A Look at EGLE’s Materials Waste Management Division
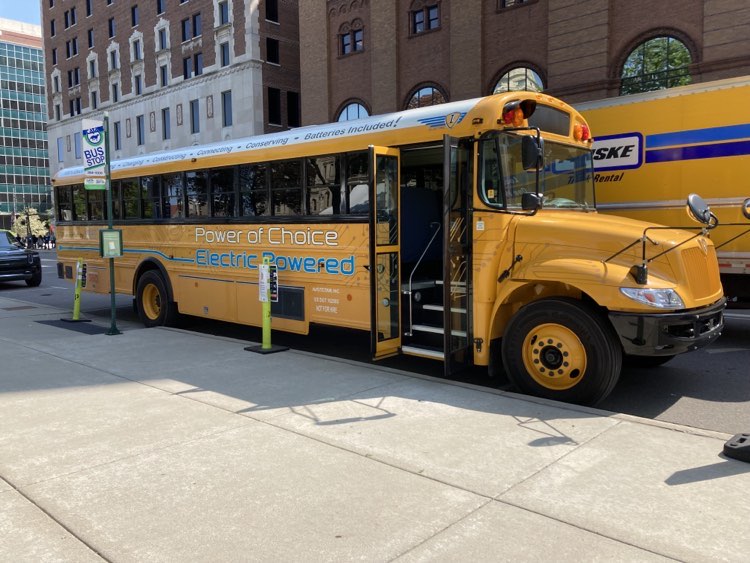
The Materials Management Division (MMD) of the Michigan Department of Environment, Great Lakes, and Energy (EGLE) oversees solid and hazardous waste programs, radioactive materials activities, a radon awareness program, recycling, and energy programs. We interviewed the director of the division, Elizabeth Browne, to get some insights. Q: How do you think energy efficiency, recycling, and pollution prevention are interconnected when it comes to fostering sustainability in Southeast Michigan? A: I have always felt you can’t have any without the others, and they are all key to having a sustainable system. Maybe it’s my biologist background. Recycling facilitates energy efficiency since it translates to diverting items from landfills. If you have a good system, you are reusing and recycling materials nearby, you save energy by not transporting material across state lines. When we look at energy efficiency, it works the same way. If we decrease the effort and resources put into heating, cooling, water usage, and transportation systems by becoming more efficient, we have more resources to allocate elsewhere. And isn’t that the very heart and definition of sustainability? Q: How do environmental justice and underrepresented communities factor into these efforts in Southeast Michigan? A: They factor in highly. There are federal funding requirements to help regulate this. The federal Justice 40 program deems that 40% of grant funds be used in underrepresented communities. Even before that, this was a focus for us. If you look at any of our requests for proposals, we pay special attention to projects coming from underrepresented communities – places where the community’s ability to be more sustainable has been stressed. We are always trying to level the playing field. Q: You work with state and federal partners, entrepreneurs, companies, organizations, and communities to reduce Michigan’s reliance on nonrenewable energy. Can you tell us more about this work? A: We work with federal partners in seeking every grant opportunity that we feel we have a nexus with. We work with companies and organizations through the Retired Engineers, Scientists, Technicians, Administrators, Researchers, and Teachers (RESTART) program. This is a group of retired professionals who work with entities to identify where they have energy issues or where renewable energy options may be a benefit. We do energy audits for houses of worship, schools, and municipal buildings. In many cases, these buildings are older and not efficient, so we offer ideas on how to improve efficiency and look at renewable options. This helps them save financial resources that they can then allocate elsewhere. We have received grant money through the Charge Up Michigan Program to install fast chargers in communities. Within this program, the cost of charger installation is divided amongst the location owner, the utility provider, and EGLE. This allows us to install more chargers, and it helps the utilities get closer to their energy efficiency goals and benefits the property owner or business. We have worked with communities to replace diesel- and gas-powered vehicles with electric ones, including Willow Run Airport and the City of Detroit. In Detroit, we replaced diesel-powered garbage trucks with EVs. We work heavily with NextCycle and the Centropolis Accelerator program at Lawrence Technological University. These are both programs to support businesses in their early stages. NextCycle is geared toward recycling activities, and the Centropolis Accelerator focuses on clean technology and the circular economy. Q: What are your biggest challenges in materials management? A: The thing that keeps me up at night is navigating grant programs. There is this huge influx of federal money, but there are a lot of checks and balances, and trying to manage the funding appropriately is a challenge. There is a lot of hurry-up-and-wait involved. We have a phenomenal team, and I don’t want to break their backs as they work to move the money out to recipients. Q: What are your highest priorities? A: Moving as much of the funding to those who need it and doing it in a way that is equitable and fair and hits the highest needs. Sometimes we make decisions that aren’t flashy, but the impact they have on that community is significant. A small community getting a few solar panels to help power their community building so the kids have someplace to go after school is a good example. We try to disburse the money in a way that supports as many communities and people as possible. Q: What does the future look like? A: I think it keeps getting brighter. The Michigan Legislature recently passed an eight-bill package that updates solid waste laws and will ensure we have sufficient landfill capacity. We just held our Virtual Michigan Materials Management Conference and had almost 600 people from 11 states represented. Getting EV chargers out across the state and seeing more and more interest in communities in terms of electrification is good progress. There is so much potential for economic growth in the energy and recycling fields. It’s astronomical. This excites me. Every day, I see people and companies that are looking for support and direction on becoming more sustainable. More and more companies understand the need to be sustainable because the public is demanding it, and it’s also for their own good. I encourage everyone to reach out to us. People interested in any EGLE grant programs can go to Michigan.gov\EGLE and search for “grants and financing.” For more information about all things Materials Management Division, our web pages can be found at Michigan.gov/EGLE/about/organization/materials-management. Be sure to subscribe to our newsletter for regular updates on sustainable business practices in and around Detroit.
