Cascade Engineering – Designing Toward Function, Planet, and People
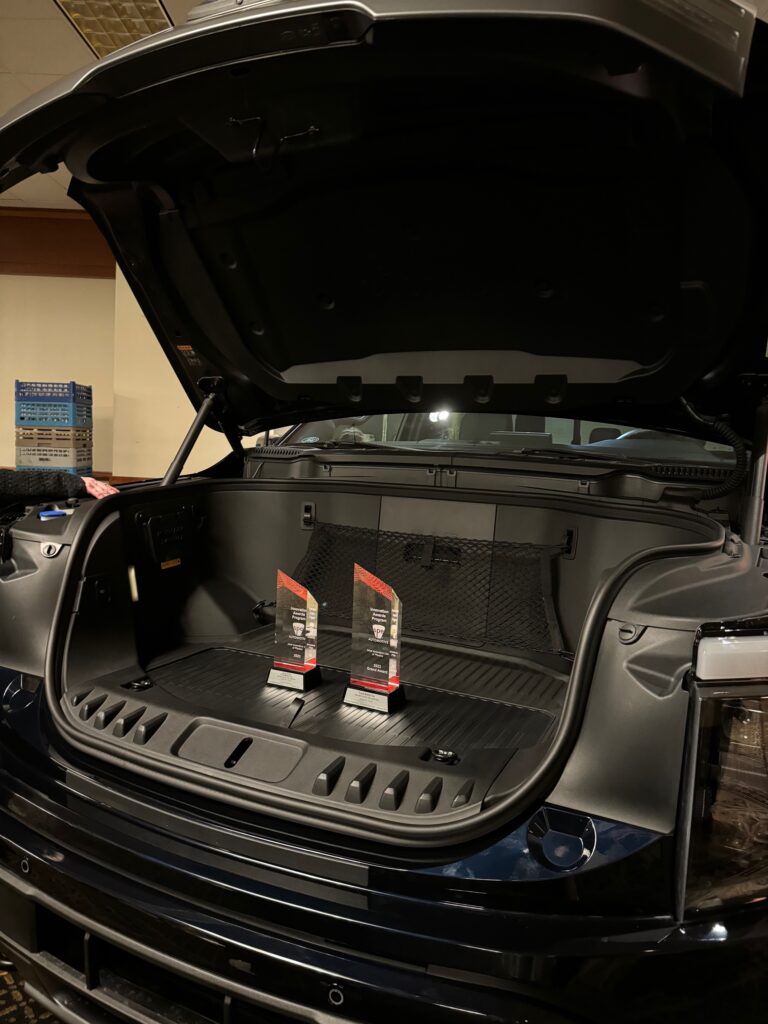
Created in 1973, Cascade Engineering specializes in large-part plastic injection molding. The second-generation, woman-owned company was recognized at the 2023 Society of Plastics Engineers Automotive Innovation Awards for its work with Ford Motor Co. on the Mega Bin/Frunk for the Ford F-150 Lightning. Frunk is a portmanteau word for a trunk on the front of a vehicle. In doing so, it converted the front trunk from a compression-molded painted sheet-molding compound to a large Class A composite injection-molded part and is currently one of the industry’s largest injection-molded product pieces. SBND interviewed Christina Keller, CEO and chair of the Grand Rapids-based Cascade Engineering Family of Cos., about the frunk’s impact on sustainability, creating circular economy solutions, and evolving trends in the industry. Q: How does sustainability stand out within Cascade Engineering? A: Cascade is a second-generation family business that is woman-owned and sustainable. We are celebrating 50 years as a triple-bottom-line company. We are a certified B Corp, ISO 14001 certified and LEED certified. Our focus is on innovative products and solutions in manufacturing and we supply to the furniture, automotive, and waste industries. Q: What role does sustainability play in the company? A: We have been organized as a triple-bottom-line – people, planet, profit – company since our inception. On the people side, we work heavily with returning citizens and also on initiatives to reduce the state of recidivism in Michigan. On the planet side, we’ve been zero waste to landfill since 2012 and have innovated a number of projects in the circular economy. Obviously, we must be profitable to engage in all these activities. Q: Can you tell us more about the frunk? I believe this is currently the industry’s largest injection molded product piece. What aspects of this impact sustainability? A: First, by eliminating the paint process there is a significant reduction of Volatile Organic Compounds (VOCs). Second, it’s more fuel efficient due to decreased product weight. Next, the manufacturing process has been streamlined to reduce energy. And finally, it’s more recyclable in that the end-of-life material can be recycled into a variety of products. Q: How do you think this impacts Southeast Michigan? A: The paint process takes place in Ford facilities, so eliminating this directly reduces VOCs in Southeast Michigan. The collaboration between Cascade and Ford serves as a promising example of potential collaborations between Tier One suppliers and manufacturers in Southeast Michigan. There are many opportunities for partnerships toward a better environmental outcome. Q: In what other ways does the frunk’s design and manufacturing process impact sustainability? A: We have eliminated the environmental burden of paint in the Frunk’s design. Additionally, the secondary routing of holes has been eliminated, reducing process steps and allowing us to produce a higher quantity of parts in less time. The seal interfaces are integrated into the assembly station for further efficiencies, and the material used is recyclable. Q: The Frunk process utilizes a 4,000-ton injection press and a tool equipped with a 16-drop hot runner system to mold these parts. Is this typical? A: No. The use of a 4,000-ton injection press is unique in the industry. The capital required to purchase this equipment poses a significant barrier for most companies. Additionally, the specialized human capital needed to operate such a large press is rare. Q: Is the new frunk product in production? A: Yes. If you buy a Ford 150 Lightning today you will get one of these pieces in your vehicle. It is fully in production and we are looking at more innovations currently. Q: What new innovations are you working on? A: Additional frunks in the near term. Before electric vehicles, we did not have the space in the front of vehicles to create a front trunk. Now, with increased demand for EVs, it’s a growing area and we are looking at manufacturing a number of additional front trunks. Q: Does being in Michigan in particular post challenges or opportunities in terms of your work on the sustainability front? A: There is an excellent