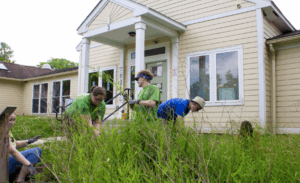
- Kim Kisner
- Business
- 10/31/2023
Cunningham-Limp, Client JST Collaborate on Plan for ‘Most Sustainable Construction Project in Michigan’
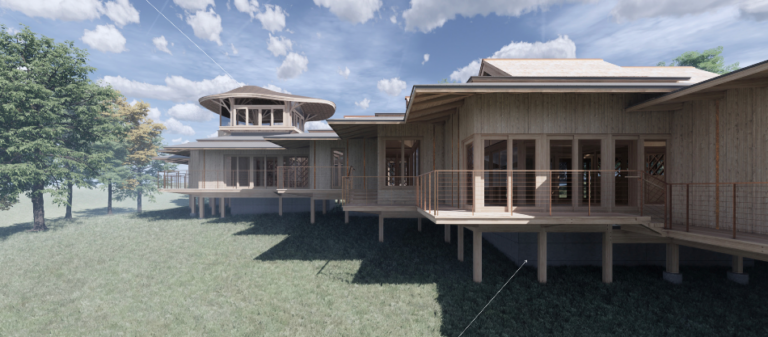
Novi-based Cunningham-Limp is developing what it is planning to be the most sustainable construction project in Michigan.
The six-building corporate campus at 35917 West 12 Mile Road in Farmington Hills will serve as the new Detroit Engineering Center for electrical connection maker Japanese Solderless Terminals (JST). All materials for the buildings are naturally sourced, and the construction will feature no drywall, paint, structured steel, catch basins, storm pipes, carpet, or other synthetic products.
SBN Detroit interviewed Jake Gardner, Cunningham-Limp project manager for the development, to find out more.
Q: How does Cunningham-Limp approach sustainability as a company overall?
A: Our mission at Cunningham-Limp is to make a positive impact on people, communities, and companies, and prioritizing environmental sustainability is one of the ways we fulfill that mission, so we work with our clients to implement creative, sustainable solutions wherever we can.
Q: How did the JST project come to fruition?
A: It first came to us through our president, Samuel J. Ashley Jr., who was immediately intrigued by the opportunity to be a part of something special in a commercial corridor using a completely sustainable methodology that will have a positive impact on the community.
His first reaction was disbelief. He couldn’t imagine that something like this would ever be undertaken in our region. However, after introductory meetings and building relationships with the collective organizations participating in the project, we went into the early planning stages. Six years later here we are.
Q: What is the impetus behind this project?
A: The development is an homage to the forest and Japanese culture and design. The primary concept behind the project is to showcase the idea of harmony between people and the ecosystem, Japanese and American cultures, and the preservation of nature in a built environment.
The philosophy is to promote corporate development in a way that is both humane and beneficial for the land it is being built on. The artistic portrayal of the forest in this project is more profound than any existing standards or certifications could reflect.
Q: How do you approach a project like this?
A: There was more than a decade of strategic planning before construction began. All aspects of the forest were thoroughly researched, and the findings of those studies have guided design and construction.
Q: Is it more expensive to construct this way?
A: It ultimately depends on what you consider to be an expense – and it’s important to look beyond just the financial aspect. We need to consider the impact our actions have on the environment. Yes, certain things may come with a financial cost, but the true cost of not taking care of our planet is far greater. We’re doing the right thing to make a positive impact on the planet. It’s not always about the money.
Q: What are the biggest challenges?
A: The unconventional approach to this project brings on many challenges. Some include stormwater management, utility connectivity between adjacent sites, and finding subcontractors who can perform the required construction techniques (building a thatched roof, for example).
Also, because of the uniqueness of this project, a lot of the truly sustainable elements go beyond current ordinances and engineering standards, so getting the concepts approved took more effort than a traditional project would.
Finally, finding subcontractors with the right mindset that are of commercial scale and size but whose quality of work is that of a high-end residential craftsman style approach is a challenge.
Q: How will the building be cooled and heated?
A: Geothermal energy is utilized to naturally heat and cool the site, while other supporting elements assist in regulating the temperature of the building. For instance, in the test lab, passive heating and cooling are implemented around the perimeter. This involves an unoccupied air chamber around the primarily underground test lab that helps in keeping the air cool, and skylights throughout the perimeter that aid in warming the air up. These elements reduce the workload on the geothermal energy system.