Valeo – Aiming for Carbon Neutrality by 2050
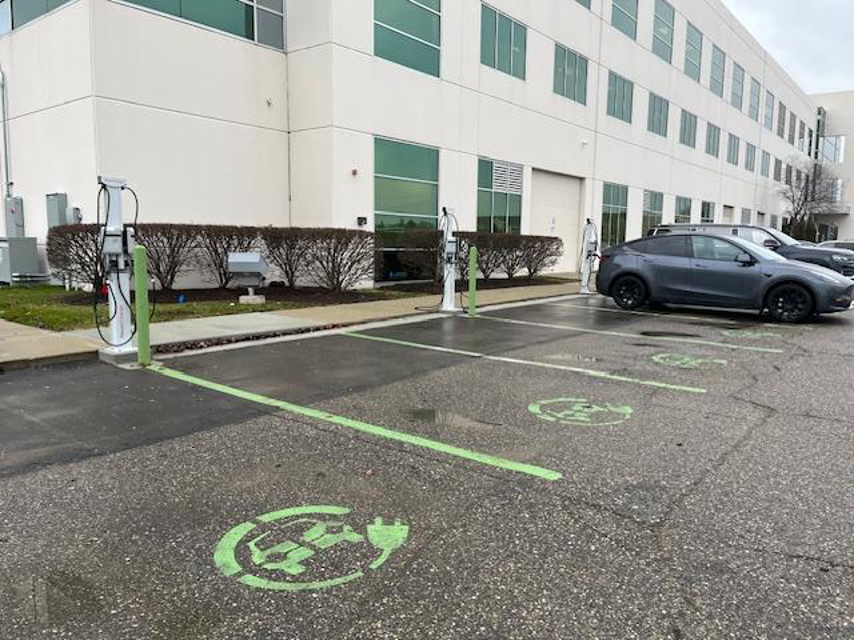
In 2021, global automotive supplier Valeo committed to reaching carbon neutrality by 2050. With $21 billion in sales and 109,900 employees in 29 countries, Valeo has a presence in Troy, Auburn Hills, and Highland Park. SBN Detroit interviewed Valeo Group CAP50 Director Zobeida Gutierrez about the company’s sustainability efforts globally and its impact on Southeast Michigan. Q: Tell us about the CAP50 project. A: Championed by CEO and President Christophe Périllat, Valeo’s global decarbonization plan primarily focuses on 156 production plants. However, our actions extend to our design centers and Valeo Service activities around the world. I have worked for Valeo for thirty years in a variety of positions, including roles in quality in operations, supplier quality, project management, and special projects. I am now the global lead for Valeo’s CAP50 decarbonization plan, and I support other sustainability and circular economy initiatives within North America. Q: What are the specifics of the plan? A: This is our action plan to contribute to carbon neutrality by 2050 across the entire Valeo value chain. Valeo has set 2030 near-term CO2 reduction targets validated by SBTi (Science Based Target initiative) Scope 1 and 2 CO2 emission absolute value reduction of 75% and Scope 3 upstream and downstream reduction of 15% from our 2019 baseline. This goal translates to removing 8.1 million metric tons of greenhouse gas emissions by 2030. Since 2019, we have removed 4.4 million metric tons as of the end of 2022, confirming the effectiveness of our CAP 50 plan. The second reduction target integrates benefits realized from electrification within our product portfolio, accounting for a 45% CO2 emission reduction due to avoided emissions at third parties as compared to the 2019 CO2 emissions footprint baseline. Q: What actions are you taking to achieve this? A: Our framework includes all three scopes as well as greenhouse gas emissions. Scope 1 targets direct emissions coming from our operations. We are currently investing to get our top 100 CO2 emitting sites Energy Management ISO 50001 certified to ensure they are focusing on energy efficiency to drive a 30% reduction in energy consumption by 2030. We are also switching to LED lights, eliminating fuel, oil, and natural gas use, installing solar panels at our sites, and introducing energy-efficient equipment. Scope 2 focuses on indirect greenhouse gas emissions incurred by our energy suppliers. Our low-carbon electricity procurement supports the increase of renewable energy capacity projects. Our internal target is to secure 50% of energy coming from renewable sources by 2025 and 80% by 2030. Valeo has committed to investing $436 million to support Scope 1 and Scope 2 actions. Scope 3 involves indirect greenhouse gas emissions within our supply chain, upstream and downstream. Upstream efforts target indirect emissions incurred by our suppliers, and downstream efforts target indirect emissions incurred by the use and end-of-life of our products. For Scope 3 upstream, we launched a sustainability assessment questionnaire to evaluate our supply chain sustainability maturity level. We also align our suppliers’ greenhouse gas emissions targets with ours – a reduction of 75% for Scope 1 and Scope 2 and 15% for Scope 3 Upstream emissions vs. their baseline year. Our suppliers are also required to cascade these targets throughout their entire supply chain. Our transportation levers within Scope 3 include greener fuels, optimization of filling rates for trucks, multimodal scenarios such as replacing airfreight with train or truck, and the use of returnable and greener packaging. For Scope 3 downstream, Valeo is accelerating its technological roadmap and cementing its global leadership in the electrification market. Currently, 60% of our portfolio supports EVs. We are researching and validating greener materials and designing more energy-efficient, lighter, and greener products. No reduction in greenhouse gas emissions is too small. Every Ton of CO2 reduced counts. Even if it’s simply balancing HVAC systems in our buildings to save energy, simple things can add up to several tons of CO2 emissions reductions. Q: How is your team structured to support the goals and initiatives? A: It starts at the top. Our board of directors has set targets and reviewed achievements related to sustainability and climate change since 2016. In addition, since 2020, a director has been responsible for monitoring corporate social responsibility issues. The Chief Sustainability Officer position within Valeo aligns with the Corporate Vice President of Sustainable