Daniel Jaconetti, National Sustainable Design Leader, and Thomas Hoff, Mechanical Engineering and Sustainable Design Leader, to explore the realities of achieving net zero, what clients are prioritizing in Southeast Michigan, and where sustainability efforts must go next. Q: As we approach 2030, how realistic is the industry-wide goal of achieving net-zero operational and embodied carbon in buildings, and where are the biggest gaps today? Jaconetti: Whether or not it’s “realistic” is beside the point; the goal is what is necessary. Scientists have defined what the atmosphere can tolerate, and we’re working backwards from there. The American Institute of Architects (AIA) has set a target of net zero energy (operational greenhouse gas emissions or “carbon”) by 2030 and net zero embodied carbon by 2050. That first part — net zero energy — is readily achievable for many, if not all. However, 2030 is less than five years away, and even if we think we may fall short, we can’t take our foot off the accelerator. One of the biggest gaps right now is energy modeling. We have the tools, but too often, energy modeling is done late in the design process. If we model earlier, we can make smarter decisions upfront, decisions that shape a building’s performance for decades. Q: What trends or client demands are driving sustainability in architecture and engineering, especially in Michigan? Hoff: The most immediate driver is cost. More efficient buildings are simply cheaper to operate and easier to manage, especially when extreme weather hits. Energy efficiency and resilience go hand in hand, and that’s an easy sell. We’re also seeing more clients who want to lead by example. They’re not just aiming for code minimum; they have their own climate goals and want to build high-performance environments that align with their values. Those are fantastic clients to work with because they’re already motivated and looking to push the envelope. Q: What are the most common challenges you face when trying to decarbonize a project? Jaconetti: The biggest challenge is often understanding. There are still knowledge gaps in what “decarbonization” actually means. Sometimes clients — even large manufacturers — are under pressure from global partners to “decarbonize” but don’t know what that entails. So, we start by educating and aligning on definitions. Another issue is that the term “net zero” itself has been made confusing, sometimes defined as just being better than a baseline. That muddies the water. Let’s be honest and consistent about what we’re doing and why. This isn’t a branding exercise. It’s an existential issue for humanity. Q: How do you communicate the long-term value or ROI of sustainable design to clients focused on short-term costs? Hoff: Energy modeling is key. We can take a theoretical building and compare design options, showing exactly how much money (and energy / GHG emissions) a client might save over 5 or 10 years. It’s about shifting the conversation from low first cost to lifecycle cost (or total cost of ownership). When we model early in the design process, we can shape the building to hit more favorable payback windows and improve ROI. In most cases, you spend a little more up front and gain a lot more over the long haul. Q: Can you share a recent Michigan project that exemplifies sustainability, and what made it successful? Hoff: One great example is the renovation and addition of the Alexander G. Ruthven Building at the University of Michigan. The original building was an old museum — architecturally iconic, but outdated and inefficient. We helped transform it into a modern administrative and classroom facility, incorporating chilled beams, a VAV hot water system, and high-performance design throughout. It’s now LEED BD+C NC V4 Gold certified. Even more important: we took a forward-thinking approach to the campus’s future. Although we needed to connect to U-M’s central steam plant in the near term, we designed the systems to be able to evolve into a more efficient central hot water system in the future, to align with their long-term sustainability goals. That kind of systemic thinking is what helps make a project truly sustainable. Q: How do public vs. private sector clients approach sustainability, and how does that play out in Southeast Michigan? Jaconetti: In our experience, both sectors are committed, but the way they document and communicate that commitment can differ. Public clients are often more visible and accountable to constituents, so there’s a strong emphasis on modeling, metrics, and transparency. Private clients, especially those with ESG reporting obligations or international affiliations, can be just as rigorous. What varies most is the degree of certification or formal documentation they pursue. Hoff: In the public sector, particularly with projects like laboratories or civic buildings, the long-term horizon is often more accepted. These clients understand that resilient design can mean lower operating costs over decades — and that aligns well with public funding structures. Q: What role does retrofitting existing buildings play in decarbonization, and how does that differ from new construction? Jaconetti: As architects, we love the blank slate of new construction — it allows us to optimize everything. But the most sustainable building is often the one that already exists. About 50% of a building’s embodied carbon is in the structure. If we can reuse that structure, we’ve already made major progress. That said, we must evaluate trade-offs carefully. Upgrading systems to all-electric, for example, might not make sense if the embodied carbon of those new systems outweighs the operational benefits. Every retrofit has different variables, it’s a nuanced equation, and we have to be honest about the priorities and data behind our decisions. Q: What technologies, policies, or behaviors will be most important in accelerating
