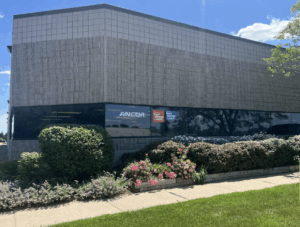
- Kim Kisner
- Education
- 01/03/2023
MSU’s Muhammad Rabnawaz is Focused on Michigan Packaging Industry Solutions
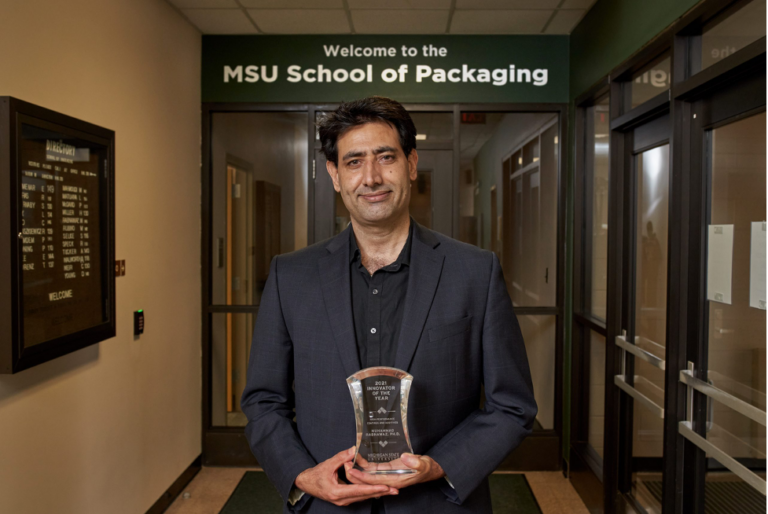
According to information from the University Research Corridor – Michigan State University, University of Michigan, and Wayne State University – each year an estimated 11,000 tons of plastic pollution enters the Great Lakes, harming fish and wildlife and getting into our food and drinking water.
“The United States currently recycles only 5 percent of its plastic waste, and 30 percent of plastic ends up in products that can’t be recycled at all,” said Muhammad Rabnawaz, an assistant professor at Michigan State University’s School of Packaging.
Since August 2016, Rabnawaz’s work in the lab includes creating a new generation of highly skilled workforce, reducing plastic waste from the packaging industry, and creating end-of-life solutions for waste plastics.
Rabnawaz and his team of students are working closely with Michigan packaging and manufacturing companies to achieve innovation around these efforts.
SBN Detroit spoke to Rabnawaz about this work and its potential impact on Southeast Michigan residents, businesses, the community, and the planet.
Q: Can you expand on the work you are doing to reduce plastic packaging waste?
A: Our mission is to find solutions to minimize the element of waste coming from packaging. My top priority is to reduce the environmental impact originating from the packaging sector.
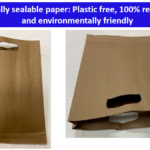
Our work focuses on several aspects related to this.
First, we are looking at how we can divert plastic waste from landfills and move it back into manufacturing. Recycled plastic typically has low performance compared to virgin plastic, so we are creating methods and protocols that help build back the properties of the material to try to achieve virgin-like performance.
Second, we are designing for simplification and driving the idea of looking at the end of life of the packaging in the beginning – when we create it. Much of the plastic used in packaging is multilayered with different types of plastic making up each of several layers. This makes it much more difficult to recycle. We are working on ways to simplify this and forward the use of single-layered plastics or those with fewer layers.
The third is paper-based alternatives. Plastic has unique properties, yet some alternatives are paper-based that do not create microplastics and hence are much better for the environment from this aspect.
So, we are working on research and creating the technologies for the implementation of real-world applications, while at the same time educating students to take the lead in sustainability and packaging innovation in the coming years.
Q: The National Science Foundation awarded you a 2021 CAREER grant to research how to best simplify plastics recycling by developing affordable polymers that are easy to recycle. What are you learning through this research?
A: A common type of plastic is a thermosetting polymer, often called a thermoset. Think of the handle of a pressure cooker or cookware. When you heat it, it does not melt. Thermosets make up 20% of the plastic market. The problem is if we cannot melt it, it cannot be recycled and used for something else.
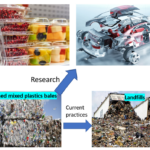
So, we are working on creating a vitrimer (plastic) that behaves like a thermoset and is heat resistant, but above a certain temperature it can be melted, so it can be recycled like thermoplastics (plastics that can be melted).
Q: What is your involvement with Michigan packaging companies?