Development and External Affairs, who works in partnership with the Chief Technology Officer and Vice President of Strategy. Sustainability topics are therefore under the direct oversight and management of the CEO. Our human resources, health, safety, and environmental, ethics and compliance, research and development, and operations departments (purchasing, quality, projects, industrial) all contribute to Valeo’s sustainable development policy, and each business group assigns CAP 50 champions. Q: What are your biggest challenges? A: Our biggest concern – which is not unique to Valeo – is the lack of renewable energy capacity. The world needs to triple global renewable capacity from 2022 levels by 2030, which must reach 11,000 gigawatts in line with the International Energy Agency’s net zero emissions by 2050 scenario. Also, there is a need for stronger domestic policies and international support, most notably in clean energy investment in emerging and developing economies. Q: What are the biggest opportunities? A: Electrification acceleration. The introduction of electric vehicles is an opportunity, not only for cars but also for micromobility. Another opportunity is preserving our resources by creating a circular economy. Valeo has created the 4R Circle, which is our plan for Robust Design, Remanufacturing, Repair, and Recycling aimed at reducing the use of raw materials and preserving the planet’s resources by giving our products extended life and recyclability options. Q: How is the work you are doing impacting Southeast Michigan? A: In June 2022, we signed a contract with energy supplier DTE Energy to contribute 100% of renewable energy usage at our Michigan locations (Troy, Auburn Hills, and Highland Park) starting in April 2024. This contract is for 20 years, and it demonstrates Valeo’s commitment to supporting renewable energy projects
Daimler Truck’s Detroit Manufacturing Plant – From Diesel to EVs
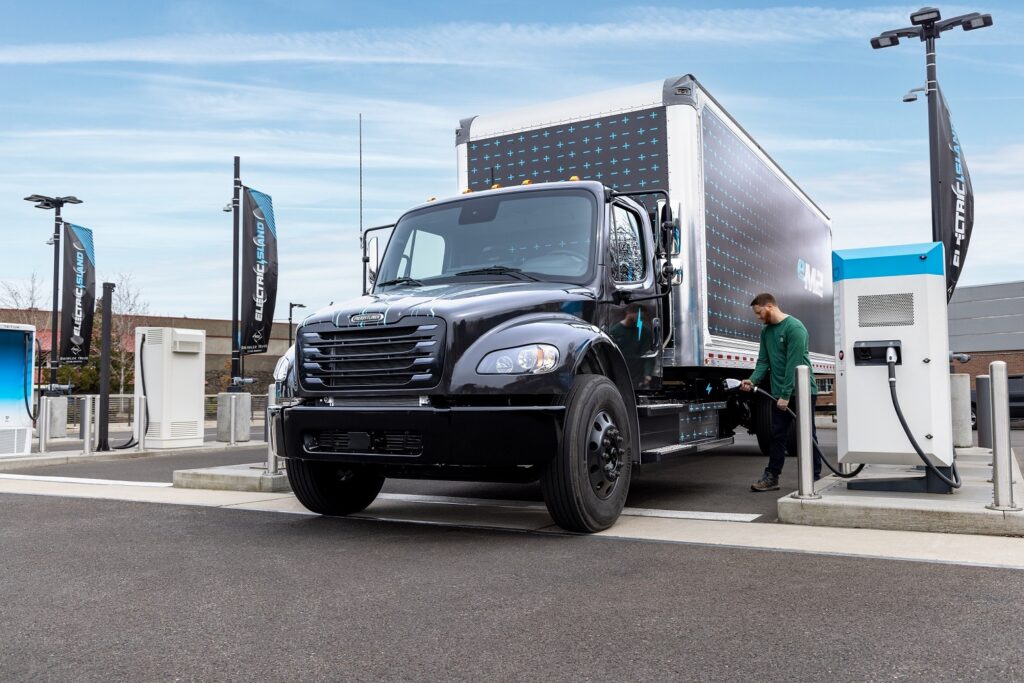
Daimler Truck’s Detroit® Manufacturing Plant produces 400 engines, 250 transmissions, and 1,300 axles daily. The 85-year-old factory is known for making diesel engines but is now working to be a leader in the transition to sustainable transportation. SBN Detroit interviewed Apoorva Mathur, remanufacturing – “reman” – electric product strategy analyst for Daimler Truck North America about the remanufacturing, reuse, and recycling side of the business. Q: How do you approach electrification? A: Our goal is to provide the ePowertrain solution that leads the transition to sustainable transportation. Everything we do pushes toward promoting sustainable transportation. Q: In your role, you focus on the sustainability of Battery Electric Vehicle (BEV) Powertrain components through remanufacturing, reuse, and recycling. How does this work? A: Clearly, part of leading the transition to sustainable transportation is providing an option that has zero emissions, but from an aftermarket perspective, it’s important to be conscious about what we do with components once they come out of the truck. We work to reuse as many components as possible through the remanufacturing process so that we are recycling what we already have. A battery has a lifecycle that extends way beyond what is usable in a vehicle, so to use that battery responsibly it has to have secondary applications. Many times, batteries that come out of a vehicle are used for peak shaving. Peak shaving is utilizing a battery storage system during peak energy usage hours to offset the amount of energy being pulled from the main grid. This reduces the load on the grid. Used batteries can also be used in a microgrid solution whereby some kind of solar or wind-powered system is connected to a battery storage system and energy from solar is used to power the batteries. This is a self-contained situation that does not rely on the grid system at all. Companies can also build used batteries into chargers to provide backup power. So, there are different ways batteries and components can be remanufactured and reused. The recycling component is pretty straightforward. We have a recycling program and a company that disposes of batteries and materials responsibly and also recycles material back into the supply chain. Q: In your role, you also support special projects that advance battery electric vehicle (BEV) adoption, such as creating a charging hub at your Redford location. Can you tell us more about that? A: Yes. The state of Michigan secured $13 million in funding in partnership with Daimler Truck North America and DTE Energy to develop the mobility charging hub earlier this year. We will build a multimodal charging hub there, helping companies to transition their fleets. The