network of manufacturers in Michigan – especially Southeast Michigan – that allows us to be truly innovative. A challenge is finding talent. This sector overall currently has 516,000 job openings and over the next decade is projected to reach 3.8 million. Another challenge we face is incarceration. The U.S. has one of the highest incarceration rates, with 1 in 100 adults in jail. We see returning citizens as a valuable pool of talent that can be trained and integrated into the workforce. This presents a unique opportunity for Michigan, as the state is not attracting enough new residents, and only 50% of college graduates stay here. Additionally, while college graduates remain in their first job for an average of two years, returning citizens tend to stay for seven years. This approach offers an interesting solution to addressing the talent gap in Michigan. Q: How do you see industry trends evolving? A: I see a lot of work in the AI space and Industry 4.0 focused on innovative manufacturing methods. There is a noticeable trend towards reshoring, driven by the constraints observed in the global supply chain during the pandemic. Companies are now striving to establish a local footprint, which also helps reduce the carbon footprint from transportation. Additionally, significant efforts are being made to maximize package density for more efficient shipping and transportation. Regarding talent attraction and retention, we have more 65-year-olds in the U.S. than ever before, while our younger demographic is declining. Q: How is Cascade adapting to the changes in the industry? A: We are constantly scanning the horizon to look at trends. On the sustainability side, we are developing an ecosystem of recycled plastic sources to enhance our clean stream of recyclable materials. We are looking at streams from medical waste that could be used, and post-consumer and post-industrial applications. We are also working on additives to use in our products such as hemp fibers, dust waste, and trash materials. And finally, we are working with
Rockford Construction – Focusing on the Full Life Cycle of Spaces
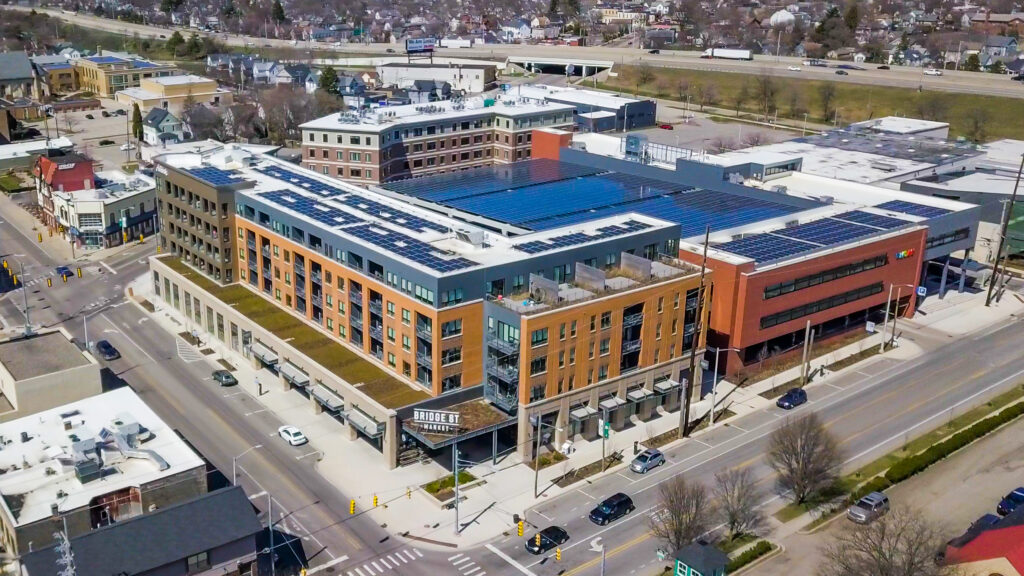
From real estate development to construction and property management, Rockford Construction has been serving the commercial, multiunit, educational, industrial, healthcare, and retail markets throughout the Midwest for more than 30 years. How do they approach sustainability? Mike VanGessel, founder and CEO of Rockford Construction, shares that and more with SBN Detroit. Q: Please tell us about the sustainability practice you have in place. A: Rockford’s current sustainability efforts reflect a “triple bottom line” that is focused on people, the planet, and profit. We consider ourselves to be good stewards of all three of these finite resources. This is certainly a broader view than many people take, but one that is important to our clients and our communities. And we’re not just a construction company. We also develop, own, and manage properties, so our focus extends across the full life cycle of space – not just the initial resources during construction, but the total cost of ownership and the impact our buildings make into the future. As a result, our efforts are quite broad. But each building type brings its own set of challenges and opportunities, allowing us to customize our approach and maximize value to our clients. Q: When did your focus on sustainability come about? A: Decades ago. Rockford was an early adopter of sustainable construction practices. We knew that buildings were a major driver of energy consumption at that time. As a company committed to delivering value to our clients, we recognized that achieving greater energy efficiency would also decrease long-term costs. As the sustainability movement evolved and our knowledge of healthy buildings has grown, our efforts have expanded to include things like water conservation, low VOC (volatile organic compounds)-emitting materials, locally sourced and rapidly renewable materials, and more. Our more-recent triple bottom line approach recognizes that “people” and “profit” are also finite resources, as we’ve seen in our current economy. The shortage of workers – not just in construction but in most industries – has driven a focus on a construction process and end-user