Guiding Michigan Businesses Toward Smarter Climate Action

Fresh Coast Climate Solutions is a Michigan-based climate consultancy that aims to help organizations across sectors implement sustainable, equitable, and economically viable climate strategies. Founded on deep expertise in greenhouse gas inventories, carbon mitigation, ESG, water stewardship, and circular economy principles, the company provides technical support and strategic guidance to businesses and municipalities navigating the energy transition. Fresh Coast has partnered on projects ranging from municipal benchmarking in Flint to advanced battery development in collaboration with American Battery Solutions. SBN Detroit interviewed Jenny Oorbeck and Josh Brugeman, co-founders of Fresh Coast Climate Solutions, to discuss the company’s current priorities, lessons from its recent projects, and how small and mid-sized businesses can build effective climate strategies in a fast-changing policy and economic landscape. Q: What is the impetus behind Fresh Coast Climate Solutions? Oorbeck: We launched Fresh Coast three years ago with a sense of urgency. The climate crisis felt personal and immediate, and we wanted to take the reins into our own hands. From the beginning, we focused on building a company culture grounded in bold, transformative action. That means not being afraid to push boundaries, not say no to pilot projects, and work only with partners who share our ambition and urgency. Our goal has always been impact at scale, not incrementalism. Brugeman: We’re very deliberate about engaging in projects that move the needle. That includes deploying transformative technologies, piloting new programmatic approaches, and pursuing strategies that can meaningfully shift the trajectory of climate and sustainability efforts. We’re not interested in business-as-usual—we want to help organizations lead. Q: What are the most common climate-related challenges businesses in Southeast Michigan are facing right now? Oorbeck: We’re seeing a consistent challenge among small and mid-sized enterprises. Many are under pressure—from customers, employees, and supply chain partners—to demonstrate meaningful climate action. But they often lack the bandwidth, technical knowledge, or financial resources to respond effectively. New regulations, evolving standards, and growing stakeholder expectations can feel overwhelming. They need help making informed, strategic, decisions that advance both their sustainability and competitiveness. Brugeman: For many of these companies, sustainability is becoming a prerequisite for doing business, especially if they’re part of larger supply chains. Increasingly, their clients are demanding emissions data, decarbonization strategies, and ESG transparency. The risk is real: Suppliers that don’t adapt could lose out on future contracts. That’s why we emphasize not only environmental stewardship, but also economic competitiveness and operational resilience – things like reducing energy costs or preparing for power disruptions and extreme weather events. Q: Once businesses are ready to act, what barriers tend to prevent meaningful progress? Oorbeck: The most common barriers are capacity and resources. In smaller organizations, sustainability is often an added responsibility for someone already juggling multiple roles. Without a dedicated team or financial backing, the work can stall. That’s why our Michigan Climate Wise Business Program—funded by the Erb Family Foundation—focuses specifically on helping these under-resourced companies move forward. We provide access to expert guidance so they can prioritize and implement practical solutions. Brugeman: I’d also highlight two major gaps: technical expertise and access to capital. Many businesses know sustainability is important, but they don’t know where to start. That’s where engaging external experts can make a difference. We encourage companies to look for “no-regrets” projects—efforts that cut emissions, save money, improve efficiency, and position them for future success. Q: Are there misconceptions you regularly encounter when it comes to emissions, ESG, or water stewardship? Brugeman: One of the biggest misconceptions is around timelines. Many leaders focus solely on short-term paybacks, but climate action is a long game. Sustainability isn’t just a “nice to have”—in larger organizations, it’s already embedded into operations, tied to financial incentives, and closely monitored at the executive level. Smaller companies don’t always realize how deeply integrated these issues have become, and that disconnect can be costly. Oorbeck: Agreed. Another misconception is that the pressure to act will fade, or that a few small gestures are enough. The reality is that some companies risk being dropped as suppliers if they can’t demonstrate