charging hub will support heavy trucks and also passenger vehicles and more with the intent to help the entire community transition to EVs. Q: What is driving your change to electrification? A: The largest driver is a combination of emissions standards becoming stricter and also a greater focus on sustainability as a whole on the global stage. Daimler Truck is committed to the Paris Agreement globally, and we are doing our part to provide our customers with zero-emission options. Daimler Truck as a whole is looking for what best suits our customers’ needs, and we are electrifying products across the board and will continue to go down that path. We are also looking at other options such as hydrogen. We need to explore everything to ensure we are giving the best options to our customers. Q: What drives your passion for what you do? A: This is so new for all of us. I’m constantly learning. We are faced with something new every day when comes to requirements from a regulatory perspective and we are constantly getting customer feedback. It’s unchartered territory for all of us and we are all taking this learning journey together in this industry. That’s fun for me. It’s not the business as usual that Detroit Diesel has been doing for 85 years. It’s new and different and exciting. Q: What are the biggest challenges? A: Again, it’s unscripted. It involves so much effort as an industry to make this switch. We can build the product, but we also need the infrastructure. There are gas stations on every corner but supporting EVs is brand new. Also, we need support from utilities. Grid support requires more resiliency as we switch, and there is a lot of work to be done here. When we say we are transforming the transportation industry we mean it. We are taking every component and turning it into something different and it requires so much from everyone. Q: What are the opportunities? A: We’ve seen a whole new level of energy and innovation coming from all sides. New suppliers and players coming into the space every day. It’s exciting to see these companies coming into the industry to push and innovate. On the infrastructure side, it’s the same. New data companies are looking at how to use power in areas to help the grid. There are new charging management systems, new charging suppliers, etc. It’s given the industry a chance to innovate and go outside the norm of what we provide. Q: How do you think the work you are doing impacts Southeast Michigan in terms of innovation? A: Detroit is the place to be when it comes to sustainable transportation. And Detroit is the hub for all things mobility. The Battery Show North America is in Detroit each year, and there is so much knowledge at that show. It’s all being done here. Detroit is the center of competency. It’s a great place to learn and innovate and partner and work within. Q: What does the future look like? A: We will see change on the roads around us. Electric cars are growing in production and adoption in this area. We will see different types of technology being used for different applications as we learn what’s effective. We will see a mixed mobility strategy across the board and that’s exciting. I also
This Month’s Message from Terry Barclay, SBN Detroit chair and CEO of Inforum
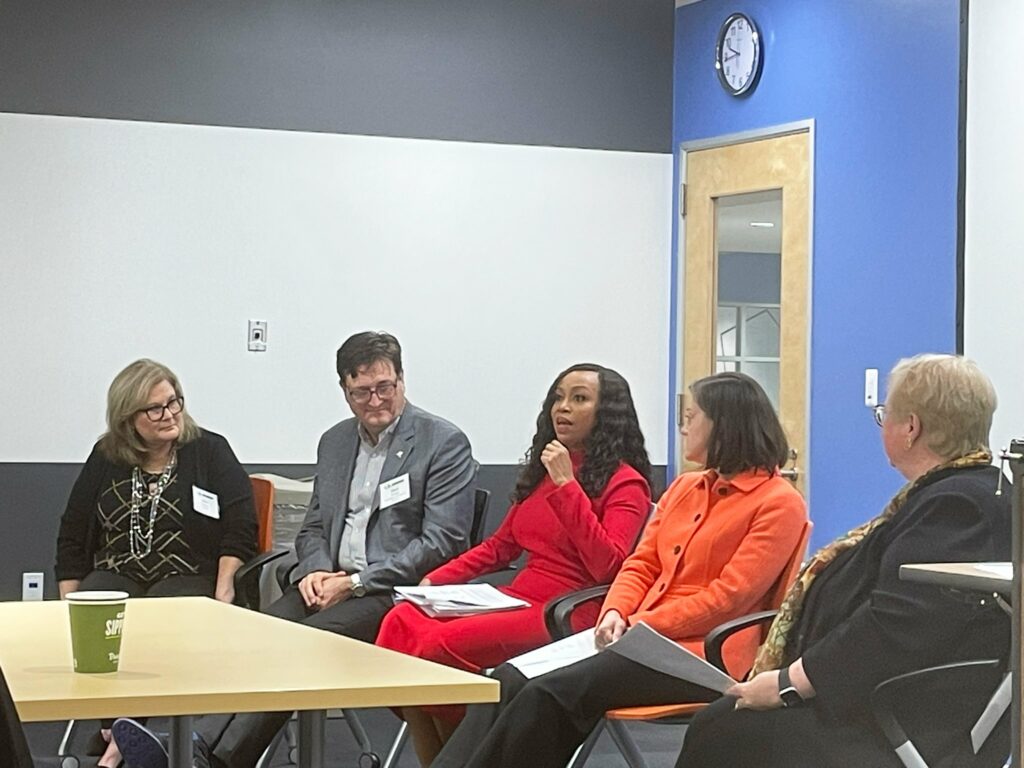
On Oct. 31, SBND hosted a panel focusing on business and sustainability in the Great Lakes region. The event was a collaboration with the Council of the Great Lakes Region and featured Shanelle Jackson, senior manager, LyondellBasell; Edna Lorenz, energy director, Corewell Health; Mark Schrupp, executive director, Detroit/Wayne County Port Authority; and Lillian Woolley, senior chemical engineer, Fishbeck. It was a fascinating discussion, and I encourage you to read the story here. Before the panel discussion, Colin Bird, counsel general of Canada in Detroit, spoke about how Canada and the U.S. work together on issues that include the environment, maritime trade, and stewardship of the Great Lakes. In Michigan, we are more aware of this than most in the U.S., but some of the specifics were new to me. Some examples: In 2022, Canada was the U.S.’s largest trading partner in goods and services. About 80% of Canadian goods exports to the U.S. ‘feed’ American supply chains for final goods. According to U.S. trade data, in 2022, bilateral trade in goods and services was US$914.3 billion, representing over US$2.5 billion worth of goods and services crossing the border every day. The joint stewardship of the environment is a cornerstone of Canada-U.S. relations, from air and water quality to wildlife management. This includes at least 50 federal bilateral arrangements, more than 100 arrangements at the state