Q: How was the site chosen?
A: Our client and project owner, JST, wanted a heavily forested site located in Farmington Hills close to their local partners. They conducted extensive studies of the land, including the prior inhabitants of the site dating back to the Native American Potawatomi Tribe, as well as the identification of every plant and animal species represented on the parcel. Following the research, it was strategically picked because the property is one of the last forested sites in JST’s target demographic, with natural water features and proximity to JST’s current office.
Q: Do you think this project will act as a “lead by example” with others looking to pursue more environmentally friendly structures?
A: The dream and hope of the entire project team is for this approach to become a trend and be replicated by others moving forward. In fact, we are optimistic that the neighboring 30-acre site will also be used in an environmentally conscious manner. We hope whoever acquires the property will continue honoring the forest and its story.
Q: What are some examples of other Cunningham-Limp projects that are focused on sustainability?
A: JST is one of the sustainable builds that C-L is most known for, but we have extensive experience in implementing sustainable practices in our projects and working in sustainable markets.
In 2005, the State of Michigan made a requirement that any new building had to be LEED-certified, so we built the first LEED-constructed project owned by the State of Michigan, which is occupied by the Department of Environment, Great Lakes, and Energy (EGLE). Additionally, we include adaptive reuse, Energy Star, and required environmental practices as part of our standard project delivery.
We are currently working on two electric vehicle battery testing laboratories in Auburn Hills. Another project that’s been recognized for its sustainable construction is the Commongrounds cooperative project in Traverse City.
Additionally, we recently received a 2023 Project Achievement award from CAM Magazine for our Orion Township Municipal Complex, which had many environmentally sustainable elements. The complex was built new and located to activate an underutilized 77.6-acre site allocated for community amenities and future park space. It also acts as a major trailhead for the Polly Ann Trail, which connects to the statewide Iron Belle Trail, and the building design is eco-friendly and functional, utilizing the natural topography to minimize environmental impact.
Q: What can other builders/developers learn from this project?
A: We’re building more than just a building here. We’re building an ecological campus that’s more conscious about preserving the forested property than the actual buildings, and that’s something I think everyone can learn something from.
Be sure to subscribe to our newsletter for regular updates on sustainable business practices in and around Detroit.
Kim Kisner
- All
- Business
- Community
- Education
- Events
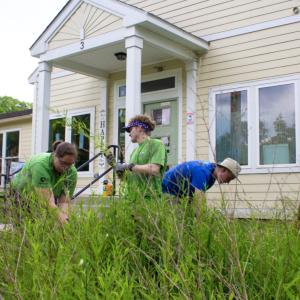
In 2020, the City of Ann Arbor adopted A²ZERO, a climate action strategy designed to achieve community-wide carbon neutrality by 2030. The plan outlines a framework for embedding sustainability into city operations, economic growth, and everyday decision-making, while also emphasizing equity and long-term resilience. One of the most visible efforts under A²ZERO is the Bryant project, a first-of-its-kind initiative to transition an entire neighborhood—home to more than 250...
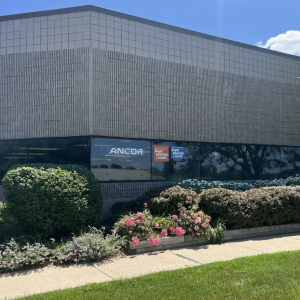
Troy-based Ancor’s roots are in automotive compliance and labeling, but the company has expanded into smart-technology solutions for healthcare, retail, and automotive, including smart battery tracking to stay compliant with local and global regulations. One of its developments is BattCor, a next-generation platform designed to create a real-time “digital twin” of an electric vehicle battery, enabling real-time monitoring, predictive analytics, and improved lifecycle management—from first use through recycling...
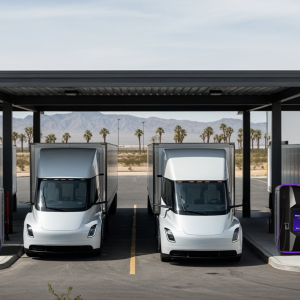
Detroit’s Eastern Market is working to become a national model for integrating freight solutions that reduce fossil fuel use and freight operation costs. San Carlos, Calif.-based ElectricFish, a finalist in the Toyota Mobility Foundation’s Sustainable Cities Challenge, was chosen to build battery-integrated fast chargers to power EVs and provide backup energy for Eastern Market. As one of only three cities worldwide chosen for this challenge, Detroit is using...