credible sustainability progress. We need to move the conversation beyond quarterly goals and toward long-term impact. This is the defining business challenge of our time. Q: How does Michigan’s regional identity shape the way companies need to approach sustainability? Brugeman: Michigan has a unique responsibility and opportunity. We sit at the center of the largest freshwater system on the planet—yet we undervalue and underprotect this critical resource. Water stewardship should be a defining focus for our region. We also have deep roots in heavy manufacturing, which has been the economic backbone of the state. As the global economy shifts toward decarbonization, Michigan is positioned to lead—but only if we commit to building a cleaner, more sustainable industrial base. We’ve excelled at making things. Now we need to excel at making them responsibly. Q: You’ve worked with municipal governments on decarbonization strategies. What can businesses learn from those efforts? Oorbeck: I started my career in the public sector, and at times cities have led the way in sustainability, especially when support at the state or federal level has wavered. Cities began developing climate action plans more than two decades ago. Businesses can learn from those experiences: how to build internal teams, engage stakeholders, and set meaningful targets. At the same time, municipalities can learn from the agility of the private sector, especially in deploying solutions quickly. Brugeman: One thing the public sector does well is plan for the long term. That mindset is essential for climate action. Conversely, the private sector often moves faster and embraces innovation more readily. If each sector borrows from the other, we can accelerate progress. Q: What recent projects are you especially proud of and what lessons might they offer to other Michigan businesses? Brugeman: One is our Michigan Climate Wise Business Program. In partnership with Centrepolis Accelerator and supported by the Erb Family Foundation, we provide sustainability and climate services to small and mid-sized businesses that lack the internal capacity to
Remora’s Carbon Capture Technology Targets Heavy-Duty Transportation

Founded in 2020 and based in Wixom, Michigan, Remora is developing a carbon capture device designed to attach directly to semi-trucks and locomotives and collect emissions. The captured carbon dioxide is then sold to end-users, creating a potential revenue stream for fleet operators and rail companies while reducing their environmental impact. The company has raised more than $100 million in venture capital. SBN Detroit interviewed Paul Gross, co-founder and CEO of Remora, about the company’s current stage of development, the challenges of scaling climate technology, and what it takes to commercialize clean transportation solutions from Southeast Michigan. Q: You’ve raised more than $100 million in venture funding. Who’s backing Remora, and what does that support enable? A: We’ve raised $117 million to date across several funding rounds. Our latest round was led by Valor Equity Partners – they were one of the first institutional investors in Tesla, so we’re fortunate to have that kind of backing and belief in what we’re building. Other key investors include Lowercarbon Capital and First Round Capital. This kind of support has allowed us to invest in R&D and begin to partner with some of the biggest transportation companies in the world. Q: To that end, Remora has drawn interest from companies like Union Pacific, DHL, and Ryder. What does that level of engagement say about the industry’s readiness to adopt carbon capture technology, and how has it shaped your strategic approach? A: I’ve been amazed at how excited trucking and rail companies are about this technology. That level of interest tells me that the industry wants to act. They’re not just talking about sustainability – they’re ready to deploy solutions that make sense financially and operationally. That’s been the missing link. Our system retrofits onto existing vehicles, and it pays for itself by generating revenue from the captured CO₂. That’s what makes it viable for these companies to adopt at scale. Q: Where are you in terms of deployment and technology development? A: We built our first carbon capture system for semi-trucks a few years ago, and that prototype taught us a lot. Our second-generation system is now running with a truck engine and achieving 90% capture efficiency – which we consider a major milestone. We’ve partnered with fleets like Ryder, Estes, and Werner and are preparing for wider deployment. We’re also designing the system to be as compact and lightweight as possible to meet the operational needs of the industry. The scale of the opportunity is huge – there are about 2 million semi-trucks on the road in the U.S., emitting around 350 million tons of CO₂ per year. On the locomotive side, we’re developing the world’s first carbon capture system for trains and testing it right now in Wixom. We’ll begin field deployment with Union Pacific next year. Q: Remora’s approach stands out because it generates revenue through carbon capture resale. How do you see this model evolving as more companies adopt decarbonization strategies? A: There’s already significant demand for CO₂ in the U.S. – around 75 million tons are used every year, and that demand is