and provincial level, and the Boundary Waters Treaty of 1909. The Canada-U.S. Joint Action Plan on Critical Minerals Collaboration and the Memorandum of Understanding (MOU) expand energy cooperation between the two countries are some examples of collaborative initiatives. Canada’s 2023 federal budget allocates $650 million over ten years to support monitoring, assessment, and restoration work in key freshwater ecosystems, many of which are shared by Canada and the US. Of this total, $420 million will go towards restoring and protecting the Great Lakes, complementing significant U.S. efforts in this regard. On September 18, the University of Michigan announced an award of $5 million from the National Science Foundation to establish the Global Center for Understanding Climate Change Impacts on Transboundary Waters, comprised of U.S. and Canadian universities and Indigenous representatives. McMaster University will lead the Canadian side, with $3.75 million in funding provided by the National Science Foundation. More trade statistics specific to Michigan can be found here. Be sure to subscribe to our newsletter for regular updates on sustainable business practices in and around Detroit.
‘We’re Building More Than Just a Building Here’
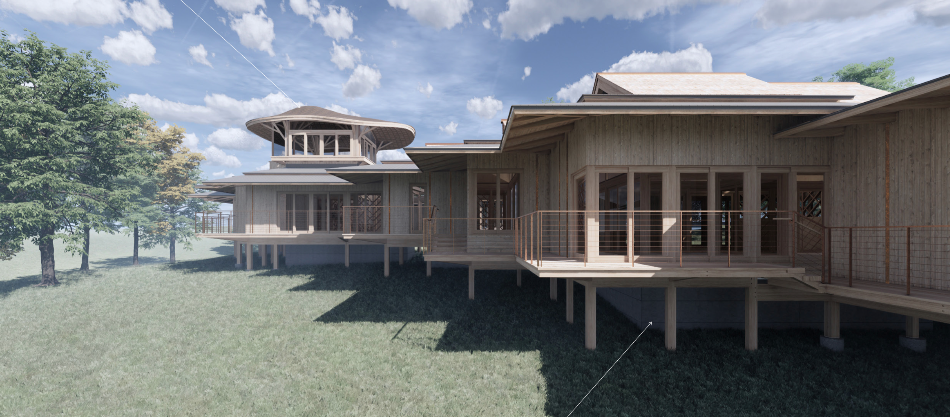
Novi-based Cunningham-Limp is developing what it is planning to be the most sustainable construction project in Michigan. The six-building corporate campus at 35917 West 12 Mile Road in Farmington Hills will serve as the new Detroit Engineering Center for electrical connection maker Japanese Solderless Terminals (JST). All materials for the buildings are naturally sourced, and the construction will feature no drywall, paint, structured steel, catch basins, storm pipes, carpet, or other synthetic products. SBN Detroit interviewed Jake Gardner, Cunningham-Limp project manager for the development, to find out more. Q: How does Cunningham-Limp approach sustainability as a company overall? A: Our mission at Cunningham-Limp is to make a positive impact on people, communities, and companies, and prioritizing environmental sustainability is one of the ways we fulfill that mission, so we work with our clients to implement creative, sustainable solutions wherever we can. Q: How did the JST project come to fruition? A: It first came to us through our president, Samuel J. Ashley Jr., who was immediately intrigued by the opportunity to be a part of something special in a commercial corridor using a completely sustainable methodology that will have a positive impact on the community. His first reaction was disbelief. He couldn’t imagine that something like this would ever be undertaken in our region. However, after introductory meetings and building relationships with the collective organizations participating in the project, we went into the early planning stages. Six years later here we are. Q: What is the impetus behind this project? A: The development is an homage to the forest and Japanese culture and design. The primary concept behind the project is to showcase the idea of harmony between people and the ecosystem, Japanese and American cultures, and the preservation of nature in a built environment. The philosophy is to promote corporate development in a way that is both humane and beneficial for the land it is being built on. The artistic portrayal of the forest in this project is more profound than any existing standards or certifications could reflect. Q: How do you approach a project like this? A: There was more than a decade of strategic planning before construction began. All aspects of the forest were thoroughly researched, and the findings of those studies have guided design and construction. Q: Is it more expensive to construct this way? A: It ultimately depends on what you consider to be an expense – and it’s important to look beyond just the financial aspect. We need to consider the impact our actions have on the environment. Yes, certain things may come with a financial cost, but the true cost of not taking care of our planet is far greater. We’re doing the right thing to make a positive impact on the planet. It’s not always about the money. Q: What are the biggest challenges? A: The unconventional approach to this project brings on many challenges. Some include stormwater management, utility connectivity between adjacent sites, and finding subcontractors who can perform the required construction techniques (building a thatched roof, for example). Also, because of the uniqueness of this project, a lot of the truly sustainable elements go beyond current ordinances and engineering standards, so getting the concepts approved took more effort than a traditional project would. Finally, finding