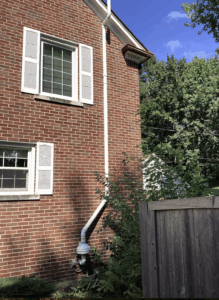
- Kim Kisner
- Business
- 07/23/2024
How a ‘Frunk’ Contributes to Sustainability
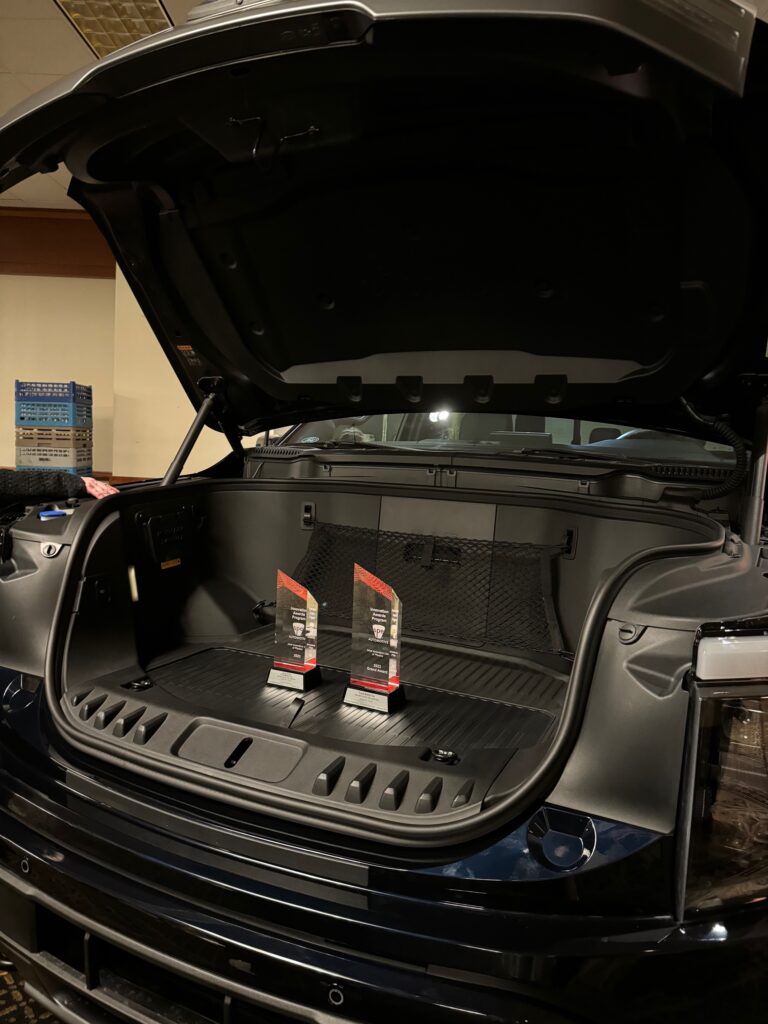
Created in 1973, Cascade Engineering specializes in large-part plastic injection molding.
The second-generation, woman-owned company was recognized at the 2023 Society of Plastics Engineers Automotive Innovation Awards for its work with Ford Motor Co. on the Mega Bin/Frunk for the Ford F-150 Lightning. Frunk is a portmanteau word for a trunk on the front of a vehicle.
In doing so, it converted the front trunk from a compression-molded painted sheet-molding compound to a large Class A composite injection-molded part and is currently one of the industry’s largest injection-molded product pieces.
SBND interviewed Christina Keller, CEO and chair of the Grand Rapids-based Cascade Engineering Family of Cos., about the frunk’s impact on sustainability, creating circular economy solutions, and evolving trends in the industry.
Q: How does sustainability stand out within Cascade Engineering?
A: Cascade is a second-generation family business that is woman-owned and sustainable. We are celebrating 50 years as a triple-bottom-line company.
We are a certified B Corp, ISO 14001 certified and LEED certified.
Our focus is on innovative products and solutions in manufacturing and we supply to the furniture, automotive, and waste industries.
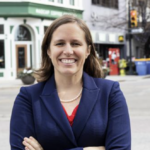
Q: What role does sustainability play in the company?
A: We have been organized as a triple-bottom-line – people, planet, profit – company since our inception. On the people side, we work heavily with returning citizens and also on initiatives to reduce the state of recidivism in Michigan. On the planet side, we’ve been zero waste to landfill since 2012 and have innovated a number of projects in the circular economy.
Obviously, we must be profitable to engage in all these activities.
Q: Can you tell us more about the frunk? I believe this is currently the industry’s largest injection molded product piece. What aspects of this impact sustainability?
A: First, by eliminating the paint process there is a significant reduction of Volatile Organic Compounds (VOCs).
Second, it’s more fuel efficient due to decreased product weight.
Next, the manufacturing process has been streamlined to reduce energy.
And finally, it’s more recyclable in that the end-of-life material can be recycled into a variety of products.
Q: How do you think this impacts Southeast Michigan?
A: The paint process takes place in Ford facilities, so eliminating this directly reduces VOCs in Southeast Michigan.
The collaboration between Cascade and Ford serves as a promising example of potential collaborations between Tier One suppliers and manufacturers in Southeast Michigan.