growing. Industries like food and beverage, wastewater treatment, and sustainable aviation fuel use it, but not to scale. We’re seeing CO₂ being converted into things like hand sanitizer and laundry detergent. So, we’re capturing a waste stream and turning it into a revenue stream. In addition to selling CO₂, we also plan to sequester it underground using EPA-certified wells. There are federal tax credits supporting this, originally passed under the Obama administration and expanded under both Trump and Biden. So, whether through resale or sequestration, we have strong pathways to scale. Q: What are the biggest barriers to broader deployment? A: The biggest challenge right now is manufacturing at scale. This is the first carbon capture system ever built for a locomotive, and there’s no existing supply chain. We’re building it from the ground up, and we’re doing it mostly here in the U.S. So, the focus now is on industrializing our manufacturing process so that we can produce systems quickly, cost-effectively, and at high quality. That’s essential if we’re going to deploy these systems at the speed the climate crisis demands. Q: What advice do you have for other cleantech startups in Southeast Michigan or beyond? A: One lesson is that it’s important to demonstrate commercial demand early. A lot of engineers and scientists are working on technology solutions in this sector, but you have to make sure you’re solving a real problem that your customer has. We started talking to trucking companies on day one, even before we had a working prototype. Getting feedback early helped us design a system that met their needs, worked within their operations, and made financial sense. That kind of customer co-design has been huge for us. Q: What metrics do you track to measure impact? A: We focus on three key indicators: capture efficiency, product purity, and energy use. Capture efficiency tells us what percentage of CO₂ the system is capturing, as I said, we’re at 90% on our latest truck engine tests. Product purity matters because a lot of our CO₂ is going to sectors that need high-purity gas, like food and beverage. Energy use is the third metric. Carbon capture is inherently energy-intensive, and we’re working constantly to improve our efficiency. If the system draws too much energy, it’s not practical – so that’s a top focus for us. Q: Looking ahead, how do you see Remora’s technology integrating with broader trends in transportation, such as fleet electrification, hydrogen fuel, or grid decarbonization? A: Our technology is best suited for heavy-duty, long-haul vehicles — the sector that’s hardest to decarbonize. Electrifying a locomotive, for example, would require about 750 Tesla batteries. Building overhead electrical lines for freight rail would cost over a trillion dollars. And hydrogen still faces a lot of technical and infrastructure challenges. Within this sector, we can retrofit existing vehicles and make a meaningful dent in emissions while generating a return.
Working to Expand Food Waste Composting in Michigan

Spurt Industries is a Wixom-based composting facility and the only EGLE-registered site in Macomb, Wayne, and Oakland counties producing STA Certified Compost, which is the Seal of Testing Assurance from the U.S. Composting Council. The company focuses on transforming food waste into high-quality compost products, working with a wide range of partners to divert waste from landfills and support healthier soils across Southeast Michigan. Through these efforts they consistently divert 15 million pounds of food waste from landfills annually. SBN Detroit interviewed Bill Whitley Jr., Owner and General Manager, and Adriana Whitley, Sales and Marketing Director, about the company’s origin, how compost is created and classified, and the importance of expanding food waste programs. Q: What inspired the founding of Spurt Industries, and how has the company’s mission evolved since its inception? A: Spurt Industries was founded in 1994, coinciding with Michigan’s yard waste ban, which required that yard waste be composted instead of landfilled. That legislation sparked the emergence of commercial composting operations in the state, including Spurt’s original facility in Grand Rapids. In 2008, a previous owner had opened a site in Wixom. We acquired the business in 2016 and have been operating fully out of that location. In Marc, we took over the SOCRRA Composting Yard in Rochester Hills, giving us two locations with roughly equal volume. This will allow us to process approximately 200,000 cubic yards of organics annually, making Spurt one of the largest composters in Michigan. Q: What does it mean to be an EGLE-registered composting facility? A: The previous process to become registered was as simple as submitting a one-page form and fee, but the state passed new solid waste laws about two years ago with new regulations. Now, the requirements are much more robust and we’re fully supportive of that shift. To operate a commercial composting site, facilities must now obtain a general permit and develop detailed documentation, including operational, fire safety and training plans, and more. We also post a $20,000 bond with the state. These measures ensure that composting is done responsibly and consistently across operators. We were involved in lobbying for these changes because we want a level playing