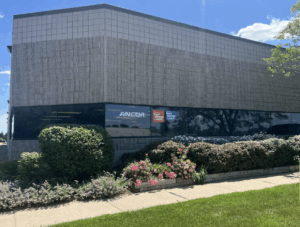
- Kim Kisner
- Business
- 11/15/2022
Processes and Proper Planning Drive Sustainability Practices
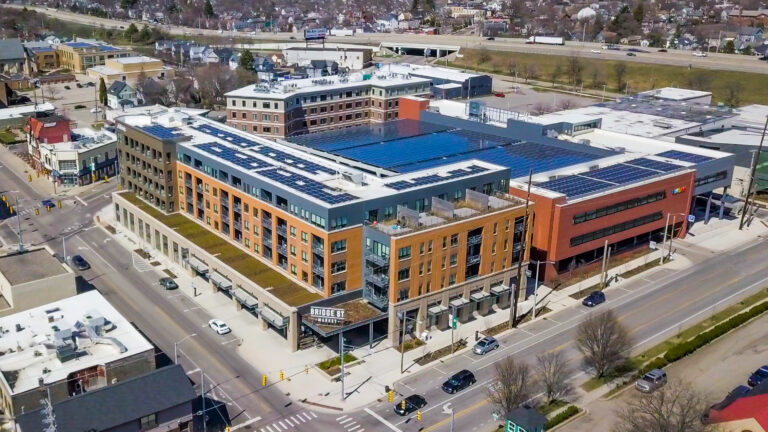
From real estate development to construction and property management, Rockford Construction has been serving the commercial, multiunit, educational, industrial, healthcare, and retail markets throughout the Midwest for more than 30 years.
How do they approach sustainability?
Mike VanGessel, founder and CEO of Rockford Construction, shares that and more with SBN Detroit.
Q: Please tell us about the sustainability practice you have in place.
A: Rockford’s current sustainability efforts reflect a “triple bottom line” that is focused on people, the planet, and profit. We consider ourselves to be good stewards of all three of these finite resources. This is certainly a broader view than many people take, but one that is important to our clients and our communities.
And we’re not just a construction company. We also develop, own, and manage properties, so our focus extends across the full life cycle of space – not just the initial resources during construction, but the total cost of ownership and the impact our buildings make into the future. As a result, our efforts are quite broad. But each building type brings its own set of challenges and opportunities, allowing us to customize our approach and maximize value to our clients.
Q: When did your focus on sustainability come about?
A: Decades ago. Rockford was an early adopter of sustainable construction practices. We knew that buildings were a major driver of energy consumption at that time. As a company committed to delivering value to our clients, we recognized that achieving greater energy efficiency would also decrease long-term costs.
As the sustainability movement evolved and our knowledge of healthy buildings has grown, our efforts have expanded to include things like water conservation, low VOC (volatile organic compounds)-emitting materials, locally sourced and rapidly renewable materials, and more.
Our more-recent triple bottom line approach recognizes that “people” and “profit” are also finite resources, as we’ve seen in our current economy. The shortage of workers – not just in construction but in most industries – has driven a focus on a construction process and end-user facilities that are highly efficient, productive, and attractive to people. The reduction of waste in time and money allows those resources to be deployed elsewhere.
Q: What are some examples?
A: Over the years, Rockford has completed hundreds of projects that are LEED certified or designed to meet certification requirements. But our approach is applied to all our projects, exploring the building design, systems, and materials to determine the right solution based on client needs, first costs, and long-term operational expenses.
The most successful projects result from early involvement and clear goal-setting. One of the best examples can be found in Circuit West, a cutting-edge energy district that encompasses a 13-block area in Grand Rapids. As Rockford was developing and constructing buildings in the area, we partnered with Consumers Energy in their effort to pilot next-generation energy technology. Together, we installed 1,800 solar panels and battery storage capable of producing 500 kilowatts every hour. Power lines were buried, and solar arrays were installed in conjunction with other construction work, greatly reducing installation costs. The result is more reliable, renewable energy for the neighborhood.
While Circuit West was a large-scale effort, early involvement allows us to explore all possibilities, uncovering those that make the greatest impact on our clients’ triple bottom Line.
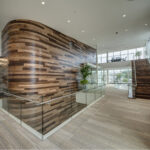
Q: What are the drivers behind these practices?
A: The driver of sustainability is simple. We are creating healthier, more energy-efficient, and cost-effective buildings for our clients and the people who will live, work, play, and heal inside of them.
In the early days, sustainable design and materials were thought to drive additional costs to buildings, and owners had to be deeply committed. Today, a better understanding of good design, appropriate systems, and more readily available sustainable and renewable materials are all driving cost savings. Why a client chooses sustainable solutions – cost savings, environmental responsibility, or healthy spaces – isn’t important. What matters is that the result helps us conserve resources and positively impact our world.
Q: Rockford services so many different industries and types of construction – how do your sustainability practices differ between projects?
A: Each project is unique, and clients have different goals and expectations. That said, best practices can vary based on different project types. For example, some industrial buildings are high users of energy and, at times, water. Energy-efficient systems, water conservation, and grey water options can provide good solutions.