subcontractors with the right mindset that are of commercial scale and size but whose quality of work is that of a high-end residential craftsman style approach is a challenge. Q: How will the building be cooled and heated? A: Geothermal energy is utilized to naturally heat and cool the site, while other supporting elements assist in regulating the temperature of the building. For instance, in the test lab, passive heating and cooling are implemented around the perimeter. This involves an unoccupied air chamber around the primarily underground test lab that helps in keeping the air cool, and skylights throughout the perimeter that aid in warming the air up. These elements reduce the workload on the geothermal energy system. Q: How was the site chosen? A: Our client and project owner, JST, wanted a heavily forested site located in Farmington Hills close to their local partners. They conducted extensive studies of the land, including the prior inhabitants of the site dating back to the Native American Potawatomi Tribe, as well as the identification of every plant and animal species represented on the parcel. Following the research, it was strategically picked because the property is one of the last forested sites in JST’s target demographic, with natural water features and proximity to JST’s current office. Q: Do you think this project will act as a “lead by example” with others looking to pursue more environmentally friendly structures? A: The dream and hope of the entire project team is for this approach to become a trend and be replicated by others moving forward. In fact, we are optimistic that the neighboring 30-acre site will also be used in an environmentally conscious manner. We hope whoever acquires the property will continue honoring the forest and its story. Q: What are some examples of other Cunningham-Limp projects that are focused on sustainability? A: JST is one of the sustainable builds that C-L is most known for, but we have extensive experience in implementing sustainable practices in our projects and working in sustainable markets. In 2005, the State of Michigan made a requirement that any new building had to be LEED-certified, so we built the first LEED-constructed project owned by the State of Michigan, which is occupied by the Department of Environment, Great Lakes, and Energy (EGLE). Additionally, we include adaptive reuse, Energy Star, and required environmental practices as part of our standard project delivery. We are currently working on two electric vehicle battery testing laboratories in Auburn Hills. Another project that’s been recognized for its sustainable construction is the Commongrounds cooperative project in Traverse City. Additionally, we recently received a 2023 Project Achievement award from CAM Magazine for our Orion Township Municipal Complex, which had many environmentally sustainable
Interconnected Set of Greenways and Blueways to Create New Southeast Michigan Trail
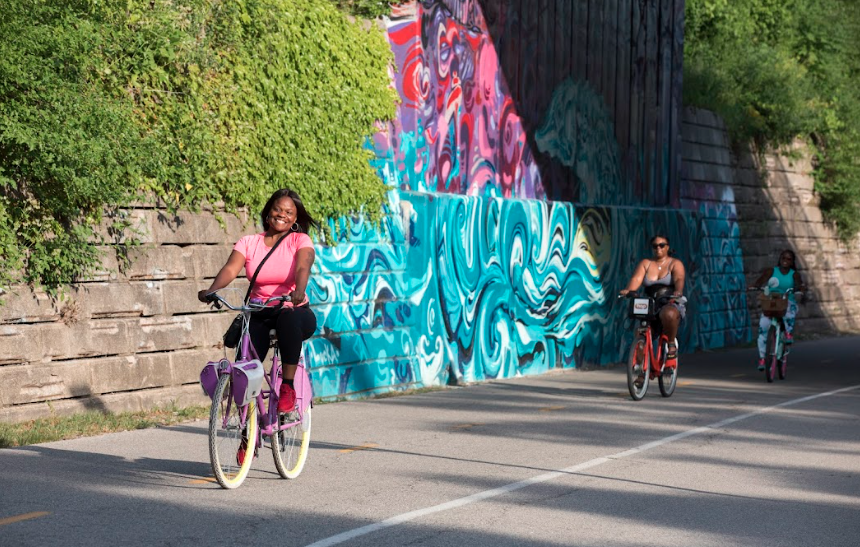
There’s the Appalachian Trail in the East, the Pacific Rim Trail in the West, and the Continental Divide Trail in the Rocky Mountains. Now, Southeast Michigan will have its own regional trail called The Great Lakes Way. Over the past several years, the Community Foundation for Southeast Michigan (CFSEM) has convened a group of organizations, municipalities, and agencies to explore ways to build on the freshwater assets of the Southeast Michigan region. They created the vision for The Great Lakes Way. Once complete, The Great Lakes Way will be an interconnected set of greenways and blueways (water trails) stretching from southern Lake Huron to western Lake Erie, passing through the counties of Monroe, Wayne, Macomb, and St. Clair. The Way incorporates about 160 miles of greenways and 156 miles of blueways along Southeast Michigan’s coastline. SBN Detroit spoke with Greg Yankee, CFSEM director of arts and environment initiatives about the vision, the sustainability aspects, and how Southeast Michigan businesses can get involved. Q: How did The Great Lakes Way get initiated under the Community Foundation for Southeast Michigan? A: We’ve been seeing a great greenway movement happening throughout the region. Communities are making serious investments in fantastic projects but there are gaps between them. It led us to think about how to connect these trails and in general, how to give more people access to trails and greenways and waterways all across the region. So, our mission is to connect people to the outdoors, to each other, and to water in a bigger way. This requires funding and community engagement and the actual work to make it happen, and all of that needs to occur in a certain order. The Community