There are many opportunities for partnerships toward a better environmental outcome.
Q: In what other ways does the frunk’s design and manufacturing process impact sustainability?
A: We have eliminated the environmental burden of paint in the Frunk’s design. Additionally, the secondary routing of holes has been eliminated, reducing process steps and allowing us to produce a higher quantity of parts in less time. The seal interfaces are integrated into the assembly station for further efficiencies, and the material used is recyclable.
Q: The Frunk process utilizes a 4,000-ton injection press and a tool equipped with a 16-drop hot runner system to mold these parts. Is this typical?
A: No. The use of a 4,000-ton injection press is unique in the industry. The capital required to purchase this equipment poses a significant barrier for most companies. Additionally, the specialized human capital needed to operate such a large press is rare.
Q: Is the new frunk product in production?
A: Yes. If you buy a Ford 150 Lightning today you will get one of these pieces in your vehicle. It is fully in production and we are looking at more innovations currently.
Q: What new innovations are you working on?
A: Additional frunks in the near term. Before electric vehicles, we did not have the space in the front of vehicles to create a front trunk. Now, with increased demand for EVs, it’s a growing area and we are looking at manufacturing a number of additional front trunks.
Q: Does being in Michigan in particular post challenges or opportunities in terms of your work on the sustainability front?
A: There is an excellent network of manufacturers in Michigan – especially Southeast Michigan – that allows us to be truly innovative.
A challenge is finding talent. This sector overall currently has 516,000 job openings and over the next decade is projected to reach 3.8 million.
Another challenge we face is incarceration. The U.S. has one of the highest incarceration rates, with 1 in 100 adults in jail.
We see returning citizens as a valuable pool of talent that can be trained and integrated into the workforce. This presents a unique opportunity for Michigan, as the state is not attracting enough new residents, and only 50% of college graduates stay here. Additionally, while college graduates remain in their first job for an average of two years, returning citizens tend to stay for seven years. This approach offers an interesting solution to addressing the talent gap in Michigan.
Q: How do you see industry trends evolving?
A: I see a lot of work in the AI space and Industry 4.0 focused on innovative manufacturing methods. There is a noticeable trend towards reshoring, driven by the constraints observed in the global supply chain during the pandemic. Companies are now striving to establish a local footprint, which also helps reduce the carbon footprint from transportation.
Additionally, significant efforts are being made to maximize package density for more efficient shipping and transportation.
Regarding talent attraction and retention, we have more 65-year-olds in the U.S. than ever before, while our younger demographic is declining.
Q: How is Cascade adapting to the changes in the industry?
A: We are constantly scanning the horizon to look at trends. On the sustainability side, we are developing an ecosystem of recycled plastic sources to enhance our clean stream of recyclable materials.
We are looking at streams from medical waste that could be used, and post-consumer and post-industrial applications.
We are also working on additives to use in our products such as hemp fibers, dust waste, and trash materials.
And finally, we are working with Automation Alley to analyze and understand where we can best benefit from AI and Industry 4.1.
Be sure to subscribe to our newsletter for regular updates on sustainable business practices in and around Detroit.
Kim Kisner
- All
- Business
- Community
- Education
- Events
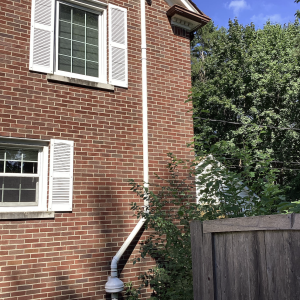
Indoor air quality has become a significant concern for communities across the country, particularly in areas with older infrastructure and a long history of industrial activity. Protect Environmental, a Louisville, Ky.-based company with an office in Ann Arbor, specializes in radon and chemical vapor- intrusion management to help identify and reduce these risks. Its services include testing, system design, and long-term management, with the goal of creating safer...
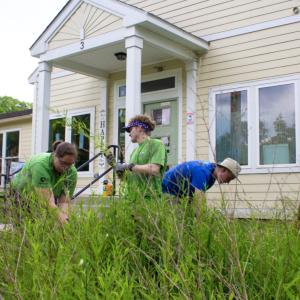
In 2020, the City of Ann Arbor adopted A²ZERO, a climate action strategy designed to achieve community-wide carbon neutrality by 2030. The plan outlines a framework for embedding sustainability into city operations, economic growth, and everyday decision-making, while also emphasizing equity and long-term resilience. One of the most visible efforts under A²ZERO is the Bryant project, a first-of-its-kind initiative to transition an entire neighborhood—home to more than 250...
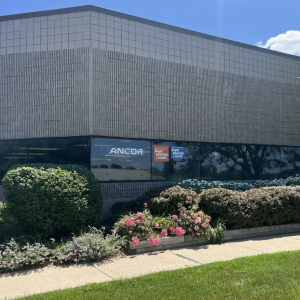
Troy-based Ancor’s roots are in automotive compliance and labeling, but the company has expanded into smart-technology solutions for healthcare, retail, and automotive, including smart battery tracking to stay compliant with local and global regulations. One of its developments is BattCor, a next-generation platform designed to create a real-time “digital twin” of an electric vehicle battery, enabling real-time monitoring, predictive analytics, and improved lifecycle management—from first use through recycling...