field where materials are managed safely and sustainably. Q: What is the significance of being the only facility in Macomb, Wayne, and Oakland counties producing STA Certified Compost? A: The STA Certification is administered by the U.S. Composting Council and is one of the most rigorous compost quality programs in the country. Only four facilities in Michigan currently hold this certification, and we’re proud to be one of them. The certification process includes documenting all input materials, monitoring every compost pile weekly for temperature, moisture, and density, and conducting rigorous lab testing on finished compost. That includes testing for nutrients, metals, and pathogens, and running plant growth trials. This high standard has enabled us to sell compost to certified organic farms – and most importantly, we produce a clean product, free of plastic, glass, or metal contamination. That’s core to our mission. Q: What distinguishes different grades of compost, and how are they managed? A: Several factors influence compost quality: Feedstock: The materials used to make the compost matter. Incorporating food waste alongside yard waste increases nutrient value and mimics natural decomposition processes. Contamination and Pathogen Control: Compost must be free of contaminants and turned regularly to kill pathogens. Otherwise, it won’t meet quality standards. Chemical Maturity: Compost must be fully matured. “Hot compost” that hasn’t cured properly won’t support plant growth. Screening Method: Screen the product to remove oversized or undecomposed material. The finer the screening, the more refined the compost. Beyond quality, we’re also mission-driven to expand food waste composting. Yard waste is mandated by law, but food waste is not – and yet, Michigan sends 1.5 to 2 million tons of food waste to landfills annually. That’s a missed opportunity for soil and water quality improvement. When we apply compost to soil, it increases water absorption by about 100 gallons per cubic yard. That means less runoff, less strain on sewer systems, and fewer sewage overflows into our lakes, which is critical for protecting Michigan’s economy and tourism industry. Q: What has been the reaction from local businesses? Have you seen more interest in food waste recycling of late? A: Absolutely. While COVID-19 significantly disrupted commercial food waste collection – dropping volume by over 90% – we’ve since seen a steady rebound. We now see meaningful enthusiasm from businesses and strong policy support from the state. Michigan has a goal to cut food waste in half by 2030, and EGLE is developing a statewide roadmap that includes composting as a key strategy. Q: How does composting help mitigate climate change and support the environment? A: There are two major benefits: Methane Reduction: Food waste in landfills produces methane – a potent greenhouse gas. Composting food waste in an aerobic (oxygen-rich) environment prevents this. Carbon Sequestration and Soil Health: Compost improves soil quality and reduces the need for synthetic fertilizers, which often require long-distance transport and carry environmental costs. Applying compost also helps sequester carbon in the soil. It’s a win-win for climate and community. Q: Are there untapped opportunities for food waste diversion and composting in Southeast Michigan? A: Yes. There’s a long list. Only a few communities offer food scrap drop-off programs, and even fewer allow food and yard waste to be co-mingled. Less than 1% of restaurants and schools are currently composting, and yet these sectors produce massive amounts of food waste. We believe every business should be composting. We have found that when restaurants begin composting, they become more aware of their overall food waste and often change behavior, improving efficiency and reducing waste overall. Grocers like Meijer and Walmart have made meaningful progress in composting, but there’s still significant untapped potential for other businesses and municipalities to follow suit. Q: What are the biggest barriers to business adoption? A: Cost is one. The other is what we call the “ick factor.” Businesses
Rethinking Water in a Changing Climate

Ann Arbor, Michigan-based LimnoTech is an environmental science and engineering firm with more than 50 years of experience with water-related issues. The firm works with public agencies, private industry, and nonprofit organizations to provide science-driven solutions to complex water challenges. SBN Detroit interviewed Brendan Cousino, PE, Principal and Senior Civil & Environmental Engineer at LimnoTech, to discuss the region’s most pressing water infrastructure challenges and where he sees the biggest opportunities for improvement. Q: What is the impetus behind LimnoTech? A: LimnoTech was founded by graduate students at the University of Michigan over 50 years ago. At the time, the country was just beginning to grapple with water pollution and how to treat contaminated waterways. This was also the early age of computing, and the founders began using computer-based modeling to better understand and solve environmental problems. Essentially, they were a crack team of water quality modeling experts who turned their research into a business that provides real-world environmental solutions. Q: With increasing climate variability, how do you approach designing water