facilities that are highly efficient, productive, and attractive to people. The reduction of waste in time and money allows those resources to be deployed elsewhere. Q: What are some examples? A: Over the years, Rockford has completed hundreds of projects that are LEED certified or designed to meet certification requirements. But our approach is applied to all our projects, exploring the building design, systems, and materials to determine the right solution based on client needs, first costs, and long-term operational expenses. The most successful projects result from early involvement and clear goal-setting. One of the best examples can be found in Circuit West, a cutting-edge energy district that encompasses a 13-block area in Grand Rapids. As Rockford was developing and constructing buildings in the area, we partnered with Consumers Energy in their effort to pilot next-generation energy technology. Together, we installed 1,800 solar panels and battery storage capable of producing 500 kilowatts every hour. Power lines were buried, and solar arrays were installed in conjunction with other construction work, greatly reducing installation costs. The result is more reliable, renewable energy for the neighborhood. While Circuit West was a large-scale effort, early involvement allows us to explore all possibilities, uncovering those that make the greatest impact on our clients’ triple bottom Line. Q: What are the drivers behind these practices? A: The driver of sustainability is simple. We are creating healthier, more energy-efficient, and cost-effective buildings for our clients and the people who will live, work, play, and heal inside of them. In the early days, sustainable design and materials were thought to drive additional costs to buildings, and owners had to be deeply committed. Today, a better understanding of good design, appropriate systems, and more readily available sustainable and renewable materials are all driving cost savings. Why a client chooses sustainable solutions – cost savings, environmental responsibility, or healthy spaces – isn’t important. What matters is that the result helps us conserve resources and positively impact our world. Q: Rockford services so many different industries and types of construction – how do your sustainability practices differ between projects? A: Each project is unique, and clients have different goals and expectations. That said, best practices can vary based on different project types. For example, some industrial buildings are high users of energy and, at times, water. Energy-efficient systems, water conservation, and grey water options can provide good solutions. In healthcare facilities, research shows that healing environments include natural light, views, good ventilation, low VOC products, and easily cleaned materials. By focusing on what makes each building unique, the low-hanging fruit of sustainability becomes clear. Often, the most sustainable building is the one that is renovated, either for its existing use or for a new one. This is particularly true in an urban setting, where many building exteriors were built to last for decades. By reusing the walls and structure, not only are tons of waste materials diverted from landfills, but owners can capture the value of materials already in place. Warehouses can be converted into apartment buildings, churches become office buildings and schools are reimagined into senior living. Over the years, Rockford has developed expertise in the adaptive reuse of space. Q: Do you have a team of people set up to implement your sustainability practices? A: In the past, the Rockford team included a director of sustainability. However, we wanted to turn what could be described as a “program” into a “practice.” Our construction team and our property and facility managers are all well-versed in sustainable practices. But we have a variety of team members, from accountants to graphic designers, who want to be a part of our company-wide efforts. That’s why we are launching a company-wide Sustainability Committee to continue to expand our impact both internally and externally. Q: Beyond vendors and material choices – what else do you look at? A: Locally sourced talent, vendors, and materials are part of a strategy that is appealing to our clients, who strive to support