Foundation of Southeast Michigan works across all of these communities and can facilitate the outreach, coordination, and funding so it makes sense for The Great Lakes Way to have this initiative with us. We have a 35-member advisory committee at the heart of The Great Lakes Way project, providing us with information, guidance, and connections to critical resources. Committee members include representatives from the Michigan Department of Natural Resources, the Metroparks, Michigan Trails and Greenways Alliance, the National Park Service, as well as parks and recreation leaders from the communities all along the route. Q: What solutions are you looking to provide with The Great Lakes Way? A: We feel that there is a definite need to provide more opportunities to spend more time outdoors recreating and enjoying our waterways. For me, growing up in Trenton we had Elizabeth Park on the water, but trails were limited and not connected to neighboring communities. There is a huge opportunity to strengthen community connections and make it easy for more people to experience these incredible natural resources all along our waterways. In short, there is no equitable access to water. In a lot of cases, geographical location determines whether you spend time recreating outdoors. But we are working to level the playing field and put these amenities within reach of as many Southeast Michigan communities as possible. Q: What are the goals of The Great Lakes Way from a sustainability perspective? A: Our goal is to help communities develop their public greenspaces while looking through a sustainability lens. Improving public access to water, building trails, and creating green spaces will also help grow our outdoor recreational economy – a win for the environment and the economy. When residents and businesses witness these projects making the environment healthier, getting people outside, connecting people to places, and enhancing economic opportunities, sustainability becomes more a part of our lives. We want to foster a stronger relationship between people and the watersheds they call home. Q: How does the Community Foundation for Southeast Michigan oversee the implementation of these sustainability practices? A: The projects are planned and managed by the individual municipalities, of course, not us. But our team acts as a resource to help communities in the planning stages by connecting them to resources, experts, and service providers so that sustainability is not an afterthought. We seek to help, not interfere. We are mindful of and in communication with each of the municipalities and communities developing these projects. So, if, for example, Clinton Township is putting in a kayak launch and Trenton wants to do the same, we can connect the two communities to learn from each other and share resources. We do a lot of that. We value being an ally and our goal is helping and facilitating, not managing a community’s projects. Q: We hear a lot about greenways but not blueways. What is the vision for blueways? A: Again, although I grew up in Trenton, I did not consider myself to be living on the water. That’s because the area along the water was an industrial corridor and often impossible to access for recreation. We have these remarkable rivers and lakes, but traditionally it’s only been where factories go. We want to help revitalize former industrial spaces where appropriate and open them up for public recreation and enjoyment of the water. Combining greenways and blueways will be a huge victory for everyone. The defining geographic characteristic of Southeast Michigan is our waterways, and to make a shift toward people enjoying them for recreation, nature appreciation, and gathering places is exciting. This is what creating better access to blueways will provide. Q: How can The Great Lakes Way impact the economy in Southeast Michigan? A: We commissioned a study on the economic impact of The Great Lakes Way. The study shows, all told and over time, that the total economic impact of The Great Lakes Way is in the billions of dollars. Q: How will The Great Lakes Way impact businesses in Southeast Michigan? A: The outdoor recreation businesses will be positively impacted, no doubt. Businesses and other points of interest located along the Way will benefit from people who stop for lunch, coffee, shopping, or to check out a historical landmark. We strongly believe that employers now recognize the
Vehya – Working to Help Consumers and Businesses Electrify Faster
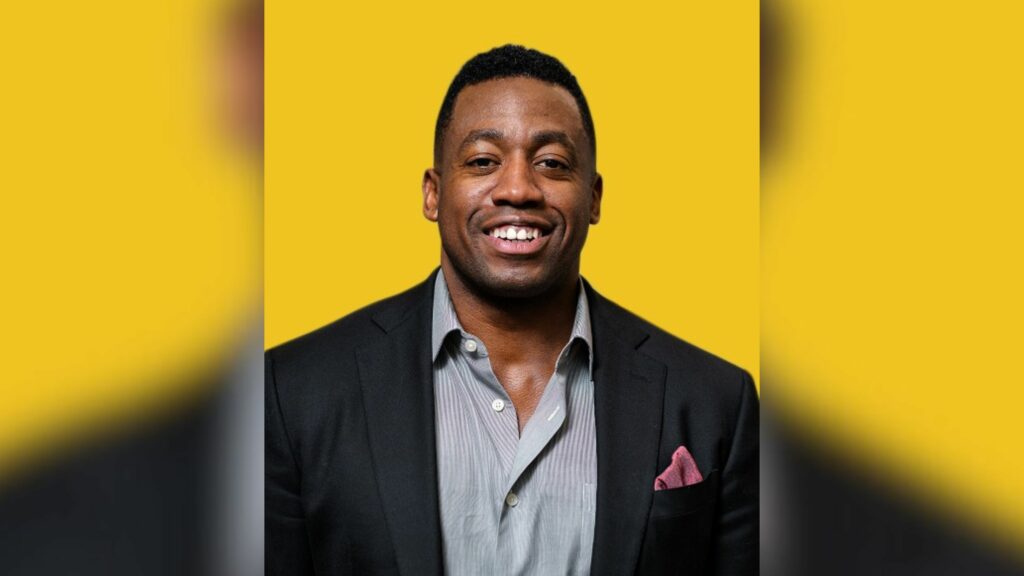
