
- Kim Kisner
- Education
- 03/14/2023
MSU’s Industrial Assessment Center Employs Students to Provide Free Assessments to Support Energy and Sustainability Goals for Businesses and Commercial Buildings
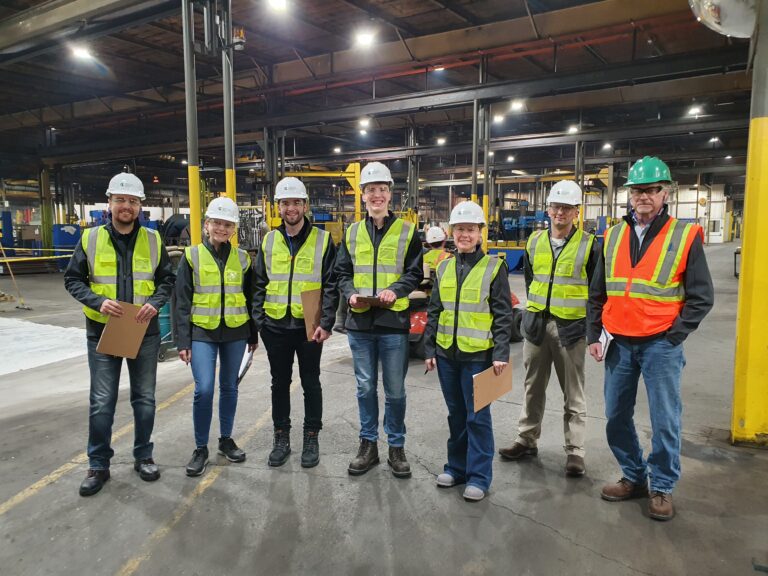
The Industrial Assessment Center (IAC) at Michigan State University, in collaboration with Michigan Technological University and Henry Ford College, offers the 6,200+ small and medium manufacturers (SMEs) in Michigan free technical assessments to help save energy, improve productivity, reduce waste, and reduce carbon emissions.
As a result, the institutions are helping to build and expand a knowledgeable and diverse energy workforce pipeline.
The scope of topics covered includes:
– Energy and water savings
– Smart manufacturing
– Energy management
– Cybersecurity
– Resilience planning
– Decarbonization
– Electrification
SBN Detroit spoke to Dr. Kristen Cetin, associate professor at MSU in the Department of Civil and Environmental Engineering. She also is the director of the MSU Industrial Assessment Center.
Q: Tell me about the Industrial Assessment Center
A: We are a U.S. Department of Energy-funded center focused on two things:
First, we support small and medium-sized manufacturers and commercial building owners by providing one-day no-cost assessments to identify opportunities to improve and support their energy and sustainability goals.
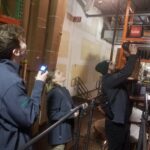
Our second focus is workforce development. Once students graduate they take manufacturing and sustainability and energy knowledge into the workforce. Some students will go on to jobs in manufacturing or energy, and others perhaps not, but will know to integrate what they’ve learned in whatever career they pursue.
We are one of 37 IAC centers across the country, and ours is a collaboration between Michigan State University, Michigan Tech, and Henry Ford College.
Q: How did the IAC come to be?
A: The Department of Energy program has been in existence since the ‘70s to support energy efficiency, and every five years they do a funding call. That’s where it began.
Michigan has not had an IAC for about six years. I moved here from Iowa and was surprised that this manufacturing-rich area did not have an IAC providing this service.
So, when the funding call came out we applied for Topic 1, which is the manufacturing side, and Topic 2, which is the commercial building side, pilot program. We knew MSU alone couldn’t easily support all regions of Michigan given how big Michigan is. Michigan Tech is surrounded by important and different industries, so they were a natural collaboration to support the northern part of the state.
Collaborating with Henry Ford College as a community college helps us to support the Detroit area, as well as to better reach more commercial buildings. This collaboration also enables broader diversity of students to participate in terms of training.
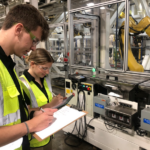
So we partnered, and it’s been going very well to date.
Q: What does the assessment process involve and how much support do you offer outside of the assessment?
A: The assessment process begins with a thorough analysis of utility bills, followed by a one-day in-person assessment. Sometimes we leave datalogger equipment to continue to monitor the operation of energy-consuming systems after the assessment. Once the assessment and analysis are complete a full report is written up including detailed recommendations, estimates of energy efficiencies, and associated costs.
We then follow up about a year after the assessment to see what was implemented, if there were efficiencies gained, and receive feedback on what was actionable and what was not. This helps us figure out what we can do better and what kind of impact each assessment has made.
In terms of supporting the implementation of our recommendations, we do a few things. If appropriate we contact utility companies to see if there are rebates or incentives that fit well.
We also connect interested companies to the Better Plants program, which can help facilitate larger-scope initiatives and provide ongoing support beyond our assessments.
And finally, a new development that is just becoming available is a matching grant program to support any company that completes the assessment. Part of the Bipartisan Infrastructure Law implementation, this is a new grant that will match company funds to support implementation of the changes recommended in the post-assessment report.
Q: Are all assessments the same or do they vary depending on the building?
A: We typically have one day to do them, so to that end we follow a similar schedule and format. But our recommendations and areas of focus vary depending on what kind of manufacturing the company is doing, or what kind of commercial building it is. We do a walk-through in the morning and obtain information about all of their systems in place. At lunch, we brainstorm about areas of improvement, and then we split into groups to dive deeper into those areas throughout the afternoon.