A: We work closely with several local companies that make plastics, companies that convert plastics to packaging, and companies that work on the recycling of plastics. So, the full supply chain
Q: When do you believe your work will be commercially viable?
A: We are certainly working toward commercializing the technologies we are developing with Southeast Michigan businesses in the interest of helping our community and our planet.
One example is a product that can be used as an alternative to a single-use plastic bag, which we are testing now and anticipate it being commercialized in up to one year.
I anticipate the technology I spoke about regarding simple structure versus multilayered to be in practice within 18-24 months.
It’s time-consuming. We have to look at performance as well as consumer safety and that takes time.
Q: What does this research potentially mean to Michigan manufacturers and businesses, and how does this tie into the manufacturing industry here?
A: Some global packaging giants run their research and development in Michigan. They are looking at materials that can improve the performance of recycled materials. According to the U.S. Plastic Pact, by 2025 if a company is creating a package it has to consist of 30% recycled material or 30% biobased material.
The collection of 30% is not easy.
Packaging companies are going to need help to meet the requirements of this pact and other regulations coming in. We are working toward that and working toward educating the next generation to assist.
Q: To that end, what kinds of skills will the students you are working with have upon entering the workforce, and might this impact Michigan businesses?
A: We are generating a workforce equipped with design and development knowledge for sustainable materials and packaging. They will have the training and expertise to deliver alternatives to protect our environment.
The research we are conducting is focused on solving real-world problems, and the students are connected to stakeholders and local companies to do so.
For example, two of my graduate students have internships they are starting in January where they’ll have opportunities to put their skills and knowledge to work, as well as bring back learnings that will then positively impact our research.
Q: What drives your passion here?
A: Developing the technologies to reduce plastic pollution coming from packaging to benefit society and make the environment better – and training students at the same time – that’s an amazing thing.
Q: What does the future of packaging look like in Michigan?
A: I think packaging will include more and more recycled materials. In the longer term, I think we’ll see more biodegradable plastics and paper alternatives.
I hope that the work we are doing will distinguish Michigan’s packaging industry as among the best in the world. In the end, finding solutions to minimize the element of waste coming from packaging is vitally important and we need to find ways to solve and fix this.
Be sure to subscribe to our newsletter for regular updates on sustainable business practices in and around Detroit.
Kim Kisner
- All
- Business
- Community
- Education
- Events
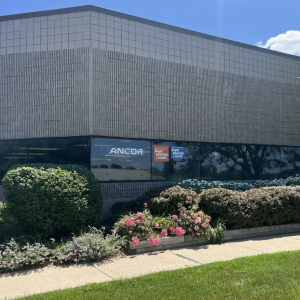
Troy-based Ancor’s roots are in automotive compliance and labeling, but the company has expanded into smart-technology solutions for healthcare, retail, and automotive, including smart battery tracking to stay compliant with local and global regulations. One of its developments is BattCor, a next-generation platform designed to create a real-time “digital twin” of an electric vehicle battery, enabling real-time monitoring, predictive analytics, and improved lifecycle management—from first use through recycling...
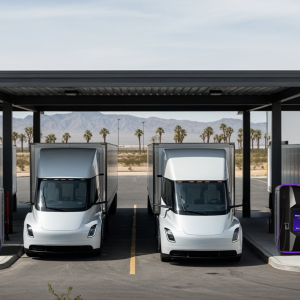
Detroit’s Eastern Market is working to become a national model for integrating freight solutions that reduce fossil fuel use and freight operation costs. San Carlos, Calif.-based ElectricFish, a finalist in the Toyota Mobility Foundation’s Sustainable Cities Challenge, was chosen to build battery-integrated fast chargers to power EVs and provide backup energy for Eastern Market. As one of only three cities worldwide chosen for this challenge, Detroit is using...
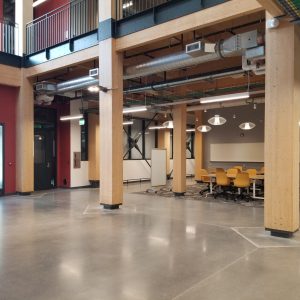
MassTimber@MSU is a cross-disciplinary initiative at Michigan State University dedicated to advancing mass timber construction and manufacturing in Michigan. Collaborating with partners across construction, forestry, development, and state agencies—including the Michigan Department of Natural Resources—the initiative leverages MSU’s land-grant mission through research, teaching, stakeholder engagement, and policy development to build a sustainable mass timber future for the state. SBN Detroit interviewed Sandra Lupien, Director of MassTimber@MSU, about the...