In healthcare facilities, research shows that healing environments include natural light, views, good ventilation, low VOC products, and easily cleaned materials. By focusing on what makes each building unique, the low-hanging fruit of sustainability becomes clear.
Often, the most sustainable building is the one that is renovated, either for its existing use or for a new one. This is particularly true in an urban setting, where many building exteriors were built to last for decades. By reusing the walls and structure, not only are tons of waste materials diverted from landfills, but owners can capture the value of materials already in place.
Warehouses can be converted into apartment buildings, churches become office buildings and schools are reimagined into senior living. Over the years, Rockford has developed expertise in the adaptive reuse of space.
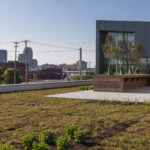
Q: Do you have a team of people set up to implement your sustainability practices?
A: In the past, the Rockford team included a director of sustainability. However, we wanted to turn what could be described as a “program” into a “practice.” Our construction team and our property and facility managers are all well-versed in sustainable practices. But we have a variety of team members, from accountants to graphic designers, who want to be a part of our company-wide efforts. That’s why we are launching a company-wide Sustainability Committee to continue to expand our impact both internally and externally.
Q: Beyond vendors and material choices – what else do you look at?
A: Locally sourced talent, vendors, and materials are part of a strategy that is appealing to our clients, who strive to support the communities in which they live and work. From there, system and material selections are customized to best meet the needs of the facility we’re working in.
Driving a lean and efficient construction process also contributes to more sustainable buildings. Building information modeling (BIM) and proper planning can minimize waste in both materials and labor.
At Rockford, we’re focused on “doing it right the first time.” This may seem like an obvious approach, but it requires sound planning, strong teamwork, clear communication, and technology tools that help keep hundreds of skilled trades workers on the same page during construction. By using these tools effectively, we are driving faster schedules, a higher level of quality, and limited rework to reduce waste.
Q: Are you pleased with the progress and impact you’ve been able to make so far?
A: Sustainability is a journey we are all on, and it continues to grow and evolve. New research and developments expand our knowledge and our options. At Rockford, we’re proud of what we’ve been able to accomplish but remain committed to adopting new technologies and processes that advance the triple bottom line.
Q: What are the biggest challenges?
A: One of the biggest challenges to sustainability in construction is the perception that it costs more. The truth is that when applied correctly, sustainability strategies can save money during construction and long after our work is complete.
The other challenge is that sustainability can feel complex and confusing. Clients can struggle with where or how to start.
Q: What are the most impactful things construction companies can do to make a difference?
A: We think the best way we can make a difference is to drive a culture of sustainability that is simple, understandable, and pervasive. We use the term “conservation” to communicate our efforts. Conserving energy, natural materials, labor, and financial resources is something everyone understands. When we involve our clients, our design and trade partners, and our Rockford team members, the best outcomes are achieved.
Be sure to subscribe to our newsletter for regular updates on sustainable business practices in and around Detroit.
Kim Kisner
- All
- Business
- Community
- Education
- Events
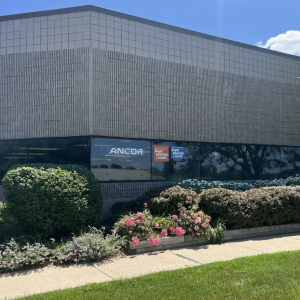
Troy-based Ancor’s roots are in automotive compliance and labeling, but the company has expanded into smart-technology solutions for healthcare, retail, and automotive, including smart battery tracking to stay compliant with local and global regulations. One of its developments is BattCor, a next-generation platform designed to create a real-time “digital twin” of an electric vehicle battery, enabling real-time monitoring, predictive analytics, and improved lifecycle management—from first use through recycling...
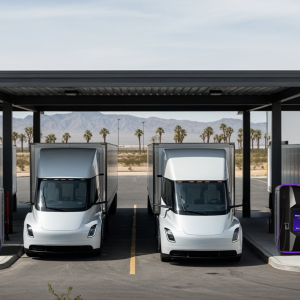
Detroit’s Eastern Market is working to become a national model for integrating freight solutions that reduce fossil fuel use and freight operation costs. San Carlos, Calif.-based ElectricFish, a finalist in the Toyota Mobility Foundation’s Sustainable Cities Challenge, was chosen to build battery-integrated fast chargers to power EVs and provide backup energy for Eastern Market. As one of only three cities worldwide chosen for this challenge, Detroit is using...
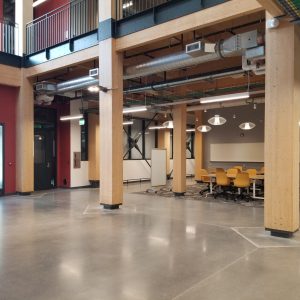
MassTimber@MSU is a cross-disciplinary initiative at Michigan State University dedicated to advancing mass timber construction and manufacturing in Michigan. Collaborating with partners across construction, forestry, development, and state agencies—including the Michigan Department of Natural Resources—the initiative leverages MSU’s land-grant mission through research, teaching, stakeholder engagement, and policy development to build a sustainable mass timber future for the state. SBN Detroit interviewed Sandra Lupien, Director of MassTimber@MSU, about the...