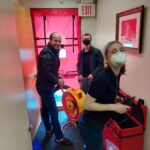
Q: How many assessments are done annually?
A: We do 30 assessments per year, approximately 20 of which are manufacturers and ten commercial buildings.
Q: What is the role of the students?
A: This is very much a student-led program. Students are the main point of contact with each of the companies we work with, the lead in the discussions, the lead in data collection, and all aspects of the program.
There is a student lead for each assessment, and that person is in charge of setting up the logistics and takes the lead during the assessment. They also present the report and recommendations to the companies we work with. They also lead the student group in creating the report draft review, which is then reviewed and approved before sharing with the company. The faculty and staff in the IAC help to support and generate ideas, provide technical expertise, as well as review recommendations and overall reports.
Our student groups range from approximately three to eight per assessment. Approximately 90% of the students are undergraduates from a variety of engineering and non-engineering backgrounds. There is also a three-credit training course that students in the IAC take during their first semester in the program. All students are paid for the work they do, including training.
Q: What does it mean to have this practical hands-on experience?
A: I think this hands-on training is even more valuable than taking classes. It’s invaluable – this targeted learning that is also meaningful work.
The amount of growth we see in students over a semester and over a year is like they’ve worked a full-time job and the level of maturity gained is remarkable.
I wish I had had the opportunity to do it when I was a student.
Q: How do you think the IAC brings value to businesses you work with?
A: I think one of the most valuable things that we bring is fresh ideas and also the new ideas generated when different people come together from businesses that do not normally have the opportunity to work together.
For example, a head of operations and a machine operator walking the plant floor together, discussing where there are operational challenges, where efficiencies can be found, and how sustainability can be elevated is something that doesn’t happen every day. We bring those opportunities and new sets of eyes to the current operations and can help lead those connections and discussions for some great outcomes.
Q: What is the future of the program?
A: We’ll see new things due to the infrastructure bill, such as more funding for the implementation of assessment recommendations through matching grant funding. I think this will have a trickle-down effect, and we’ll be able to enhance the program in different ways. It’s an exciting time and I’m looking forward to seeing where it goes, and the differences we can make when it comes to sustainability, energy savings, and decarbonization.
Be sure to subscribe to our newsletter for regular updates on sustainable business practices in and around Detroit.
Kim Kisner
- All
- Business
- Community
- Education
- Events

ZF Group, a global technology company with its North American headquarters in Northville, specializes in systems for passenger cars, commercial vehicles, and industrial technology. With a focus on next-generation mobility, the company develops solutions that address electrification, automation, and digitalization while aiming to improve safety, efficiency, and sustainability in transportation. SBN Detroit interviewed Anuj Shah, Sustainability Lead, for the Americas, to explore the most pressing environmental challenges in...

The Chip Bag Project, based in Detroit, is a sustainability initiative that upcycles hard-to-recycle snack packaging — particularly chip bags — into insulated sleeping bags for individuals experiencing homelessness. Founded by Eradajere Oleita, the project addresses both environmental waste and housing insecurity by transforming materials like Mylar into practical, thermally efficient solutions. In June, Oleita was among Trelllis’s 30 Under 30, its annual recognition of the brightest young...

PowerPanel, headquartered in Oxford, focuses on sustainable energy technology with a particular emphasis on hot water systems and thermal energy capture. The company designs and manufactures modular solar hybrid systems that integrate both photovoltaic and thermal components into a single unit. Its goal is to offer energy solutions that are more efficient, durable, and economically viable for a range of commercial and industrial applications. SBN Detroit interviewed Garth...