management solutions that are both adaptable and future-proof? A: To be future-proof, everything must be adaptable. We’re facing longer drought periods and increasingly intense rainfall events – sometimes in very short time frames. These extremes are becoming more common, and we’ve seen the consequences play out across Michigan. Our approach is to stay aligned with the latest climate science, evaluate the full range of projected conditions, and design infrastructure that can perform under both extremes. Q: What are some of the most pressing water-related challenges facing Southeast Michigan today, and how do they compare to other regions? A: Southeast Michigan is dealing with aging infrastructure systems that were built for historical conditions – not today’s climate realities. The recent Great Lakes Water Authority pipe break in Southwest Detroit is one example. Urban flooding and stormwater management are key issues, as is legacy pollution from our industrial past, compounded by new threats like microplastics, and PFAS. At the same time, Michigan is unique in its abundance of freshwater, much of it in relatively clean condition. That puts a responsibility on all of us to protect these globally significant resources. Q: Conversely, what are the biggest opportunities in Southeast Michigan for improvement and is there any low-hanging fruit? A: In many ways, we’ve already picked the low-hanging fruit. For example, our region has been ahead of the curve when it comes to combined sewer overflow treatment. Investments made in the ’90s and early 2000s, such as retention basins and treatment systems, have made a real difference in improving water quality in the region. Many of the pollutant sources in our stormwater are more broadly distributed. What’s next is being more strategic to plan infrastructure investment. We’re using better data and technology to monitor conditions. For example, we can now use robotics to inspect pipes so we don’t have to wait for them to fail, and real-time monitoring to inform operations during wet weather. That allows us to make smarter, targeted investments to prepare for changing conditions. Q: What innovative strategies or technologies are emerging to help cities like Detroit handle extreme weather events and stormwater management? A: Big data and real-time system operations are making a huge difference. With improved forecasting, operators can anticipate where rainfall is headed and adjust pump systems and treatment infrastructure in advance. We’re also using high-resolution 2D modeling to understand where water will accumulate during storms. That allows us to plan better and pinpoint risk areas. It’s transforming how we manage and design urban stormwater systems. Q: You worked extensively on the Ralph C. Wilson, Jr. Centennial Park on the Detroit riverfront. What specific water-related challenges did this project address, and how does it serve as a model for future waterfront development? A: The site had a number of infrastructure issues. There was legacy sediment contamination from industrial activity that had to be remediated to support a healthy aquatic ecosystem. The bulkheads along the river also were failing, creating dangerous sinkholes. We replaced those with new shoreline stabilization measures. We also incorporated aquatic habitat restoration into the project. The result is a world-class park that improves the riverfront for people while also addressing serious environmental concerns. It’s a great example of how community projects and infrastructure improvements can work hand in hand. Q: Infrastructure in Detroit is aging and often not designed for today’s environmental pressures. What are the biggest gaps in water infrastructure that need to be addressed, and what solutions exist? A: Much of the infrastructure was designed for storm conditions that were expected to occur once every 10 years. Now we’re seeing those types of storms almost every year, at least in some locations within the region. Our stormwater systems simply weren’t built to handle that level of intensity and frequency. The biggest gap is funding. Many systems are at or beyond their design life, but utilities don’t have the financial resources to replace them quickly. We need to identify failure points, understand what’s most vulnerable, and prioritize investment accordingly. Q: What role do community engagement and education play in developing effective climate resilience projects? A: Community engagement is a core part of most projects we work on. It’s essential that the infrastructure improvements we make actually serve the people who live there. When communities have a voice in the design process, the outcomes are better. Education also is key. Whether it’s installing a rain barrel, planting native species, or simply understanding how the stormwater system works, individual actions can add up. If we can manage even the first half inch of rainfall before it enters the storm system, we reduce the reliance on aging infrastructure. Q: Looking ahead, what do you see as the biggest opportunities for improving climate resilience and sustainable water management in the next decade? A: One major opportunity is the shift we’re seeing from purely regulatory compliance to voluntary corporate action. Many of our corporate clients are taking the initiative to reduce their water impacts. That’s a