Detroit-based Vehya is a two-year-old marketplace, which offers services to businesses and individuals looking to adopt EV technology. SBN Detroit interviewed founder and CEO William McCoy to find out more. Q: What can you tell us about Vehya? A: Vehya (pronounced and meaning “via”) is a marketplace for electrification. With everyone moving (or trying to move to) electrification quickly for a sustainable future, we know the project management – research, execution, installation, maintenance – portion can be challenging. So, we created a platform that makes that process easy. Before, if a consumer or office wanted to get an easy charger, they would have to find an electrician, vet them, research products to find the best solution, schedule installation, etc. Vehya turns those steps into a turnkey process. We sell electric vehicle chargers, solar, battery storage, and other resiliency products and have a network of certified service providers to install and service them. Q: Are the end users consumers or businesses? A: Both. In the beginning, we focused more on the commercial and quickly realized there was just as much of a need on the consumer side. The people we were working with on commercial projects were asking if we could do this for them at their homes, or for their clients so we created a consumer-facing platform as well. Q: What needs do you believe Vehya solves? A: People and businesses that are looking to transition to electric often do not have the time or resources for the research and logistics involved. So, we fill that gap. Early adopters will jump in and figure it out, but for others – for the mainstream – they need help. We streamline the process to help both consumers and businesses electrify faster. Q: Tell me about your new partnership with DTE. A: DTE was looking to help their customers streamline the process of obtaining electric vehicle chargers both from a financial and logistical standpoint. They launched an RFP and ultimately chose Vehya for this partnership, which we are so happy to participate in. It’s a fantastic program because it opens the door for many more people to make the transition to EV who couldn’t without the financing DTE’s program offers. Further, many homes need service panel upgrades to support EV charging and that is an additional cost, so the financing becomes even more important. Customers can now come onto the platform, buy a charger and have it shipped to their home, identify an electrician to install it, and sign up for financing all in one place. Through this program, we’ve had about 2,500 enter the platform chargers and have facilitated close to 400 installs in the three months since it launched. Q: Tell me about the partnership with Stellantis A: In March, we became a preferred partner for EV charger sales, installation, and maintenance for Stellantis’ U.S. auto dealers. Our program includes Vehya-certified electricians, detailed site surveys, comprehensive estimates, and a dedicated account manager that handles all administrative and project management duties. Q: How is the Vehya marketplace different than other platforms? A: The fact that we offer products, service providers, and project management is different than other platforms. You can buy a charger on a marketplace like Amazon but then you have to figure out the installation. We vet and certify our service providers as well. Q: Tell me about that vetting and certification process. A: Most of our electricians are certified by the Electric Vehicle Infrastructure Training Program (EVITP). We then certify them regarding experience and licensing. They must have the highest levels of insurance. And we do a background check. Q: How do you think the work you do impacts Southeast Michigan businesses? A: A lot of businesses want to electrify their fleets and company cars but don’t know where to start and don’t have the resources to do the research. Workforce development and job creation are also important pieces to us. Vehya is the marketplace that connects consumers and businesses with highly qualified service providers. It connects these service providers to people raising their hands for help in turn creating and bolstering careers. Q: What does the future look like for the company? A: We are working to make our online processes even quicker and to scale our offering. We are also working with underserviced communities to take advantage of EV transition opportunities as well. Financing is key. An average install in the Detroit area is $2,300, because as I had mentioned, a service panel upgrade is typically needed. We are working with banks now to put together consumer packaging to spur adoption and make it easier for more people. Equity and inclusion have to be considered – we need everyone to be a part of this. Be sure to subscribe to our newsletter for regular updates on sustainable business practices in and around Detroit.